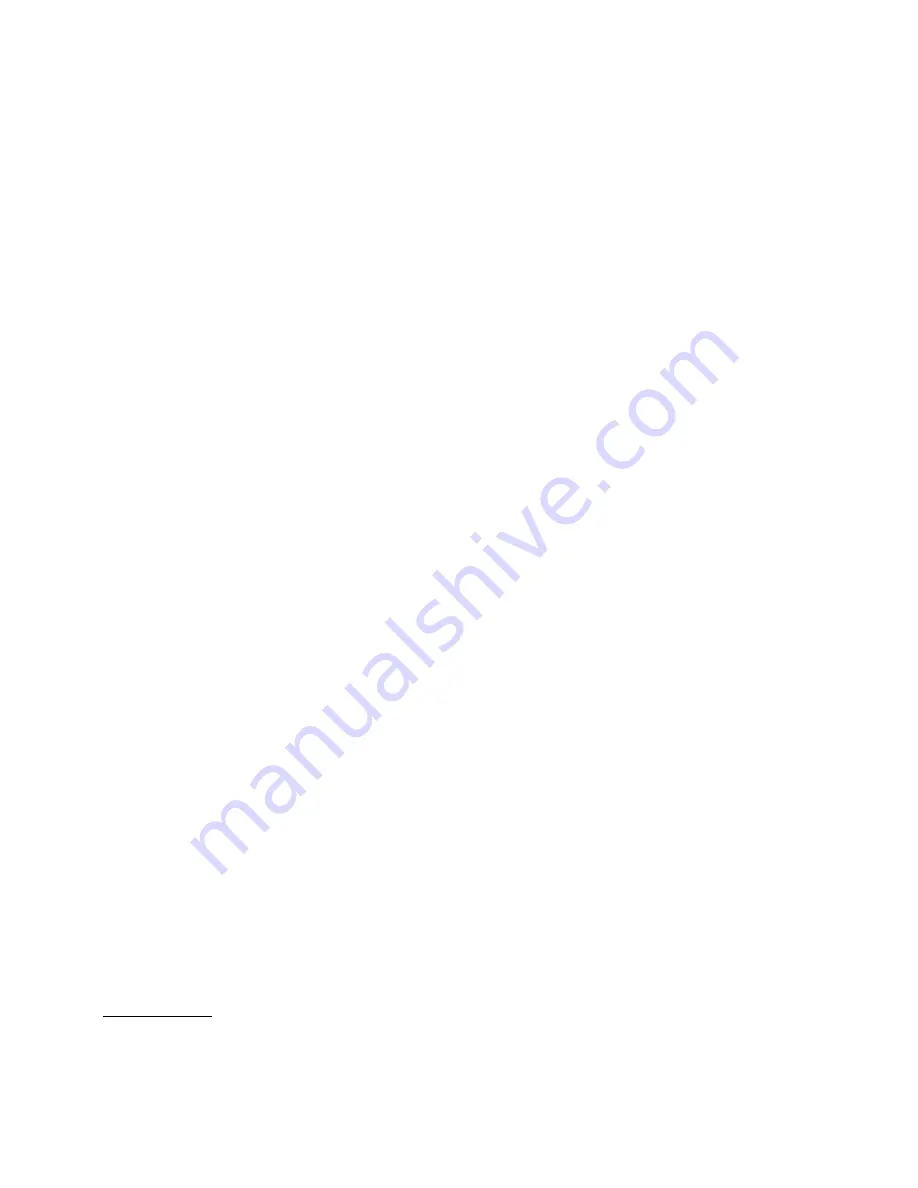
HAMWORTHY HEATING LTD
WARMWELL
500001091/F
is important that all controls and safety features are
checked for correct operation.
NOTE!
Measuring
flue gas CO
2
and gas temperatures will give an
indication of the state of the boiler flueways and
waterways. Results should be compared with
previously measured values to establish possible
loss of efficiency.
13.2 Before
servicing the boiler, the following
procedure must be carried out: -
WARNING: Isolate
the electrical supply and turn off the gas service
cock to the boiler module being serviced.
1)
Remove the front casing door by using a
screwdriver to rotate the ¼ turn latch.
