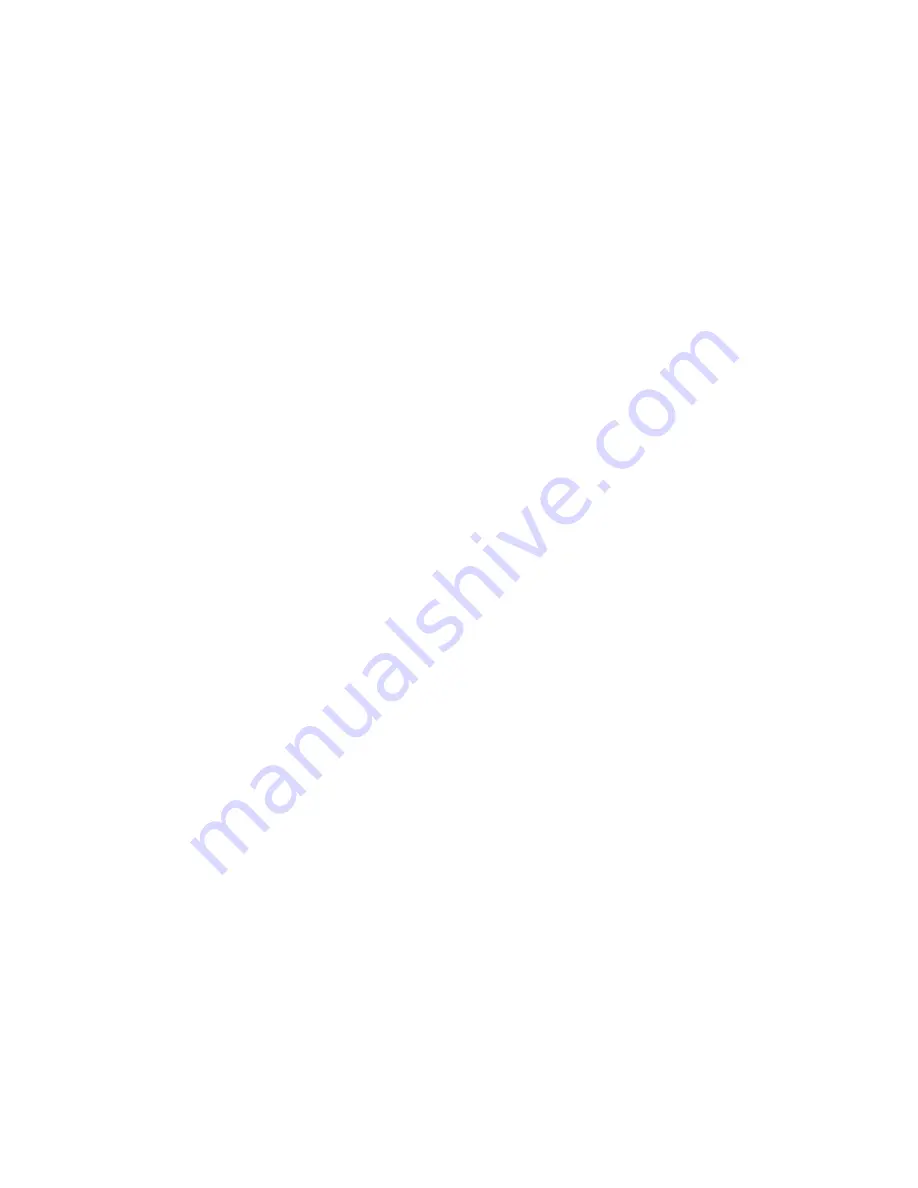
HAMWORTHY HEATING LTD
WARMWELL
500001091/F
8.3
For low gas pressure switch (Propane boilers)
cut LK9.
9)
Ensure pressure switch sensing tubes are
correctly fitted, without twists or kinks. Refer to
Figure 2.2 (p4) for provisional (factory set) pressure
switch settings. Refer to Figure 11.5 (p28) for
pressure switch locations.
11.6 Procedure for Initial Lighting
Ensure gas service cock is in the "off" position.
Press the control thermostat knob to switch ‘on’ the
boiler. Press lockout button on fascia to re-set timer
(wait at least 15 seconds before pressing again if
lockout neon does not go out. After a delay the HSI
neon should illuminate on the fascia and the igniter
should be visible through the viewing port on the
burner front plate. As the gas service cock is
closed, the controls should go to lockout after
approximately 3 seconds (amber neon on fascia lit).
