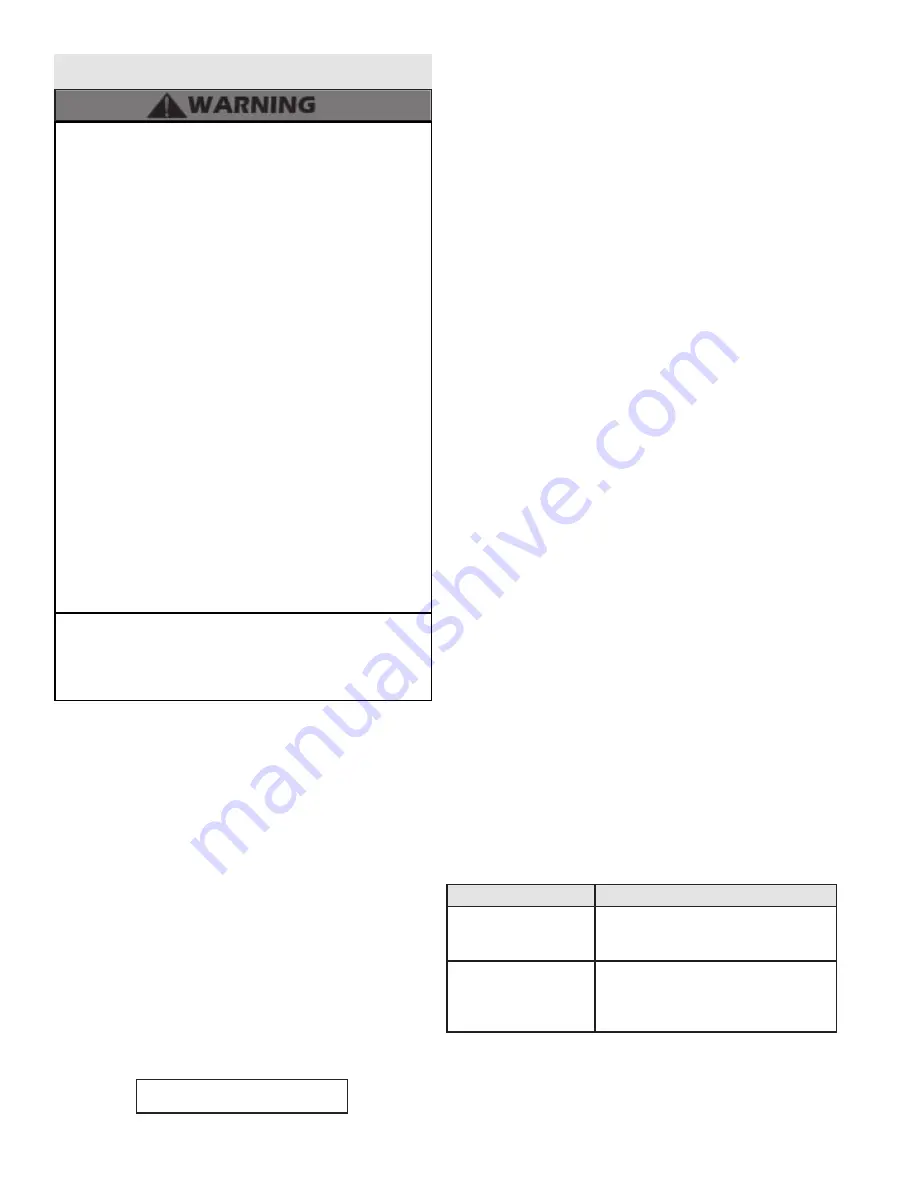
lp-445-r4 Rev. 006 Rel. 027 Date 7.21.20
42
Part 10 - Start-Up Procedure
FOR YOUR OWN SAFETY READ BEFORE OPERATING
1. This boiler does not have a pilot. It is equipped with an ignition
device which automatically lights the burner. Do not try to light
the burner by hand.
2. BEFORE OPERATING: Smell all around the boiler area for gas. Be
sure to smell next to the floor because some gas is heavier than air
and will settle on the floor.
3. WHAT TO DO IF YOU SMELL GAS
• Do not try to light any boiler.
• Do not touch any electric switch, do not use any phone in
your building.
• Immediately call your gas supplier from a neighbor’s phone.
Follow the gas suppliers’ instructions.
• If you cannot reach your gas supplier, call the fire
department.
• Turn off the gas shutoff valve (located outside the boiler) so
that the handle is crosswise to the gas pipe. If the handle
will not turn by hand, don’t try to force or repair it, call a
qualified service technician. Force or attempted repair may
result in a fire or explosion.
4. Do not use this boiler if any part has been under water.
Immediately call a qualified service technician to inspect the
boiler and to replace any part of the control system and any gas
control that has been damaged.
5. The boiler shall be installed so the gas ignition system
components are protected from water (dripping, spraying, rain,
etc.) during boiler operation and service (circulator replacement,
condensate trap, control replacement, etc.)