2)
Turn off gas service cock, (fitted upstream of
gas control valve) and carefully drop down the
fascia of the controls housing.
3)
Undo both screws on gas valve gland plate,
situated under controls assembly, and carefully
disconnect the plug from the PCB. Withdraw the
cable and plug assembly.
4)
Disconnect igniter and probe leads carefully. A
protective boot will require pulling back to reveal the
sensing probe connector.
5)
Slacken union below gas service cock and
release. Slacken and remove nuts/washers holding
gas valve and manifold assembly. Remove
manifold assembly taking care not to damage high/
low gas solenoid.
6)
Carefully remove burner assembly by pulling
burner front plate. Check condition of igniter
assembly and probe for damage. Clean as
required. Check burner bars and clean using a soft
brush if required (if possible use compressed air to
blow out the dust inside the bar). Damaged or
cracked burner bars should be replaced. To replace
an individual bar will require drilling out the rivets
holding it on to the front plate. A replacement
burner bar will be supplied with clinch nuts and
screws to fix onto the front plate.
13.3
The boiler flueways can now be cleaned as
follows:-
1)
Carefully remove sloping front panel by pulling
both edges around the centre position. Remove the
top casing front panel secured by spring latches.
Insert a screwdriver into the slot in the 7 way plug
and socket assembly connected to the fan. The plug
can then be pulled away from the socket.
Disconnect the electrical connections from the main
PCB (CN1, CN2 & CN11), and carefully withdraw
the cables from the rear of the panel. Disconnect the
float switch cable via the push fit connector. Note
the relative positions and disconnect the flexible
hoses from the pressure switches. Remove the
exhaust fan control panel from the top side panels
control circuit is configured to establish a light/dark
check thereby ensuring the switch is open (no air)
before starting the fan. Once started the circuit then
checks that the switch has changed position (full air)
thus allowing the boiler to light and continue firing.
Prior to the ignition sequence starting, the fan has to
operate the air pressure switch and prove airflow.
With the thermostat calling for heat, neon NE7 on
the main PCB will be illuminated, indicating power to
the exhaust fan.
Once the fan is running, neon NE10 on the main
PCB will be illuminated – indicating that the low fire
airflow has been detected. A 20 second pre-purge
will commence, subsequent to which the green HSI
LED on the control panel fascia will illuminate. After
approximately 10 seconds the green Low Fire LED
on the control panel fascia will illuminate, indicating
the opening of the low fire gas valve. On ignition the
green HSI LED on the fascia will be extinguished.
Should there be a demand for hi fire, neon NE8 on
the main PCB will be illuminated, indicating the
changeover to the High Fire fan speed.
Subsequently, neon NE12 on the main PCB will be
illuminated, indicating that the High Fire airflow has
been detected. Simultaneously, the green High Fire
LED on the control panel fascia will illuminate. The
boiler should now be operating at High Fire.
A float switch is fitted to monitor the level in the
condense trap. Should the trap fail to discharge
condensate, the switch will operate and cause the
boiler to shut down. The condense trap should be
inspected regularly and cleaned out if necessary.
All Propane firing boilers are fitted with a low gas
pressure switch (set at 20mbar). Should the gas
supply pressure fall below this level, the boiler
will
not
operate. Refer to Appendix ‘A’ (p41) to check
operation of the low gas pressure switch.
12.2 Fault Finding Procedures
General fault finding is shown in Figure 12.2
(p34/35). If the boiler still cannot be operated
satisfactorily after following the chart, consult your
local office of Hamworthy Heating for assistance.
12.3 Possible Causes of Boiler Lockout
1) Ignition failure due to faulty igniter.
2) Ignition failure due to faulty gas valve.
3) No or low gas supply pressure.
4) No ignition due to faulty controller.
5) Ignition failure due to faulty damper mechanism.
6) Condensate trap blocked.
13.0 SERVICING
13.1
Regular annual servicing is recommended to
ensure trouble free operation. Although cleaning of
flueways may not be necessary on a yearly basis, it
33
Содержание Warmwell 120
Страница 50: ...HAMWORTHY HEATING LTD WARMWELL 500001091 F NOTES 44...
Страница 51: ...Notes...