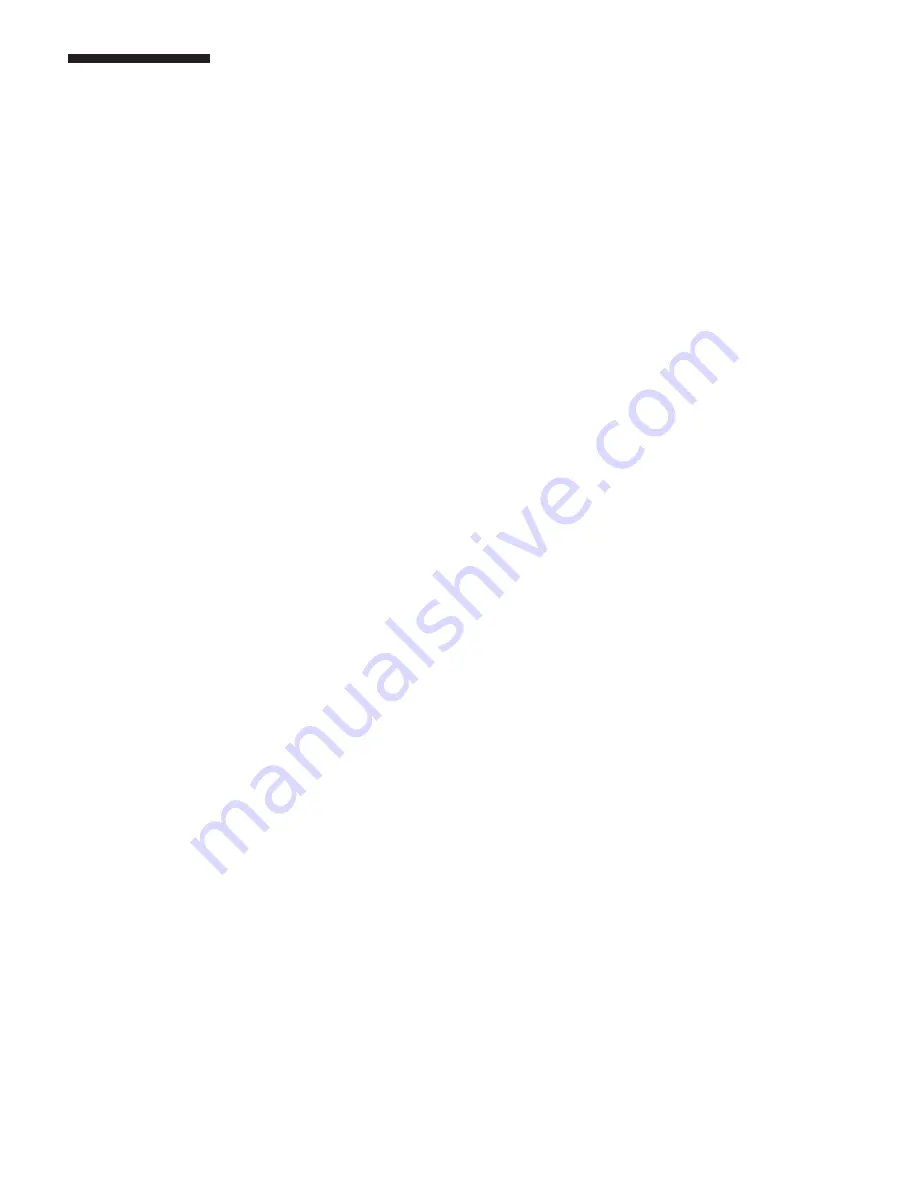
66
PART 8. MAINTENANCE
C. HEAT EXCHANGER ANTI-SCALING PREVENTION FEATURE
The
appliance
controller contains
sophisticated software that
enables it to monitor the rate of
temperature rise through the heat
exchanger. By doing this, it greatly
reduces the possibility of heat
exchanger failure due to scaling
or fouling. A set of parameters are
programmed in at the factory, to
provide a design temperature rise
(∆T) setting on each size unit that
is fixed. The Anti-Scale is based
on an increase over the design
∆T through the heat exchanger.
This Anti-Scale is determined
using the inlet and outlet sensors,
even if a tank thermistor is being
used. If the Anti-Scale setting is
reached, the unit will display H11,
shut down and not re-fire until it
has cooled. The first 3 times this
happens, there will be a reduction
of the maximum firing rate. The
fault will be accompanied by either
an A, B, or C suffix, indicating a
maximum firing rate of 80%, 50%,
or 30% respectively. The control
will go into hard Lockout after the
C suffix is achieved, and have to
be manually reset. Once the heat
exchanger has been acid cleaned,
contact the factory for instructions
on resetting the unit for full rated
BTU input.
Typical causes for repeated H11
indications at start up are air
trapped in the heat exchanger
or contaminates lodging in the
piping or heat exchanger during
installation, both of these causes
can generally be cleared by
isolating the hot water system and
flushing water at full city pressure
through the drain valve or relief
valve on the
appliance
outlet.
Содержание XL800
Страница 6: ...6 PART 1 GENERAL INFORMATION As a Stand Alone Appliance HOT CONTROL MENU NAVIGATION ...
Страница 7: ...7 PART 1 GENERAL INFORMATION Appliance as Part of a Cascade HOT CONTROL MENU NAVIGATION ...
Страница 19: ...19 PART 2 ELECTRICAL B INTERNAL WIRING CONNECTION continued XL BCB LAYOUT ...
Страница 21: ...21 PART 2 ELECTRICAL XL CASCADE BOX ...
Страница 31: ...31 PART 4 VENTING Direct Vent Terminal Clearances ...
Страница 32: ...32 PART 4 VENTING Direct Vent Terminal Clearances continued Other Than Direct Vent Terminal Clearances ...
Страница 33: ...33 PART 4 VENTING Other Than Direct Vent Terminal Clearances continued ...
Страница 69: ...69 PART 10 PARTS BREAKDOWN 1A 1B PART 10 PARTS BREAKDOWN 2 ...
Страница 70: ...70 PART 10 PARTS BREAKDOWN 3 4 5 6 7 8 9A 9B 9C 10 4 ...