If the above occurs correctly, open service cock and
press reset button on fascia.
After a delay, the ignition should be visible and the
main gas valve should energise, lighting the main
burner. Turn the control thermostat to the required
flow temperature.
NOTE!
The multi-meter should
be reading at least 1µA.
11.7 Gas Pressure Adjustment and Combustion
Checks
After the boiler has operated for approximately 10
minutes, press the control thermostat knob to switch
‘off’ the boiler. Open the pressure test point screw
on the burner manifold and fit a manometer (suitable
for 30mbar - Natural Gas or 50mbar - Propane).
Check low fire (start rate) against pressure shown in
Figure 2.2 (p4) or Appendix ‘A’ (p41). If necessary
adjust low fire pressure (refer to Figure 11.7a p29
for relevant gas valve fitted).
Having checked the low fire pressure,
carefully
adjust the differential (low fire offset) R21 (see
Figure 11.1 p26) between high and low fire (0 to 10°
C) on the main PCB. A recommended setting is 5°C.
Re-fit high/low plug connection CN16 to the main
PCB and check the high fire gas pressure against
that shown in Figure 2.2 (p4) or Appendix ‘A’ (p41).
If necessary adjust high fire governor to suit.
Occasionally this high fire adjustment can influence
the low fire (start rate), therefore remove plug
connection CN16 and check low fire pressure again.
Adjust if required. Repeat until low and high fire
pressures are as shown in Figure 2.2 (p4) or
Appendix ‘A’ (p41).
Cont: Page 31
1)
Gas supply is connected but turned to the "off"
position. Any unions or fittings are correctly
tightened, test points are closed, burners correctly
positioned, injectors are in place (of correct size)
and tight and that the ignition and probe leads are
connected correctly. Ensure Hot Surface igniter and
sensing probe assembly are not cracked or broken.
2)
Ensure electricity is connected, the gas valve
PCB connection is correctly located and that the
sensor and thermostat bulbs are fully inserted into
the boiler pocket. Reset temperature limiter by
firmly pressing pin (in controls housing.)
3)
If a sequencing interface module is fitted to the
boiler control panel, locate and the hand auto switch
‘SW1’ on the boiler main PCB (refer to Figure 11.1
p26), and set it to the ‘hand’ position to override
operation of the sequencing interface module for the
purposes of commissioning.
4)
Check setting of both temperature limiter and
control thermostat. The temperature limiter must be
set at 100°C from the factory unless otherwise
instructed. Set thermostat to required temperature.
5)
Drop down fascia on the controls housing to
reveal access to the main PCB. Figure 9.1 (p15)
shows the correct location of incoming wires.
Remove the plug connection CN21 from the main
PCB and replace the link by inserting a multi-meter
set to read DC
µ
A. Carefully remove high/low plug
connection CN16 from the main PCB, this will
ensure burner stays at start rate (low fire) when
fired.
6)
The Warmwell fully automatic boiler utilises a
low fire start gas rate ignited by hot surface igniter
(HSI), see Figure 14.1. To ascertain which type of
gas valve is fitted and the method of low fire and
high fire adjustment, refer to Figure 11.7. You
should familiarise yourself with this procedure for
use later when required.
7)
If a single header pipe kit is fitted, ensure that
the shunt pump is connected to the plug connection
CN13 on the main PCB. The run on timer is preset
to 5 minutes. Check that the fuse on the main PCB
is fitted and sound.
8) IMPORTANT:- PRIOR TO LIGHTING UP THE
BOILER, THE SAFETY LINKS ON THE MAIN PCB
MUST BE REMOVED AS DETAILED, TO ENSURE
SAFE OPERATION OF THE BOILER – REFER TO
FIGURE 11.1. THE LINKS MUST BE CAREFULLY
CUT USING A SMALL PAIR OF ELECTRICAL SIDE
CUTTERS AND THE RESULTANT LOOSE LINKS
MUST BE REMOVED FROM THE PCB SO AS NOT
TO CAUSE AN ELECTRICAL SHORT.
8.1
Check that LK2, LK3, LK4, LK5, LK6, LK10, &
LK13 have been factory removed.
8.2
For optional sequencing interface module
control cut LK7 & LK12.
27
Содержание Warmwell 120
Страница 50: ...HAMWORTHY HEATING LTD WARMWELL 500001091 F NOTES 44...
Страница 51: ...Notes...