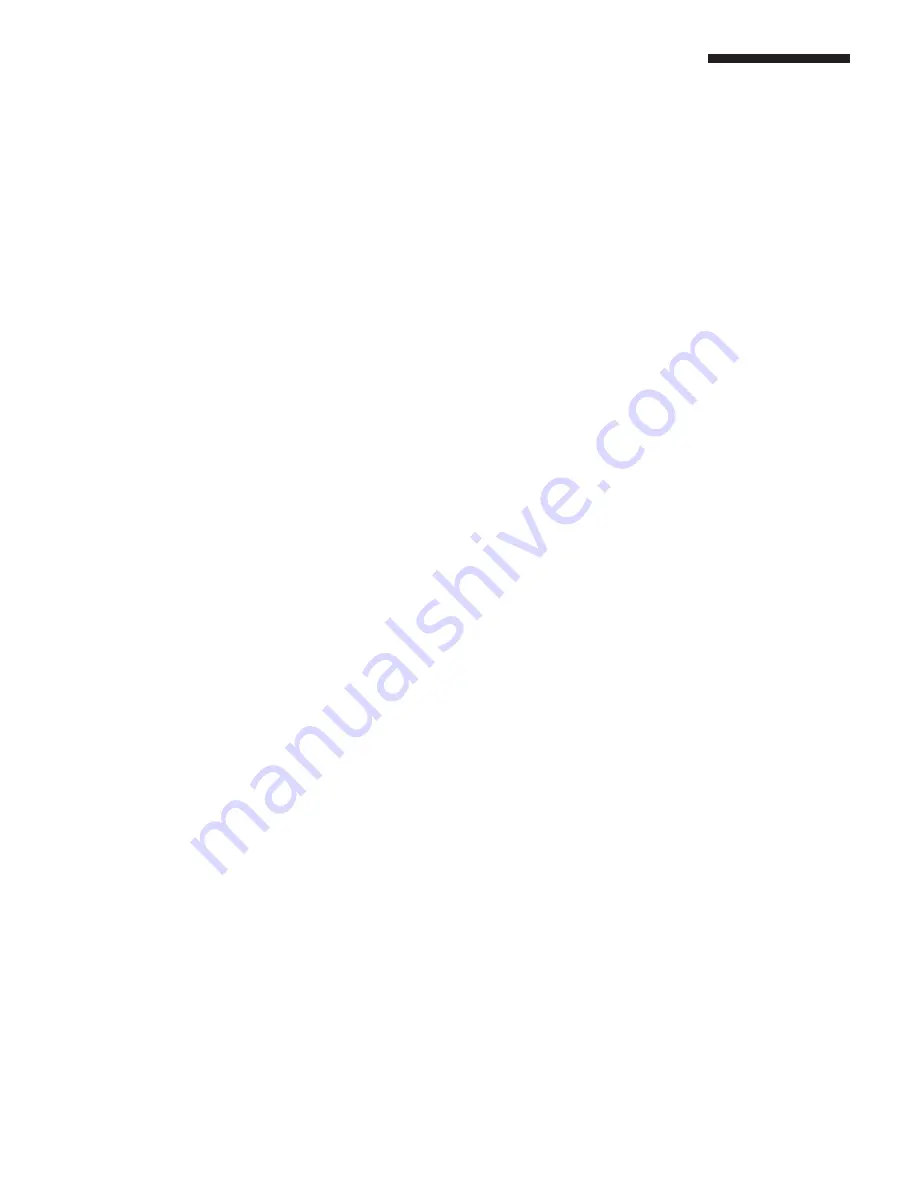
49
PART 6. START-UP PROCEDURES
3. Turn on gas shutoff valve (located
outside the cabinet on the rear
of the appliance) so that the
handle is aligned with the gas
pipe. If the handle will not turn by
hand, don’t try to repair it; call a
qualified service technician. Force
or attempted repair may result in a
fire or explosion.
4. Do not use this appliance if
any part has been under water.
Immediately call a qualified service
technician to inspect the appliance
and to replace any part of the
control system and any gas control
which has been under water.
