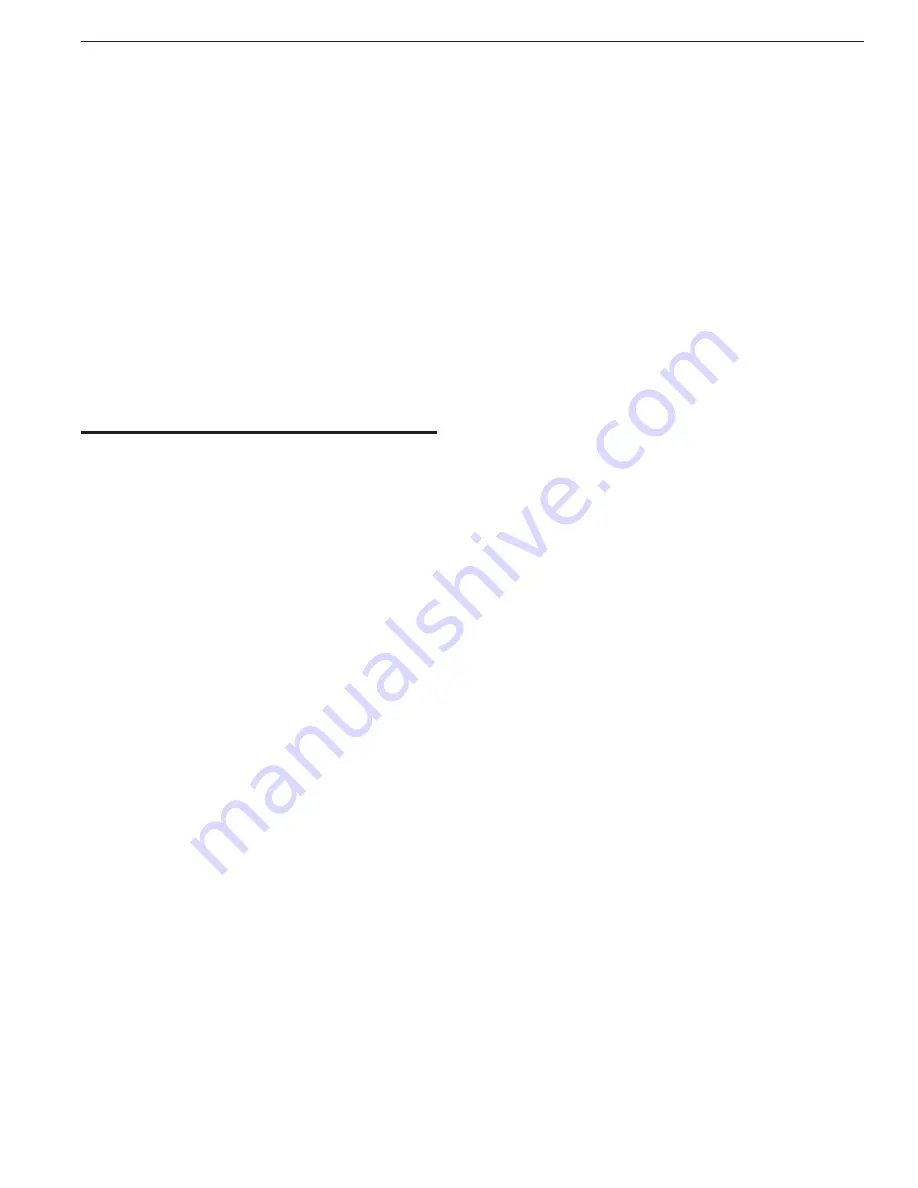
Error #10406 - WARN_PROG_OVER_RANGE_LOADCELL_COEF
Description:
The sampled maximum load cell signal (coe
ffi
cient) is greater than the acceptable range from
the normal coe
ffi
cient value) for this unit. The acceptable range of this parameter is empirically determined
and selected for di
ff
erent models and capacities.
Reaction:
Handle OLED displays the warning while unit is allowed to continue to run. The over-range
warning indicates the potential error in programming the parameter without altering the value. The sam-
ple value is still retained.
Cause / Remedy:
The load cell maximum signal (coe
ffi
cient) is sampled during procedure step (2) (see
Warning #10404). When this parameter is calibrated, the unit is expected to be loaded with a weight corre-
sponding to the capacity of the unit. The possible causes can be:
(a) Step (1) of the calibration procedure (see Warning #10404) is not correctly performed.
(b) The pickup weight does not match the rated capacity.
(c) The metal mounting bracket of the white plastic wear ring may be bent such that the wear ring is pressing
against the cast housing opening. When the unit is loaded, the wear ring should be situated near the cen-
ter of the circular opening without any contact. Readjust the bracket or replace it.
(d) Problem with the load cell electronics. This may include a damaged load cell or loose load cell cable con-
nection to the actuator main interface board or to the servo drive.
(e) The actuator PCB board which processes the load cell signal may be damaged or out of spec. Replace the
PCB board.
