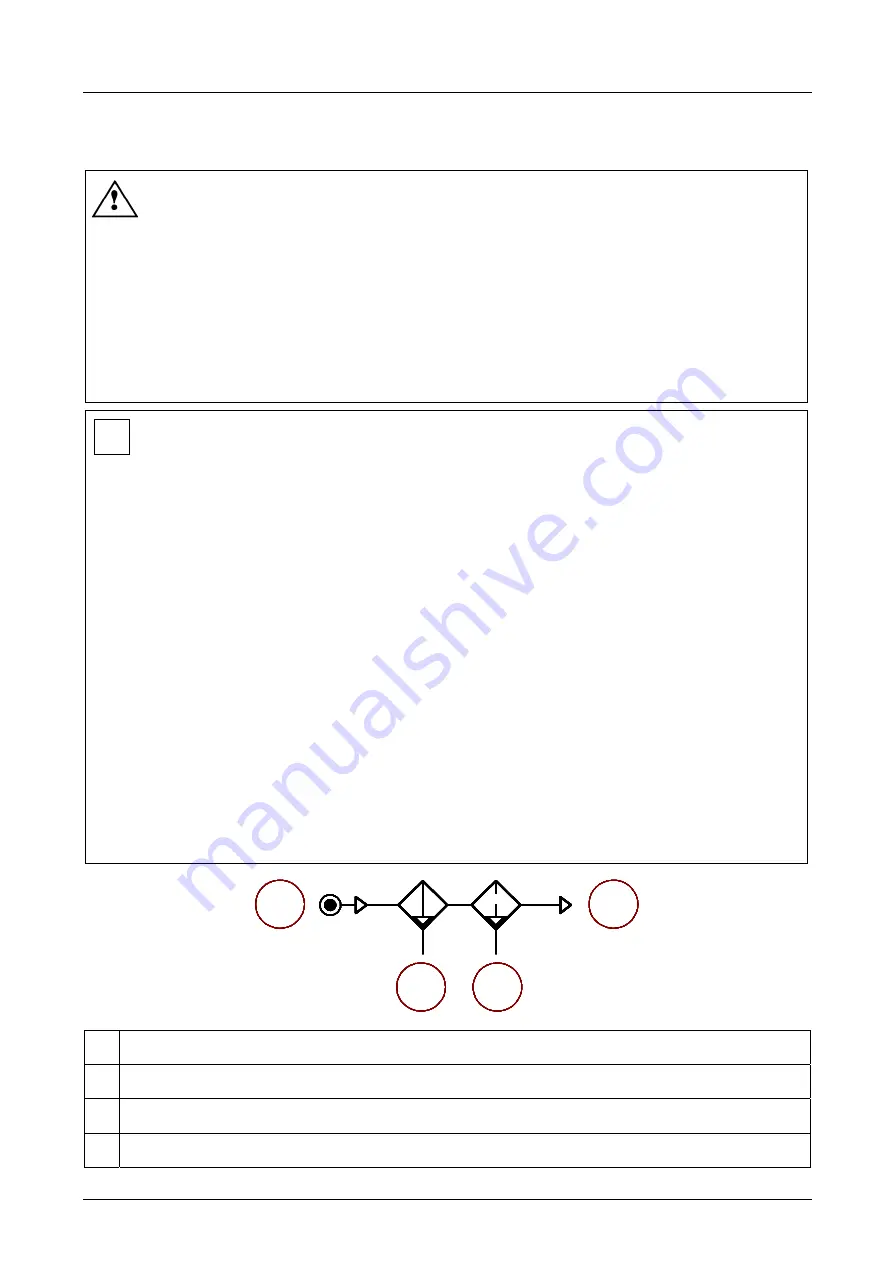
HSD
5801H0056
_______________________________________________________________
71/181
4.4 PNEUMATIC CONNECTIONS
4.4.1 Air purity
IMPORTANT:
Introduce in the electrospindle compressed air of a purity in
accordance with ISO 8573-1, classes 2, 4, 3, i.e:
•
class 2 for the solid particles:
solid particle size < 1 µm;
•
class 4 for the humidity:
dew-point < 3°C (37.4°F)
•
class 3 for the total oil:
concentration of oil < 1 mg / m
3
Failure to comply with these specifications may result in product malfunction.
The guarantee is not valid if pollutants are found during repair operations.
i
As an example, the above-mentioned specifications can be implemented by following the
indications below:
•
If a lubricated air circuit is present in the machine, it should be isolated from the dry air
circuit (to be used by the electrospindle) by means of non-return valves.
•
The filters indicated in this section should be installed as near the electrospindle as
possible.
•
taking into account the fact that the efficiency of the filters is <100%, it is essential that
the machine be fed with properly treated air;
As a general guide, introduce (into the circuit indicated in this section) compressed air
with a purity rating complying with ISO 8573-1, classes 7, 6, 4, i.e.:
o
Type 7 for solid particles:
solid particle size < 40 µm;
solid particle concentration < 10mg/m
3
;
o
class 6 for the humidity:
dew point < 10°C;
o
class 4 for the total oil:
oil concentration < 5 mg/m
3
;
•
at the end of the working day, empty the pneumatic system to enable the automatic
purging of filters;.
•
Carry out regular maintenance operations of the filters according to the manufacturer's
indications, and replace them when they are saturated and lose effectiveness
(approximately every 6/12 months).
3
2
1
4
3
2
1
4
3
2
1
4
3
2
1
4
3
2
1
4
3
2
1
4
3
2
1
4
3
2
1
4
3
2
1
4
3
2
1
4
3
2
1
4
3
2
1
4
1
Mains power supply.
2
Pre-filter 5 µm.
3
De-oiling filter 0.1 µm.
4
To the HSD product.