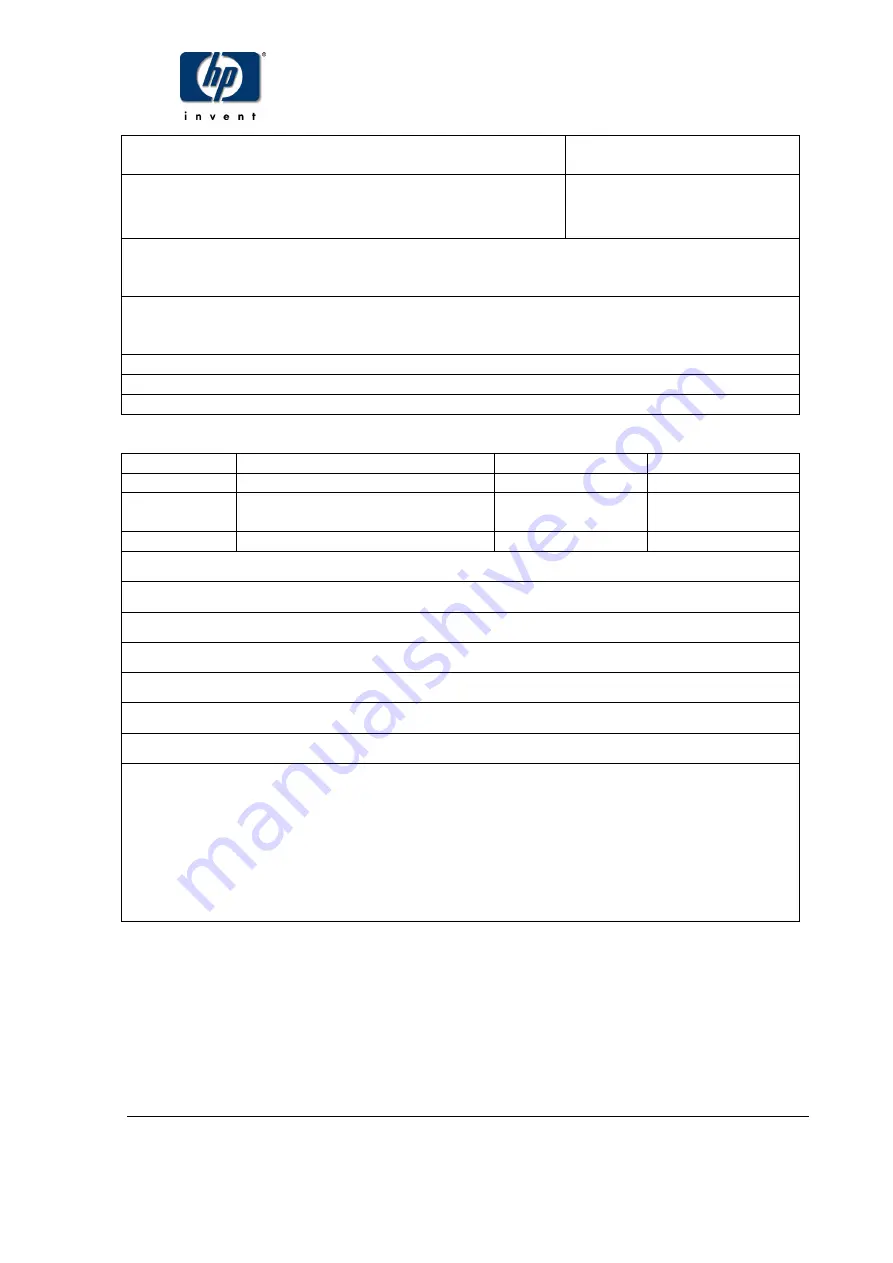
filename: CA293-00600.doc
page 1 of 221
hp indigo field change order
kit p/n:CA292-00550
HP Indigo press ws4000 Cluster 1
procedures
doc p/n: CA293-00600
This document applies to the following products/serial numbers:
HP Indigo press ws4000 serial nos. 2210002-22100122 & 110001
This document applies to the following parts/assemblies:
Cluster 1 assemblies
Software affected:
⌧
yes
no
Type of change:
mandatory
⌧
partial
conditional
Supporting
ECO:
configuration control
Revision Description
Release
date Reviewer
00
Initial release
15 Jan 04
Yossi Bahar
01
Press software installation only
option
15 Mar 04
Yossi Bahar
Responsible reviewer:
Meir Kormian
NameHaim
signature
date
R&D reviewer:
Haim Belinkov
Name
signature
date
Engineering reviewer:
Ron Levkovits
Name
signature
date
Group manager:
Aaron Lubelski
Name
signature
date
Documentation manager:
Ronit Shugal
Name
signature
date
Written by:
Asher Reichert
Name
signature
date
Configuration control:
Charles Margy
Name
signature
date
Hewlett-Packard Company, Indigo Division, P.O. Box 150
Kiryat Weizmann, P.O. Box 150, Rehovot 76101, Israel
©Copyright Hewlett-Packard Company, 2003. All rights reserved.
CONFIDENTIALITY NOTICE
This document contains valuable trade secrets and confidential information of Hewlett-Packard Company. Nothing herein
may be copied, reproduced or distributed in any form or medium, or disclosed to any third party in any manner, without prior
written authorization of Hewlett-Packard Company. The copyright notice, which appears in this document, is purely
precautionary and shall not be deemed to constitute publication or intent to publish, in whole or in part.