5. The appliance shall be installed
so the gas ignition system
components are protected from
water (dripping, spraying, rain, etc.)
during appliance operation and
service (circulator replacement,
condensate trap, control
replacement, etc.).
B. LIGHTING INSTRUCTIONS (continued)
C. OPERATING INSTRUCTIONS
D. INI PROCESS AND SERVICE PROCEDURES
1.
STOP!
Make sure you have read
the safety information above.
2. Turn off all electric power to the
appliance.
3. This appliance is equipped
with an ignition device which
automatically lights the burner. Do
not try to light the burner by hand.
4. Turn gas shutoff valve clockwise
to “off” —do not force it.
5. Wait five (5) minutes to clear
out any gas. If you then
smell gas, STOP! Follow the
instructions from Section B:
Lighting Instructions in the safety
information. If you don’t smell
gas, go to the next step.
6. Turn the gas shutoff valve counter
clockwise to “on.”
7. Turn on all electric power to
appliance.
8. Set the thermostat to the desired
setting.
9. If the appliance will not operate,
follow the instructions “To Turn
Off Gas To Appliance” (Part 7,
Section F, and call your service
technician or gas supplier.
The HOT™ Controls, contain a
unique function, they track the
accuracy, degradation and fouling
of all connected sensors and
pressure transducers and the major
components of the system; appliance
heat exchanger, fan, pump and
igniter.
This tracking is accomplished by
taking readings of and creating trend
lines for each mentioned item and
then running calculations of some
versus others to determine how the
need for maintenance of specific
components is progressing.
Aside from the use of up to 11
different sensors to monitor items
like incoming gas and leaving fan
pressure and pressure at the exiting
side of the heat exchanger and
condensate drain connection, we
have an initialization (INI) process
that takes place automatically in the
background to collect this data during
steady state conditions and record it,
to populate the trend lines.
The creation of a baseline: Zero INI
(Z-INI), is an important step in this
process and normally occurs during
the commissioning of the system.
Within 2 minutes of powering the
appliances up, a question will be
presented on screen: “A ZERO INI
IS REQUIRED—RUN NOW?” YES
or NO, unless the entire system is
fully commissioned and operating
normally, answer NO. The question
will be presented every 15 minutes
until you finally select “YES”. It is best
not to answer YES until all appliances
are started and combustion set.
When they are all ready, turn off
power to all at the switch on the
front near the display. Go back to the
appliance with two displays, power
it and all others on, and when the
question is presented again (two
minutes or less), answer YES on each
individual appliance. The Z-INI should
be completed in less than 10 minutes.
If you end up with the Z-INI running
when things are not quite 100% as
they will be when the system is up
and running, not to worry, with the
proper password, you can overwrite
the Z-INI with a replacement, so you
are sure your Z-INI is a true baseline
to work from.
Содержание XL800
Страница 6: ...6 PART 1 GENERAL INFORMATION As a Stand Alone Appliance HOT CONTROL MENU NAVIGATION ...
Страница 7: ...7 PART 1 GENERAL INFORMATION Appliance as Part of a Cascade HOT CONTROL MENU NAVIGATION ...
Страница 19: ...19 PART 2 ELECTRICAL B INTERNAL WIRING CONNECTION continued XL BCB LAYOUT ...
Страница 21: ...21 PART 2 ELECTRICAL XL CASCADE BOX ...
Страница 31: ...31 PART 4 VENTING Direct Vent Terminal Clearances ...
Страница 32: ...32 PART 4 VENTING Direct Vent Terminal Clearances continued Other Than Direct Vent Terminal Clearances ...
Страница 33: ...33 PART 4 VENTING Other Than Direct Vent Terminal Clearances continued ...
Страница 69: ...69 PART 10 PARTS BREAKDOWN 1A 1B PART 10 PARTS BREAKDOWN 2 ...
Страница 70: ...70 PART 10 PARTS BREAKDOWN 3 4 5 6 7 8 9A 9B 9C 10 4 ...