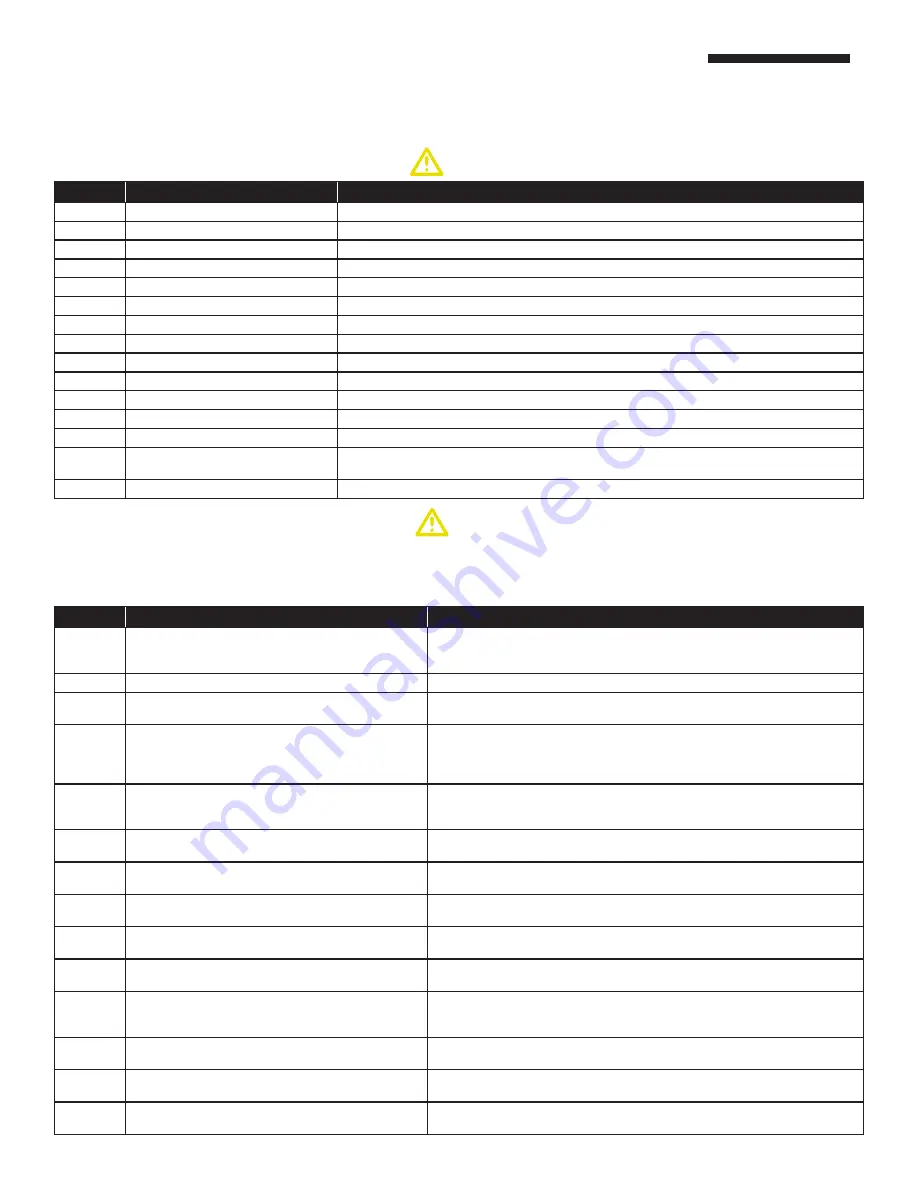
59
PART 7. SERVICE AND MAINTENANCE
D. SOFT LOCKOUT CODES (See Section 1, Part A for Sensor Locations and Uses)
(TABLE 7-1) CCB SOFT LOCK OUT (SLO) CODES
(TABLE 7-2) BCB SOFT LOCK OUT (SLO) CODES
*Codes may appear with an A, B, or C as a suffix denoting the number of times the code has appeared since the
last Initialization (INI). Some SLO’s are accompanied by a reduction of the maximum firing rate; A=80%, B=50%,
C=30%. After the C suffix appears, the next code of that kind becomes an HLO (manual reset required).
Code
Cause
Recommended Action
CCB01
Sensor S1 fault
Check that the S1 sensor is connected
CCB02
Sensor S2 fault
Check that the S2 sensor is connected
CCB03
Sensor S3 fault
Check that the S3 sensor is connected
CCB04
Sensor S4/SZ1 fault
Check that the S4/SZ1 sensor is connected
CCB05
Sensor S5/SZ2 fault
Check that the S5/SZ2 sensor is connected
CCB06
Sensor S6 fault
Check that the S6 sensor is connected
CCB07
Sensor SZ3 fault
Check that the SZ3 sensor is connected
CCB08
Sensor zone 4 fault
Check that the zone 4 sensor is connected
CCB09
Sensor zone 5 fault
Check that the zone 5 sensor is connected
CCB10
Sensor zone 6 fault
Check that the zone 6 sensor is connected
CCB11
Sensor zone 7 fault
Check that the zone 7 sensor is connected
CCB12
Sensor zone 8 fault
Check that the zone 8 sensor is connected
CCB15
Communication error via Modbus programming Quantity of programmed appliances does not match quantity of connected appliances.
