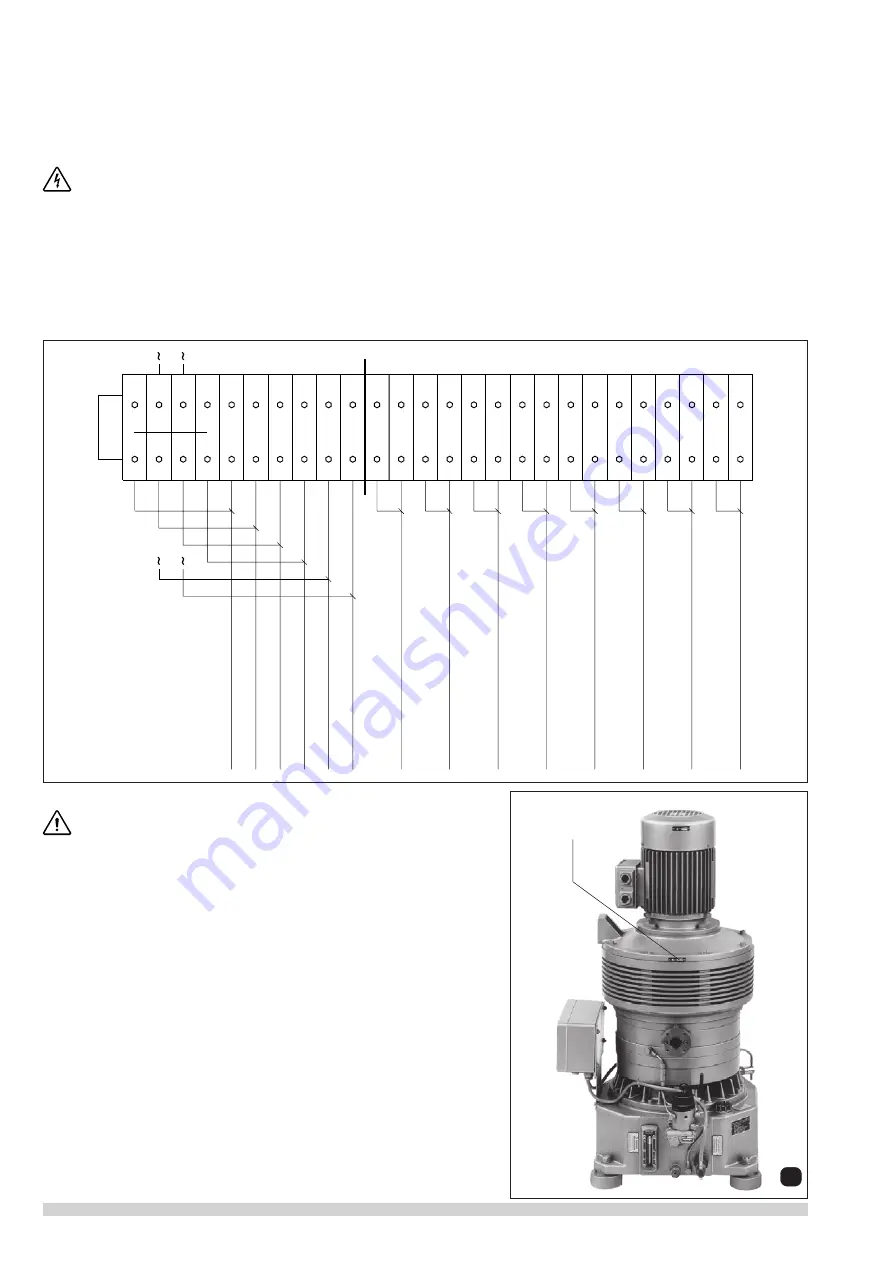
- 6 -
1
2
3
4
5
6
7
8
9
10 11 12 13 14 15 16 17 18 19 20 21 22 23 24 25 26
X 1
4
O
4.2 Electrical installation
4.2.1 General
Compare the electrical data of the motor and control system with available mains supply (type of current, voltage, supply frequency,
permitted amperage) (see data plate (N) in D 140 and D 141). Connect pumps via a motor starter to protect the motor, and
standards relating to strain relief of the connecting cable should be complied with.
We recommend the use of motor starter with thermal and magnetic overload protection. A temporary overload may occur during
a cold start.
The electrical installation may only be made by a qualified electrician under the observance of EN 60204. The main
switch must be planned through the operator.
The approximate values for setting motor overload protection should be obtained from the motor manufacturer or motor
nameplate.
4.2.2 Electrical connections for motor and control of monitoring systems
All electrical connections for the motor and for the control of the monitoring systems are housed in terminal boxes. Each conductor
terminal is numbered, and all connections for motor and monitoring elements are allocated a specific number (see circuit diagram).
Connection numbers must be observed during refitting or repair work to simplify detection of causes of faults.
4.2.3 Terminal box Connections
Suction valve
Bleeding valve
V
alve flushing unit
V
alve fr
esh oil
V
alve oil mist separator
Reserve
Reserve
Reserve
Level pr
e-separator
Level flushing liquid
Reserve
Level oil mist separator
Level fr
esh oil VL
V
Level fr
esh oil flushing
4.3 Initial Operation
Warning –> Start-up with pipework
At start-up, severe damage may occur if there is debris in the pipework.
We therefore recommend a vacuum tight inlet filter of 5 micron rating is
installed for start-up.
Start the pump briefly to check the direction of rotation (see arrow (
O
)).
Warning.
When handling moist and aggressive media, the vacuum pump
must be operated against the closed suction side but open bleed valve
(accessory) before and after the process. Pre-run and post-run last about 20
to 30 minutes. The pump is brought to operating temperature during the pre-
run to prevent condensation of moist media inside the pump. Residues are
flushed out by the post-run and are purged before stoppage. Pre-run and post-
run take place automatically when the selector switch is set accordingly.