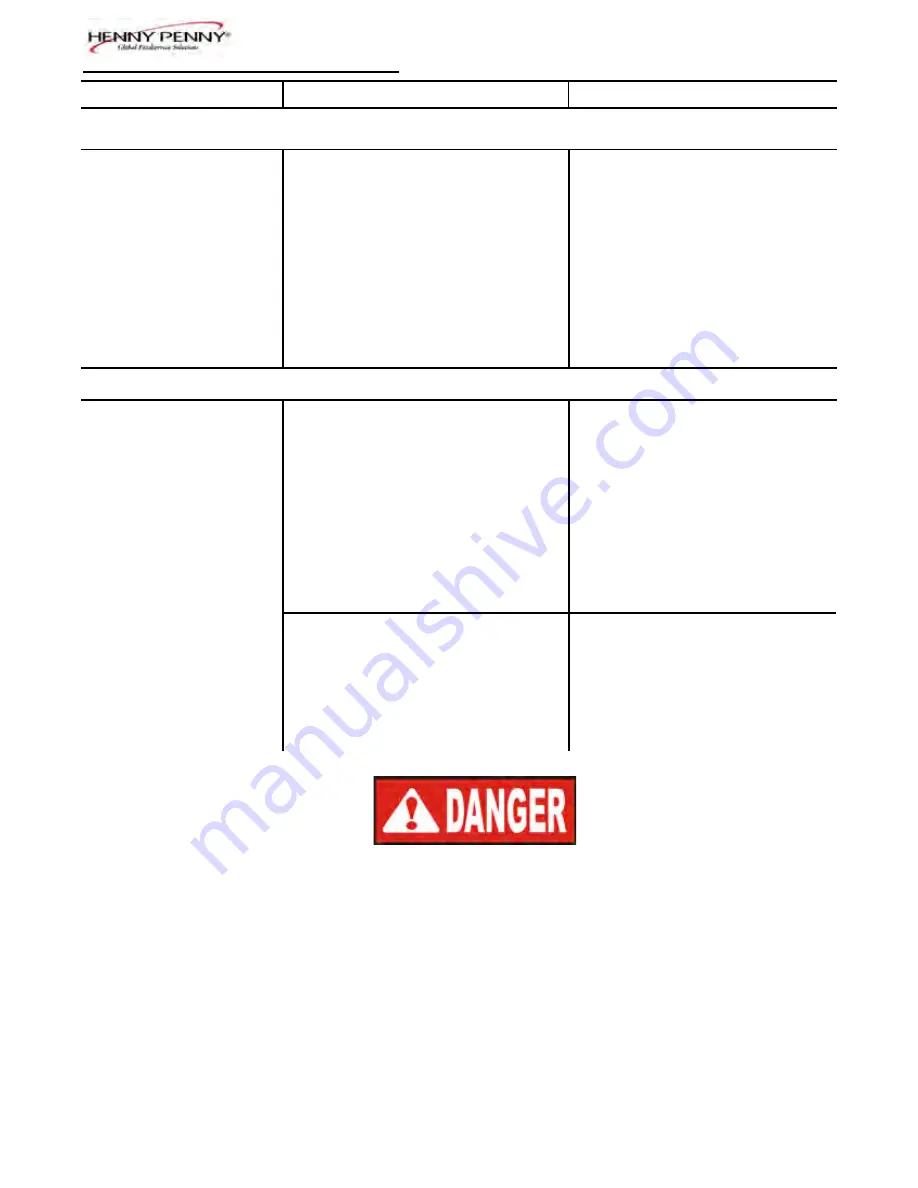
Model 691
1-6
Problem
Cause Correction
POWER SECTION
With switch in
•
Open circuit
•
Check to see that unit is
POWER position,
plugged in
the fryer is completely
•
Check the breaker or fuse
inoperative
at supply box
(no power)
•
Check voltage at wall
receptacle
•
Check POWER switch;
replace if defective
•
Check cord and plug
PRESSURE SECTION
Pressure will not
•
Exhaust line from solenoid
•
Turn unit off and allow
exhaust at end of
valve to exhaust tank
fryer to cool to release
cook cycle
clogged
pressure from frypot;
clean all pressure lines,
exhaust stacks, and exhaust
tank
•
Solenoid valve clogged
•
Check and clean solenoid
valve
Operating
•
Deadweight clogged
•
Turn unit off and allow
pressure too high
fryer to cool to release
pressure from frypot;
remove deadweight and clean
•
Exhaust line to stack clogged
•
Clean exhaust line to stack
DO NOT OPERATE UNIT. IF HIGH PRESSURE CONDITIONS EXIST, SEVERE
INJURIES AND BURNS WILL RESULT. PLACE THE POWER/PUMP SWITCH IN THE
OFF POSITION IMMEDIATELY. RELEASE THE PRESSURE BY ALLOWING UNIT TO
COOL. THE PRESSURE WILL THEN DROP. DO NOT RESUME USE OF UNIT UNTIL
CAUSE OF HIGH PRESSURE HAS BEEN FOUND AND CORRECTED.