CCB20-
CCB27
Communication error with a specific appliance;
A = CCB 20… H = CCB 27
Check specific appliance to see that it is powered on, if yes, then check all communication connections at display and
main boards
CCB200
EEPROM fault
Check that the EEPROM is connected properly
Code
Cause
Recommended Action
A1*
Excessive pressure differential (∆P) on water side of heat exchanger
Check for scaling or blockage on water side of heat exchanger, also check pump performance. If
this SLO is indicated while the unit is firing, it is doing so at a reduced BTU input; low enough to stay
below that maximum ∆P set point.
B01
Pressure too high at condensate drain connection during Stand By
Look for condensate backing up into combustion side of heat exchanger.
B02
Pressure too high at condensate drain connection during pre-purge
Insure condensate drain system is flowing freely, and vent is clear of obstructions. Also, be sure the
Z-INI has been initiated.
B03
Pressure too low at condensate drain connection during pre-purge
Check for condensate (water) in the condensate neutralizer (if equipped) or the condensate trap
at appliance outlet. If it is dry, add water to form trap. The appliance also will initiate an auto-filling
process for the condensate trap, indicated on the screen during this operation. Also, be sure the
Z-INI has been initiated.
B04
Pressure at flue/condensate sensor is too low
Check flue gas vent connection or sensor connection located at condensate drain line. Also check
for a disconnected or open condensate drain line and last, look for a leak in the heat exchanger
outer casing (behind the insulation).
DW7*
Temperature rise (∆T) through heat exchanger is too high
Unit is operating at a reduced BTU input - check for scaling or blockage on water side of heat
exchanger, also check pump performance.
FL05*
Flue gas temperature too high
Unit is burning at a reduced BTU input rate. The cause of the high flue gas temperature should be
investigated and corrected ASAP
FL09*
Fouling of the fire side of the heat exchanger
Unit is burning at a reduced BTU input rate. A combustion side inspection and cleaning should be
scheduled ASAP.
FL13
Flue gas sensor (T5) fault (not connected or open status)
Check the condition of the connectors and wires from the card edge connector at the board to the
flue gas sensor on the appliance.
FL14
Flue gas sensor (T5) fault (short circuit status)
Take an OHM reading at the connector on the flue gas sensor - compare it to the chart in Part 7,
Section I, replace if out of range.
G01*
Gas supply pressure too low
If this occurs at the beginning of an ignition cycle, this SLO will stay until the pressure is high enough
for proper ignition. If this occurs while the unit is firing, and it continues to fire, it is doing so at a
reduced BTU input low enough to stay above that minimum pressure set point.
H01
Outlet sensor (T1.1, 1.2) fault (not connected or open status)
Check the condition of the connectors and wires from the card edge connector at the board to the
outlet sensor on the appliance.
H02
Inlet sensor (T2) fault (not connected or open status)
Check the condition of the connectors and wires from the card edge connector at the board to the
inlet sensor on the appliance.
H04
Outlet sensor (T1.1, 1.2) fault (short circuit status)
Take an OHM reading on the outlet sensor - compare it to the chart in Part 7, Section I, replace if
out of range.
Содержание XL800
Страница 6: ...6 PART 1 GENERAL INFORMATION As a Stand Alone Appliance HOT CONTROL MENU NAVIGATION ...
Страница 7: ...7 PART 1 GENERAL INFORMATION Appliance as Part of a Cascade HOT CONTROL MENU NAVIGATION ...
Страница 19: ...19 PART 2 ELECTRICAL B INTERNAL WIRING CONNECTION continued XL BCB LAYOUT ...
Страница 21: ...21 PART 2 ELECTRICAL XL CASCADE BOX ...
Страница 31: ...31 PART 4 VENTING Direct Vent Terminal Clearances ...
Страница 32: ...32 PART 4 VENTING Direct Vent Terminal Clearances continued Other Than Direct Vent Terminal Clearances ...
Страница 33: ...33 PART 4 VENTING Other Than Direct Vent Terminal Clearances continued ...
Страница 69: ...69 PART 10 PARTS BREAKDOWN 1A 1B PART 10 PARTS BREAKDOWN 2 ...
Страница 70: ...70 PART 10 PARTS BREAKDOWN 3 4 5 6 7 8 9A 9B 9C 10 4 ...