C.2. Command Warnings - Motion Control
Error #11000 - WARN_BOTH_TRAVEL_LIMITS_ENGAGED
Description:
Both the upper and lower travel limit switches are engaged at motion startup (i.e. handle, pendant,
fl
oat mode, etc.). This warning can only trigger after the unit has powered up and is di
ff
erent from error #501.
Reaction:
Motion not started and handle display warning on the OLED.
Cause / Remedy:
(a) Check for any mechanical binding that could engage both the upper and lower limit switches.
(b) Check and correct if the limit switch cable is connected to the interface board.
(c) Check for bad electrical connection or shorted wires from the switches.
Error #11001 - WARN_UNCONTROLLED_MODE_SWITCH
Description:
The current running control mode (RUN MODE) is switched to another unexpectedly or a Han-
dle type miss-match is detected.
Reaction:
Handle OLED displays the warning while unit is allowed to continue to run.
Cause / Remedy:
When a control mode is started, the handle OLED displays the type of RUN MODE
the unit is running at, e.g. HANDLE, PENDANT, or FLOAT MODE.
(a) If the OLED displays the incorrect Handle type or Mode at any time that does not match the actual Handle
type/Mode, the Handle motherboard may be damaged and should be replaced.
(b) For all other cases, please contact Gorbel Inc. to describe the symptoms and if the problem is reoccurring.
Error #11003 - WARN_SLIDE_PENDANT_TYPE_IO_BOTH_OFF
Description:
Slide or pendant handle sends a unique signal to the PLC to di
ff
erentiate the handle type. This error
is caught if none of them is received.
Reaction:
Unit is stopped with a warning display.
Cause / Remedy:
Replace the slide or pendant handle motherboard.
Error #11004 - WARN_UP_DOWN_V_LIMITS_AT_SAME_POSITION
Description:
This warning is triggered when both the Upper and Lower Virtual Limits are attempted to be
programmed to the same position, which would essentially stop all motion. This is done by checking if the
distance gap between these two limits is less than 1”. In other words, the Upper and Lower Virtual Limits
must be at least 1” apart.
Reaction:
Handle OLED displays the warning message and the virtual limit is not programmed.
Cause / Remedy:
While this warning attempts to catch and prevent false setup, if it is unintentional, move
the two virtual limit positions slightly apart and re-program the virtual limit(s).
G-Force® & Easy Arm Q2 - iQ2 Service Manual
Gorbel Inc.
Revised 5/21
6 - 16
Содержание G-Force iQ2 Series
Страница 2: ...G Force Easy Arm Q2 iQ2 Service Manual Gorbel Inc Revised 5 21 0 1 This page intentionally left blank...
Страница 4: ...G Force Easy Arm Q2 iQ2 Service Manual Gorbel Inc Revised 5 21 0 3 This page intentionally left blank...
Страница 19: ...This page is intentionally left blank G Force Easy Arm Q2 iQ2 Service Manual Gorbel Inc Revised 5 21 5 5...
Страница 42: ...This page is intentionally left blank G Force Easy Arm Q2 iQ2 Service Manual Gorbel Inc Revised 5 21 7 3...
Страница 43: ...ACTUATOR PCB GEN 2 G Force Easy Arm Q2 iQ2 Service Manual Gorbel Inc Revised 5 21 7 4...
Страница 45: ...This page is intentionally left blank G Force Easy Arm Q2 iQ2 Service Manual Gorbel Inc Revised 5 21 7 6...
Страница 83: ...G Force Easy Arm Q2 iQ2 Service Manual Gorbel Inc Revised 5 21 9 30 This page is intentionally left blank...
Страница 105: ...G Force Easy Arm Q2 iQ2 Service Manual Gorbel Inc Revised 5 21 9 52 This page is intentionally left blank...
Страница 111: ...G Force Easy Arm Q2 iQ2 Service Manual Gorbel Inc Revised 5 21 9 58 Remote Force Sensing Hub SEE CHART 1...
Страница 112: ...G Force Easy Arm Q2 iQ2 Service Manual Gorbel Inc Revised 5 21 9 59 FSH HUB Options...
Страница 113: ...G Force Easy Arm Q2 iQ2 Service Manual Gorbel Inc Revised 5 21 9 60 This page is intentionally left blank...
Страница 119: ...G Force Easy Arm Q2 iQ2 Service Manual Gorbel Inc Revised 5 21 9 66 Diagram G 1a G360 with Air Assembly and Disassembly...
Страница 120: ...G Force Easy Arm Q2 iQ2 Service Manual Gorbel Inc Revised 5 21 9 67 Diagram G 1b G360 Assembly and Disassembly...
Страница 121: ...G Force Easy Arm Q2 iQ2 Service Manual Gorbel Inc Revised 5 21 9 68 This page is intentionally left blank...
Страница 136: ...G Force Easy Arm Q2 iQ2 Service Manual Gorbel Inc Revised 5 21 9 83 This page is intentionally left blank...