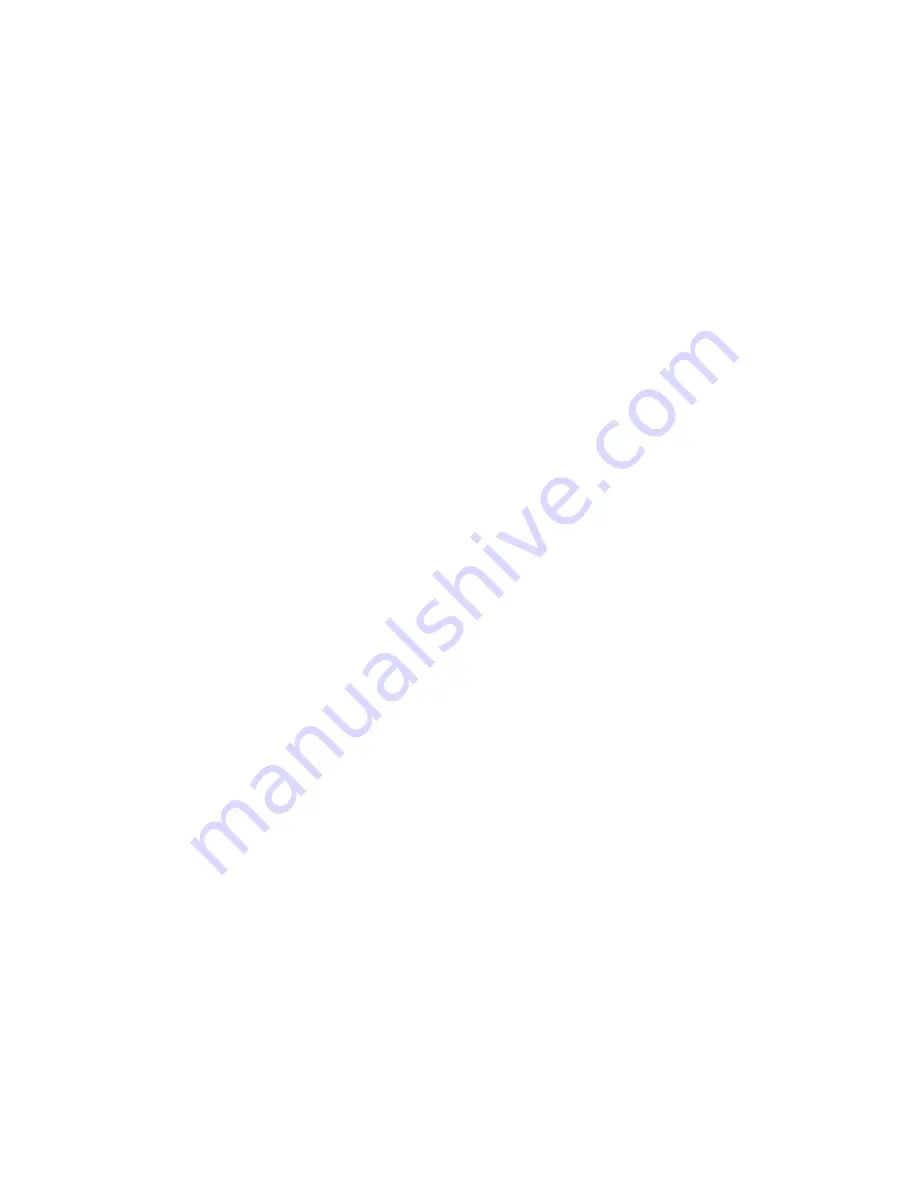
HAMWORTHY HEATING LTD
WARMWELL
500001091/F
same direction as the arrow on the bottom of the
valve. Refit all external components. Switch on gas
and power supply and check for integrity of all joints
using a proprietary leak detector. Ensure gas valve
(s) operation is correct and safe before continuing.
Refer to
Section 5.6
(p7)
if necessary for valve
integrity check procedure.
