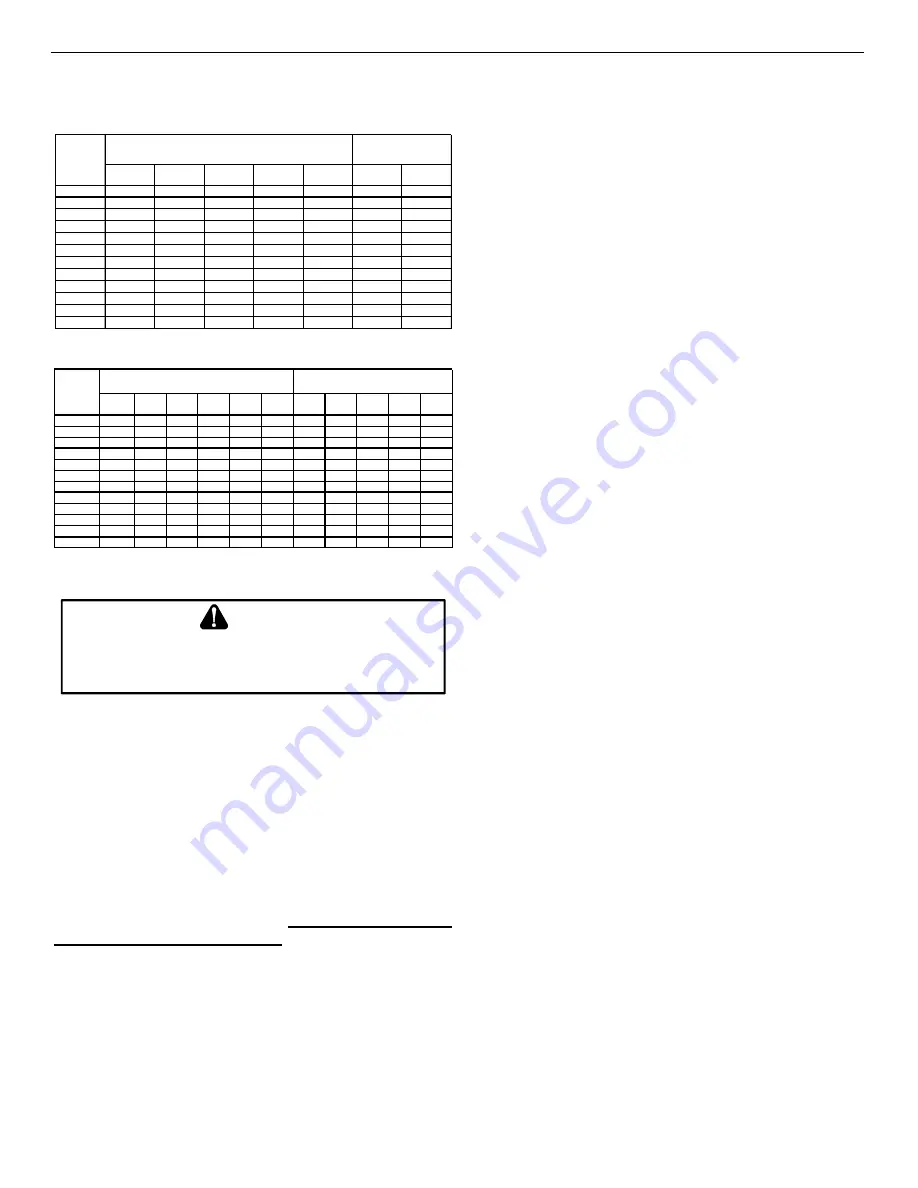
22
P
ROPANE
G
AS
P
IPING
C
HARTS
3/8"
1/2"
5/8"
3/4"
7/8"
1/2"
3/4"
10
730
1,700
3,200
5,300
8,300
3,200
7,500
20
500
1,100
2,200
3,700
5,800
2,200
4,200
30
400
920
2,000
2,900
4,700
1,800
4,000
40
370
850
1,700
2,700
4,100
1,600
3,700
50
330
770
1,500
2,400
3,700
1,500
3,400
60
300
700
1,300
2,200
3,300
1,300
310
80
260
610
1,200
1,900
2,900
1,200
2,600
100
220
540
1,000
1,700
2,600
1,000
2,300
125
200
490
900
1,400
2,300
900
2,100
150
190
430
830
1,300
2,100
830
1,900
175
170
400
780
1,200
1,900
770
1,700
200
160
380
730
1,100
1,800
720
1,500
Sizing Between First and Second Stage Regulator*
Maximum Propane Capacities listed are based on 2 psig pressure drop at 10 psig setting.
Capacities in 1,000 BTU/hour.