1-3. TROUBLESHOOTING (Continued)
Sept. 2004
Содержание PFG-691
Страница 1: ...Henny Penny Pressure Fryer Model PFG 691 TECHNICAL MANUAL...
Страница 2: ......
Страница 52: ...Model 691 2 34 SN FH001JC ABOVE Aug 2004...
Страница 53: ...Model 691 2 35 SN FH001JC ABOVE Aug 2004...
Страница 54: ...Model 691 2 36 SN FH001JC ABOVE Aug 2004...
Страница 55: ...Model 691 2 37 BELOW SN FH001JC March 2004...
Страница 56: ...Model 691 2 38 BELOW SN FH001JC March 2004...
Страница 57: ...Model 691 2 39 BELOW SN FH001JC March 2004...
Страница 58: ...Model 691 2 40 BELOW SN FH001JC March 2004...
Страница 60: ......
Страница 62: ...Model 691 3 2 FIGURE 3 1 FRAME COVER ASSEMBLY Oct 2004...
Страница 68: ...Model 691 3 8 FIGURE 3 6 LID COVER ASSEMBLY March 2007...
Страница 70: ...Model 691 3 10 FIGURE 3 7 DRAIN PAN FILTER ASSEMBLY Aug 2010...
Страница 72: ...Model 691 3 12 FIGURE 3 8A FILTER PUMP ASSEMBLY SN LH028JC BELOW Aug 2010...
Страница 74: ...Model 691 3 14 FIGURE 3 8B FILTER PUMP ASSEMBLY SN LH029JC ABOVE Oct 2004...
Страница 77: ...Model 691 3 17 FIGURE 3 10 GAS BURNER ASSEMBLY May 2005...
Страница 79: ...Model 691 3 19 FIGURE 3 11 GAS PIPING CONTROLS Dec 2009...
Страница 84: ...Model 691 3 24 FIGURE 3 15 DEADWEIGHT SOLENOID ASSY SN AP0802029 ABOVE Aug 2010...
Страница 87: ...Model 691 3 27 FIGURE 3 16B STEAM BOX HOSE ASSEMBLY SN AP0802028 BELOW Aug 2010...
Страница 89: ...Model 691 3 29 FIGURE 3 17 FLUE ASSEMBLY BLOWER SN AP0802028 BELOW Dec 2009...
Страница 93: ...Model 691 3 33 FIGURE 3 18 SOLENOID VALVE ASSEMBLY Sept 2005...
Страница 95: ...Model 691 3 35 FIGURE 3 19 FRYPOT DRAIN PIPING Oct 2008...
Страница 97: ...Model 691 3 37 FIGURE 3 20 LIFT BEAM SHROUDS SN AP0802028 BELOW Aug 2010...
Страница 99: ...Model 691 3 39 FIGURE 3 21 COUNTERWEIGHT PULLEY SYSTEM SN AP0802028 BELOW Aug 2010...
Страница 124: ...Inspection 4 Rev A 1219 US 35 West P O Box 60 Eaton OH 45320 937 456 8400 Fax 937 456 8402 www hennypenny com...
Страница 139: ...Inspection 12 Rev A...
Страница 140: ...Inspection 12 Rev A...
Страница 141: ...Inspection 12 Rev A...
Страница 144: ...Inspection 15 Rev A...
Страница 145: ...Inspection 16 Rev A...
Страница 146: ...Inspection 16 Rev A...
Страница 159: ...Inspection 24 Rev A Figure 2 1...
Страница 160: ...Inspection 24 Rev A Figure 2 2...
Страница 183: ......