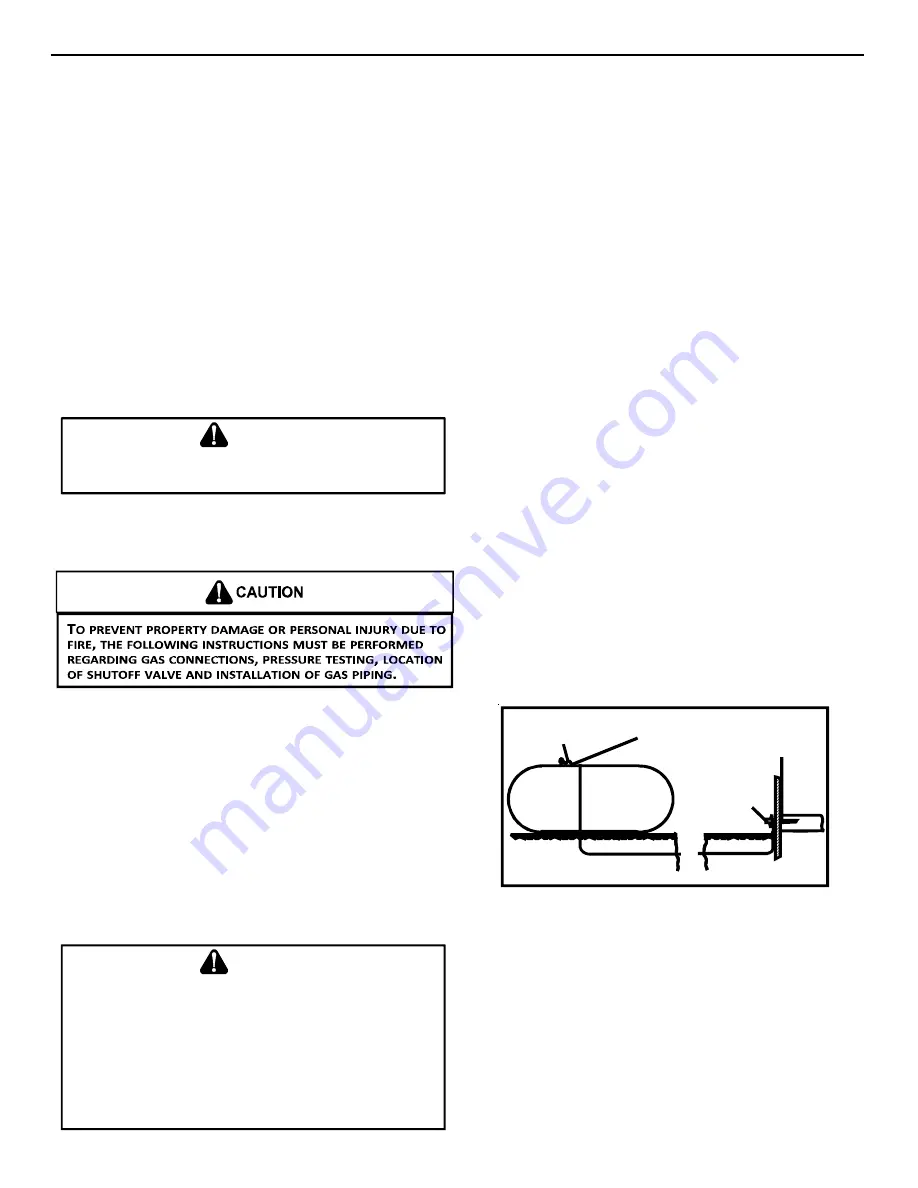
21
C
OUNTERFLOW
I
NSTALLATIONS
When the gas piping enters through the left side of the furnace,
the installer must supply a straight pipe and a 90 degree elbow
to reach the exterior of the furnace.