Nominal Pipe Size
Schedule 40
Tubing Size, O.D. Type L
Pipe or
Tubing
Length,
Feet
3/8"
1/2"
5/8"
3/4"
7/8"
1-1/8"
1/2"
3/4"
1"
1-1/4" 1-1/2"
10
39
92
199
329
501
935
275
567
1,071
2,205
3,307
20
26
62
131
216
346
630
189
393
732
1,496
2,299
30
21
50
107
181
277
500
152
315
590
1,212
1,858
40
19
41
90
145
233
427
129
267
504
1,039
1,559
50
18
37
79
131
198
376
114
237
448
91
1,417
60
16
35
72
121
187
340
103
217
409
834
1,275
80
13
29
62
104
155
289
89
185
346
724
1,066
100
11
26
55
90
138
255
78
162
307
630
976
125
10
24
48
81
122
224
69
146
275
567
866
150
9
21
43
72
109
202
63
132
252
511
787
200
8
19
39
66
100
187
54
112
209
439
665
250
8
17
36
60
93
172
48
100
185
390
590
Pipe or
Tubing
Length,
Feet
Nominal Pipe Size
Schedule 40
Tubing Size, O.D. Type L
Sizing Between Se cond Stag e and Appliance Regulator*
Maximum Propane Capacities listed are ba se d on 2 p sig pressure d rop at 10 psig se tting.
Cap acities in 1,0 00 BTU/hour.
C
IRCULATING
A
IR
AND
F
ILTERS
N
EVER
ALLOW
THE
PRODUCTS
OF
COMBUSTION
,
INCLUDING
CARBON
MONOXIDE
,
TO
ENTER
THE
RETURN
DUCT
WORK
OR
CIRCULATION
AIR
SUPPLY
.
WARNING
Duct systems and register sizes must be properly designed for
the CFM and external static pressure rating of the furnace.
Ductwork should be designed in accordance with the recom-
mended methods of “Air Conditioning Contractors of America”
Manual D.
A duct system must be installed in accordance with Standards
of the National Board of Fire Underwriters for the Installation of
Air Conditioning, Warm Air Heating and Ventilating Systems.
Pamphlets No. 90A and 90B.
A closed return duct system must be used, with the return duct
connected to the furnace.
NOTE:
Ductwork must never be
attached to the back of the furnace. For installations requiring
more than 1800 CFM, use a bottom return or two sided return.
Supply and return connections to the furnace may be made
with flexible joints to reduce noise transmission. To prevent the
blower from interfering with combustion air or draft when a cen-
tral return is used, a connecting duct must be installed be-
tween the unit and the utility room wall. A room, closet, or
alcove must not be used as a return air chamber.
When the furnace is used in connection with a cooling unit, the
furnace should be installed in parallel with or on the upstream
side of the cooling unit to avoid condensation in the heating
element. With a parallel flow arrangement, the dampers or other
means used to control the flow of air must be adequate to
prevent chilled air from entering the furnace and, if manually
operated, must be equipped with means to prevent operation of
either unit unless the damper is in the full heat or cool position.
When the furnace is installed without a cooling coil, it is rec-
ommended that a removable access panel be provided in the
outlet air duct. This opening shall be accessible when the fur-
nace is installed and shall be of such a size that the heat
exchanger can be viewed for visual light inspection or such that
a sampling probe can be inserted into the airstream. The ac-
cess panel must be made to prevent air leaks when the furnace
is in operation.
When the furnace is heating, the temperature of the return air
entering the furnace must be between 55°F and 100°F.
When a furnace is installed so that supply ducts carry air cir-
culated by the furnace to areas outside the space containing
the furnace, the return air shall also be handled by a duct sealed
to the furnace casing and terminating outside the space con-
taining the furnace.
C
HECKING
D
UCT
S
TATIC
Refer to your furnace rating plate for the maximum ESP (exter-
nal duct static) rating.
Total external static refers to everything external to the furnace
cabinet. Cooling coils, filters, ducts, grilles, registers must all
be considered when reading your total external static pres-
sure. The supply duct pressure must be read between the fur-
nace and the cooling coil. This reading is usually taken by
removing the “A” shaped block off plate from the end on the
coil; drilling a test hole in it and reinstalling the block off plate.
Take a duct static reading at the test hole. Tape up the test
hole after your test is complete. The negative pressure must be
read between the filter and the furnace blower.
Too much external static pressure will result in insufficient air
that can cause excessive temperature rise. This can cause
limit switch tripping and heat exchanger failure.
To determine total external duct static pressure, proceed as
follows;
1. With clean filters in the furnace, use a draft gauge (inclined
manometer) to measure the static pressure of the return
duct at the inlet of the furnace. (Negative Pressure)
2. Measure the static pressure of the supply duct. (Positive
Pressure)
3. The difference between the two numbers is .4” w.c.
Содержание DVC80603B
Страница 47: ...47 THIS PAGE LEFT INTENTIONALLY BLANK...