Failure to follow these instructions could result in property
damage, serious personal injury, or death.
A. Control Overview
The control is one of the primary safety devices of the boiler. It
monitors the safety sensors of the boiler to assure safe and efficient
operation.
The control has many features associated with system design. This
section addresses programming features, including Boiler Settings /
System Settings / Maintenance Settings and System Diagnostics, to
help in customizing your control. It is important to fully understand
control capabilities before customization, as its factory defaults may
already fit your system design and not require any adjustment at all.
If you discover any evidence of a gas leak, shut down the boiler
at once. Find the leak source with a bubble test and repair
immediately. Do not start the boiler again until the leak is repaired.
Failure to comply could result in substantial property damage,
severe personal injury, or death.
B. Navigation of the Display
The display includes a two line backlit LCD readout to provide
informative messages about the operation of the boiler. Many
operating parameters can be viewed and adjusted by using the six
buttons on the display. The function of each button is described
below.
RESET
– The RESET button has two functions.
– Resets any lockout error code
– Returns the user to the default display screen.
ENTER
– The ENTER key is used to access parameter programming
mode. To access this mode, hold down the ENTER key for more than
4 seconds. The readout will change to:
ENTER MENU CODE
000
One of the zeroes will be blinking. Use the
^ v
arrow keys to change the
blinking digit to the correct value. Use the
< >
arrow keys to select the
next digit to change and again use the
^ v
keys to change the value.
Repeat until the correct code is entered. Press the
ENTER
key to accept
the code entered. If the code is correct, the readout will change to
the appropriate screen. If the programming code is not accepted, the
readout will continue to display as shown above.
ENTER
is also used to enable a function for editing. After the user
navigates to the desired function, the user holds down
ENTER
for one
second. When
ENTER
is released, the function value will begin to blink.
The function can now be changed using the
^ v
keys. After the new
value is displayed, the user then presses
ENTER
for 1 second to lock the
new value of the function. The value will then stop blinking.
LEFT AND RIGHT ARROW KEYS
–
< >
are used to navigate between
the default display, status display, analog and cascade displays if they
are enabled. The
< >
keys are also used in programming modes to
change between programmable functions. It is recommended you
use the Menu Maps in the back of this manual and the detailed menu
instructions printed in this section to help in menu navigation.
UP AND DOWN ARROW KEYS
–
^ v
are used to navigate between the
various functions displayed in the menu. After the function is enabled
for editing by pushing the
ENTER
key, the
^ v
keys are used to adjust
the function upward or downward to the desired value.
C. Operating Instructions
Before operating the unit, it is important to remove the cover and
verify that the gas line and water lines are connected to boiler and fully
purged. If you smell gas, STOP; Follow the safety instructions listed in
the first part of this section. If you do not smell gas, follow the next
steps.
1. Turn down the thermostats before applying power to the boiler. If
0–10 volt or other inputs are used, make sure that they are set so there
is no call for heat while programming.
2. Turn on the power to the boiler or boilers if a cascade system used.
3. Next, check the boiler settings. Adjustment and factory defaults are
outlined within this section. If a cascade system is used, it is important
that all the boilers have the same boiler settings.
4. Next, check the system settings. Adjustments and factory defaults are
outlined within this section. If a cascade system is used, it is important
that the Master Boiler is programmed with the correct system settings.
5. Create a demand on the boiler or boilers if a cascade system is
used. The user can monitor system functions when the boilers are
operational.
6. If the boilers fail to start, refer to the troubleshooting section in the
back of this manual.
D. Programming Boiler Settings
Boiler Setting Program Access
Note: Programming the boiler control is not possible when the boiler
is firing. Make sure any input which can create a demand on the boiler,
such as the tank thermostat, is turned off, so the boiler will remain idle
to allow programming.
Screen
Description
ENTER MENU CODE
000
To access the boiler setting program,
press and hold
ENTER
for 4 seconds until
the display shows the screen at left.
ENTER MENU CODE
600
Use the arrow keys to log in the
Boiler
Menu Access Code - 600
. Press
ENTER
to
confirm the code and access the
Boiler
Setting Program
navigation menu.
Table 16 - Boiler Setting Access
Содержание MODCON500 FS
Страница 34: ...lp 445 r4 Rev 006 Rel 027 Date 7 21 20 34 Figure 26 Cascade Master and Follower Wiring ...
Страница 61: ...lp 445 r4 Rev 006 Rel 027 Date 7 21 20 61 Figure 34 Water Side Replacement Parts All Models ...
Страница 62: ...lp 445 r4 Rev 006 Rel 027 Date 7 21 20 62 Figure 35 Cabinet Replacement Parts All Models See Table ...
Страница 65: ...lp 445 r4 Rev 006 Rel 027 Date 7 21 20 65 Maintenance Notes ...