A ground joint union, drip leg and manual shutoff valve must
also be supplied by the installer. In most cases, the installer
may also need to supply a transition piece from ½” to another
pipe size. When the gas piping enters through the right side of
the furnace, the installer must supply the following fittings (start-
ing at the gas valve):
•
Close Nipple
•
90 Degree Elbow
•
Straight Pipe to Reach Exterior of Furnace.
G
AS
P
IPING
C
HECKS
Before placing unit in operation, leak test the unit and gas con-
nections.
T
O
AVOID
THE
POSSIBILITY
OF
EXPLOSION
OR
FIRE
,
NEVER
USE
A
MATCH
OR
OPEN
FLAME
TO
TEST
FOR
LEAKS
.
WARNING
Check for leaks using an approved chloride-free soap and wa-
ter solution, an electronic combustible gas detector, or other
approved testing methods.
NOTE:
Never exceed specified pressures for testing. Higher
pressure may damage the gas valve and cause subsequent
overfiring, resulting in heat exchanger failure.
Disconnect this unit and shutoff valve from the gas supply pip-
ing system before pressure testing the supply piping system
with pressures in excess of 1/2 psig (3.48 kPa).
This unit must be isolated from the gas supply system by clos-
ing its manual shutoff valve before pressure testing of gas sup-
ply piping system with test pressures equal to or less than 1/2
psig (3.48 kPa).
P
ROPANE
G
AS
T
ANKS
AND
P
IPING
I
F
THE
GAS
FURNACE
IS
INSTALLED
IN
A
BASEMENT
,
AN
EXCAVATED
AREA
OR
CONFINED
SPACE
,
IT
IS
STRONGLY
RECOMMENDED
TO
CONTACT
A
PROPANE
SUPPLIER
TO
INSTALL
A
GAS
DETECTING
WARNING
DEVICE
IN
CASE
OF
A
GAS
LEAK
.
S
INCE
PROPANE
GAS
IS
HEAVIER
THAN
AIR
,
ANY
LEAKING
GAS
CAN
SETTLE
IN
ANY
LOW
AREAS
OR
CONFINED
SPACES
.
P
ROPANE
GAS
ODORANT
MAY
FADE
,
MAKING
THE
GAS
UNDETECTABLE
EXCEPT
WITH
A
WARNING
DEVICE
.
•
•
WARNING
A gas detecting warning system is the only reliable way to
detect a propane gas leak. Rust can reduce the level of odorant
in propane gas. Do not rely on your sense of smell. Contact a
local propane gas supplier about installing a gas detecting
warning system. If the presence of gas is suspected, follow
the instructions on Page 3 of this manual.
All propane gas equipment must conform to the safety stan-
dards of the National Board of Fire Underwriters, NBFU Manual
58.
For satisfactory operation, propane gas pressure must be 10
inch WC at the furnace manifold with all gas appliances in
operation. Maintaining proper gas pressure depends on three
main factors:
1. Vaporization rate, depending on temperature of the liquid,
and “wetted surface” area of the container or containers.
2. Proper pressure regulation. (Two-stage regulation is
recommended for both cost and efficiency).
3. Pressure drop in lines between regulators, and between
second stage regulator and the appliance. Pipe size will
depend on length of pipe run and total load of all
appliances.
Complete information regarding tank sizing for vaporization, rec-
ommended regulator settings, and pipe sizing is available from
most regulator manufacturers and propane gas suppliers.
Since propane gas will quickly dissolve white lead and most
standard commercial compounds, special pipe dope must be
used. Shellac-based compounds resistant to the actions of
liquefied petroleum gases such as Gasolac
®
, Stalactic
®
,
Clyde’s
®
or John Crane
®
are satisfactory.
Refer to the following illustration for typical propane gas instal-
lations and piping.
200 PSIG
Maximum
5 to 15 PSIG
(20 PSIG Max.)
Continuous
11" W.C.
Second Stage
Regulator
First Stage
Regulator
Propane Gas Installation (Typ.)
Содержание DVC80603B
Страница 47: ...47 THIS PAGE LEFT INTENTIONALLY BLANK...