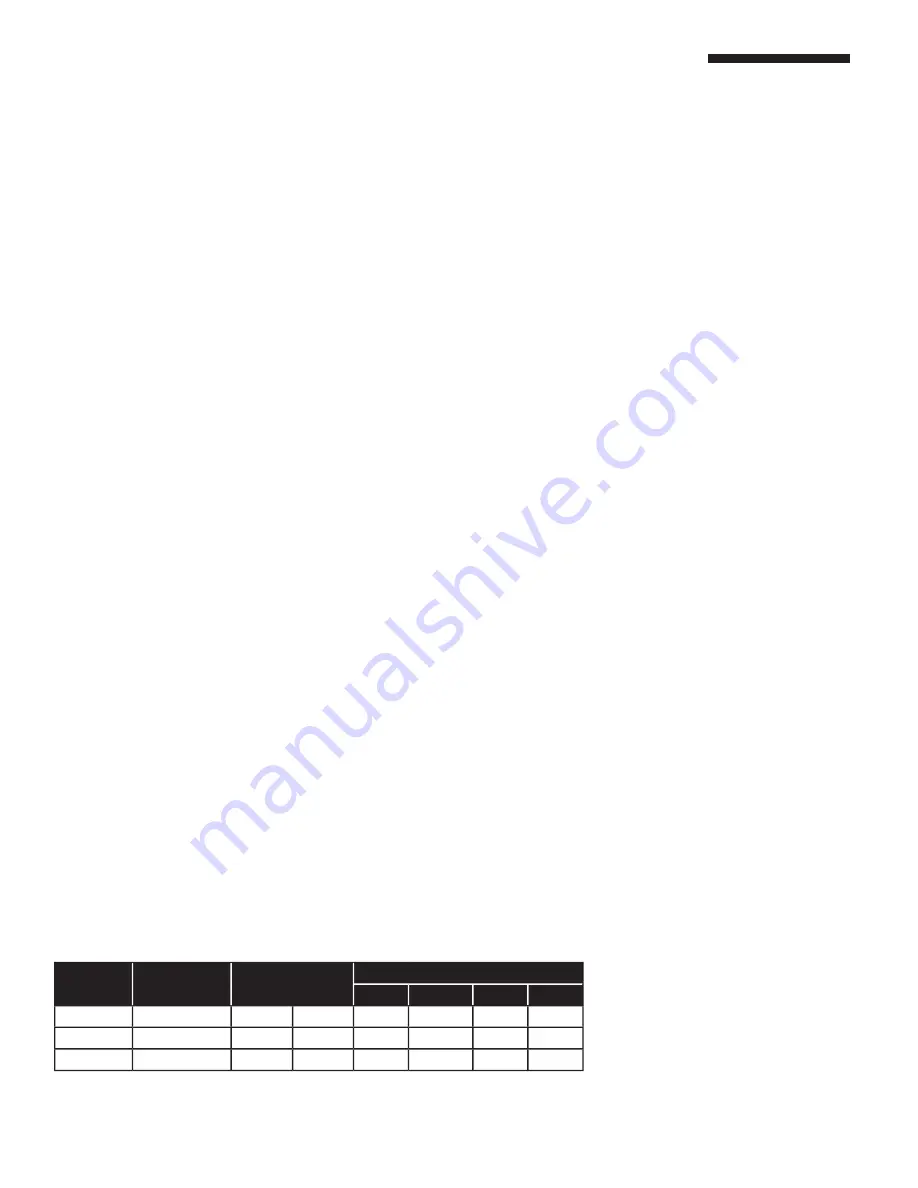
39
PART 5. PIPING
Basic piping connection steps are listed below. A drawing, specific to your application can be obtained from your
distributor or the Manufacturer, which will guide you through proper installation of the appliance.
1) Pipe properly, in accordance with generally accepted piping principals
or the Manufacturers specific documents.
2) Connect system return to the pipe entering the appliance.
3) Connect system supply to the pipe leaving the appliance
containing the Relief Valve.
4) Install Drain Valve on system supply.
NOTE:
The appliance cannot be drained of water without purging the unit with air pressure, 15 PSI minimum. The
system’s air vent must be closed during this process.
(TABLE 5-1) BOILER PIPING
Model
Boiler Only
GPM ∆P
Design ∆T
Minimum Manifold Pipe Size
Single
Double
Triple
Quad
HW 800
30.2@2'
50.0 ˚F 27.8 ˚C
1.5"
2"
2.5"
3"
HW 1000
50.0 ˚F 27.8 ˚C
2"
2.5"
3"
4"
HW 1500
50.0 ˚F 27.8 ˚C
2"
3"
4"
6"
Note: Flow rates shown above are for clean, closed loop systems, if there is any doubt about system cleanliness
proper precautions should be taken, and the flow rates for appliances as shown in Table 5-2 should be utilized.
PART 5. PIPING
A. HYDRONIC HEATING BOILER PIPING
The appliance is designed to function
in a closed loop (minimum) 12 PSI
System. Never let the appliance
operate without a minimum of 10 PSI
water pressure, this assures that the
heat exchanger can be completely
purged of air, failure to do so could
cause damage. It is important to
note that the appliance is flow
dependent for proper efficiency
and life expectancy; therefore,
primary-secondary piping or use of
a low loss header design is always
recommended. Each appliance
should have an Air Eliminator, which
will remove air from the Hydronic
System. Always follow good piping
practices. Observe minimum 1"
clearance to combustibles around
all uninsulated hot water pipes, or
when openings around pipes are
not protected by non-combustible
materials. On an appliance installed
above the level of the highest heat
transfer device, some state and local
codes require a low water cut off
device at the time of installation by
the installer. A water flow switch is
provided as standard and will take
the place of a low water cut-off. If
the appliance supplies hot water
to heating coils in air handler units,
flow control valves or other devices
must be installed to prevent gravity
circulation of boiler water in the coils
during the cooling cycle.
Minimum Manifold Pipe Sizes
Содержание XL800
Страница 6: ...6 PART 1 GENERAL INFORMATION As a Stand Alone Appliance HOT CONTROL MENU NAVIGATION ...
Страница 7: ...7 PART 1 GENERAL INFORMATION Appliance as Part of a Cascade HOT CONTROL MENU NAVIGATION ...
Страница 19: ...19 PART 2 ELECTRICAL B INTERNAL WIRING CONNECTION continued XL BCB LAYOUT ...
Страница 21: ...21 PART 2 ELECTRICAL XL CASCADE BOX ...
Страница 31: ...31 PART 4 VENTING Direct Vent Terminal Clearances ...
Страница 32: ...32 PART 4 VENTING Direct Vent Terminal Clearances continued Other Than Direct Vent Terminal Clearances ...
Страница 33: ...33 PART 4 VENTING Other Than Direct Vent Terminal Clearances continued ...
Страница 69: ...69 PART 10 PARTS BREAKDOWN 1A 1B PART 10 PARTS BREAKDOWN 2 ...
Страница 70: ...70 PART 10 PARTS BREAKDOWN 3 4 5 6 7 8 9A 9B 9C 10 4 ...