5)
Re-light the boiler using instructions on the
inside of the door. Check and adjust, the low fire/
start gas and high fire gas pressures, refer to Figure
2.2 (p4) for Natural Gas or Appendix ‘A’ (p41) -
propane firing, for correct settings. Re-set throttle
valve position, if replaced, see Figure 11.7b (p30)
for procedure. If necessary, refer to
Section 11.4
Commissioning the Boiler
(p24), for correct
procedures.
14.6 Fan Assembly
Ensure power supply is isolated. Access to the rear
of the boiler is required to service this item.
NOTE!
The 7 way plug and socket assembly
requires a 'tool' to disengage the locking
mechanism. A screwdriver should be inserted into
the slot in the plug and socket assembly. The plug
can then be pulled away from the socket.
Undo the 4 nuts holding the motor assembly to the
fan housing and remove complete motor and
impeller unit.
Due to the aggressive media being handled, it is
recommended that the complete fan motor and
impeller assembly be replaced if a motor has failed.
If required clean fan impeller taking care not to bend
or distort assembly.
Re-assemble unit in reverse order of dis-assembly.
NOTE!
All models utilise a capacitor start and run
motor. Before replacing motor due to possible
failure, ensure the capacitor is functioning correctly
(located in the exhaust fan control panel).
Ensure all screws are tightened and re-fit plug/
socket assembly.
Periodically check the fan volute, which is inside the
plenum chamber. This will require removal of the
stainless steel plenum chamber at the rear of the
boiler. Ensure flue is supported before removal.
The fan volute is fitted internally and fixed to the
plenum by the pressure tapping connection
assembly.
NOTE!
Connect pressure-sensing tubes
to their relevant positions to achieve correct
operation of the pressure switches.
See Figure 11.5 (p28) for tube/switch assembly
layout.
that of the control thermostat with some minor
differences. These are as below: -
Remove the 'push on' spade connections from the
temperature limiter body noting position of coloured
cables. Remove plastic cover (if fitted) and unscrew
holding nut to detach temperature limiter from
housing. Gently feed the capillary back through the
controls bulkhead. Re-set temperature limiter to
100°C. Check the operation of the device by
carefully applying a heat source to the bulb. Re-
assemble temperature limiter into controls housing
ensuring correct cable notation. Refer to the
thermostat diagram if terminal identification differs
from those given in Figure 9.1 (p15).
14.5 Main Gas Valve.
NOTE!
Some gas valve components can be
replaced without completely removing the whole
assembly from the boiler. However, Hamworthy
Heating strongly recommend that a new gas valve
assembly is fitted to ensure safe, reliable operation
of the boiler. Please refer to Hamworthy Heating
Technical Department before attempting to remove
components from the gas valve.
NOTE!
Only gas valves with an identical Type No.
may be used for replacement. Please contact
Hamworthy Heating spares Dept. for further
information.
Various types and manufacturers of gas valves are
used. Refer to Figure 11.7a (p29) for particular
valve(s) fitted.
1)
Ensure power and gas supplies are isolated.
2)
Remove the gas valve wiring plugs from the gas
valve(s) – secured by M3 screws through the plug
body.
NOTE!
The position of the relevant electrical
cables should be noted, especially on the 95 &
120kW boilers. Undo the union connection and
8mm nuts holding the gas valve/manifold assembly
to front plate, this will allow the whole assembly to
be removed from the boiler.
3)
Remove the gas valve by unscrewing cap head
screws holding valve to pipework. NOTE! The
position of the relevant electrical cables should be
noted, especially on the Warmwell 140 boiler. When
replacing the gas valve, it is advisable to renew the
`O` ring seals sealing both ends. See
SECTION
15.0 Recommended Spares
for Part Nos. Note
that the `O` ring fitted to the 60 & 95kW (Natural
Gas) and all propane models, is different to that
used on the 140kW (Natural Gas) model. Do not
over tighten cap head screws in gas valve body.
Ensure electrical plugs are firmly and correctly
located and holding screws are tightened.
4)
Replace assembly ensuring correct orientation
of the gas valve. Ensure that the gas flow is in the
38
Содержание Warmwell 120
Страница 50: ...HAMWORTHY HEATING LTD WARMWELL 500001091 F NOTES 44...
Страница 51: ...Notes...