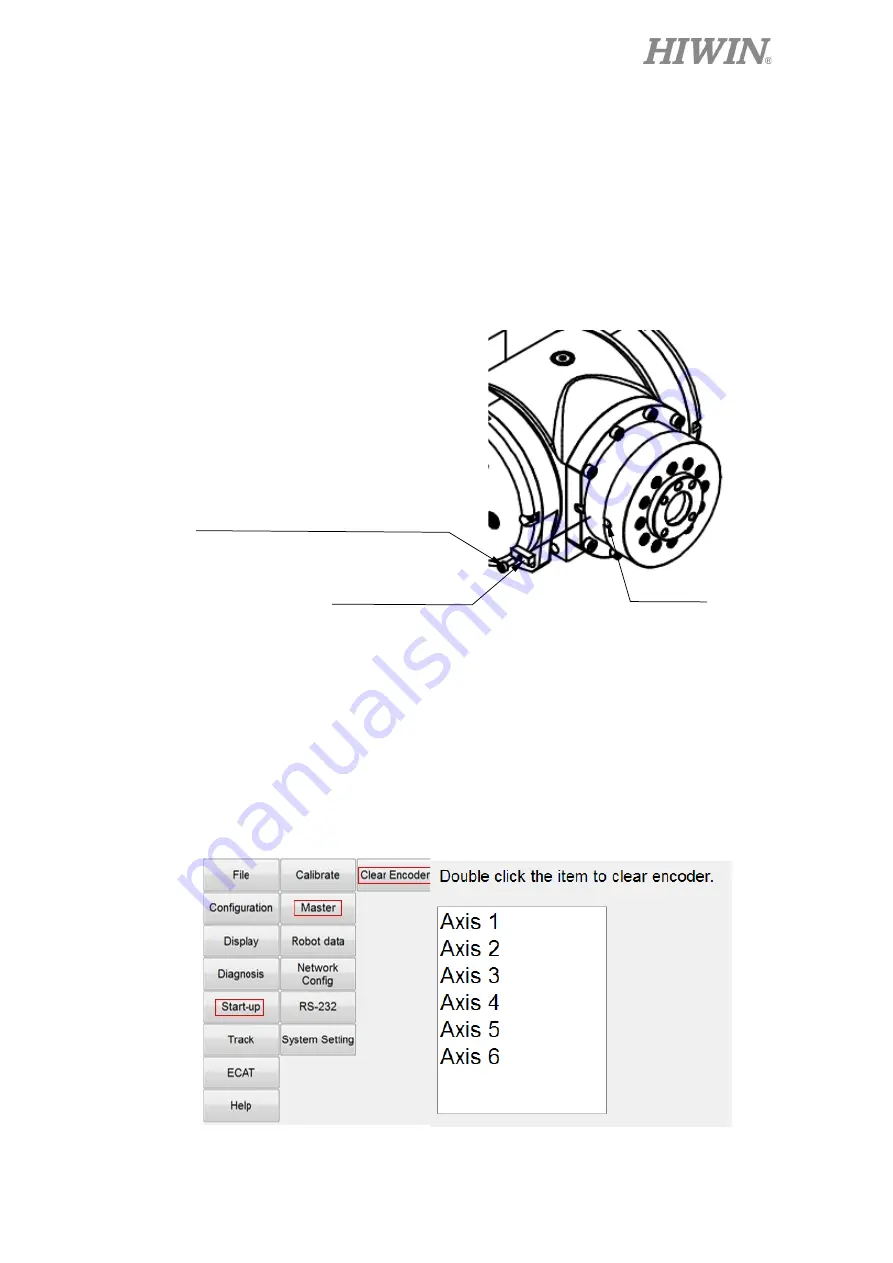
50
C13UE001-1903
J6-axis Zero-position setting
Step1.
Operate J6 at low speed to align the calibration mark with the keyway.
Step2.
Insert the calibration tool(B) to the keyway to calibrate Zero-position. (The
hexagon socket screw can be secured to the calibration tool(B) in advance.)
Step3.
Finish calibration and remove the calibration tool(B) by using the hexagon
socket screw.
Step4.
Clear encoder by HRSS. (Refer to page 53)
Step5.
Zero-position setting of J6 axis is completed.
Figure 4-7 Illustration of J6-axis Zero- position setting
Clear encoder by HRSS
Step1.
Select the “JOINT” as the coordinate system.
Step2.
Move the robot to the Zero-position. (Refer to section 4-1)
Step3.
Click Main Menu>>Start-up>>Master>>Clear Encoder. (As shown in
Figure 4-8)
Step4.
Double click the axis to clear encoder. (As shown in Figure 4-8)
Figure 4-8 Clear encoder by HRSS
Calibration tool(B)
Keyway
Hexagon socket head cap screw
M3
×
0.5P
×
8L(Nylok)
Содержание RA610-GB Series
Страница 1: ...www hiwin tw User Manual Articulated Robot RA610 GB RT610 GB Original Instruction...
Страница 20: ...18 C13UE001 1903 Figure 1 4 e Eye bolt securement Sling installation position 2 M12 Eyebolt...
Страница 37: ...35 C13UE001 1903 Figure 2 4 b RA610 1476 GB Wrist moment diagram RT610 1476 GB Wrist moment diagram...
Страница 38: ...36 C13UE001 1903 Figure 2 4 c RA610 1672 GB Wrist moment diagram RT610 1672 GB Wrist moment diagram...
Страница 39: ...37 C13UE001 1903 Figure 2 4 d RA610 1869 GB Wrist moment diagram RT610 1869 GB Wrist moment diagram...
Страница 55: ...53 C13UE001 1903 Corresponding manipulator model name 1 RA605 XXX GB RT605 XXX GB 2 RA610 XXXX GB RT610 XXXX GB...
Страница 56: ...54 C13UE001 1903 5 3 Operation Name descriptions of the manual brake release device and their functions...
Страница 61: ...59 C13UE001 1903 Table 6 3 Inspection schedule...