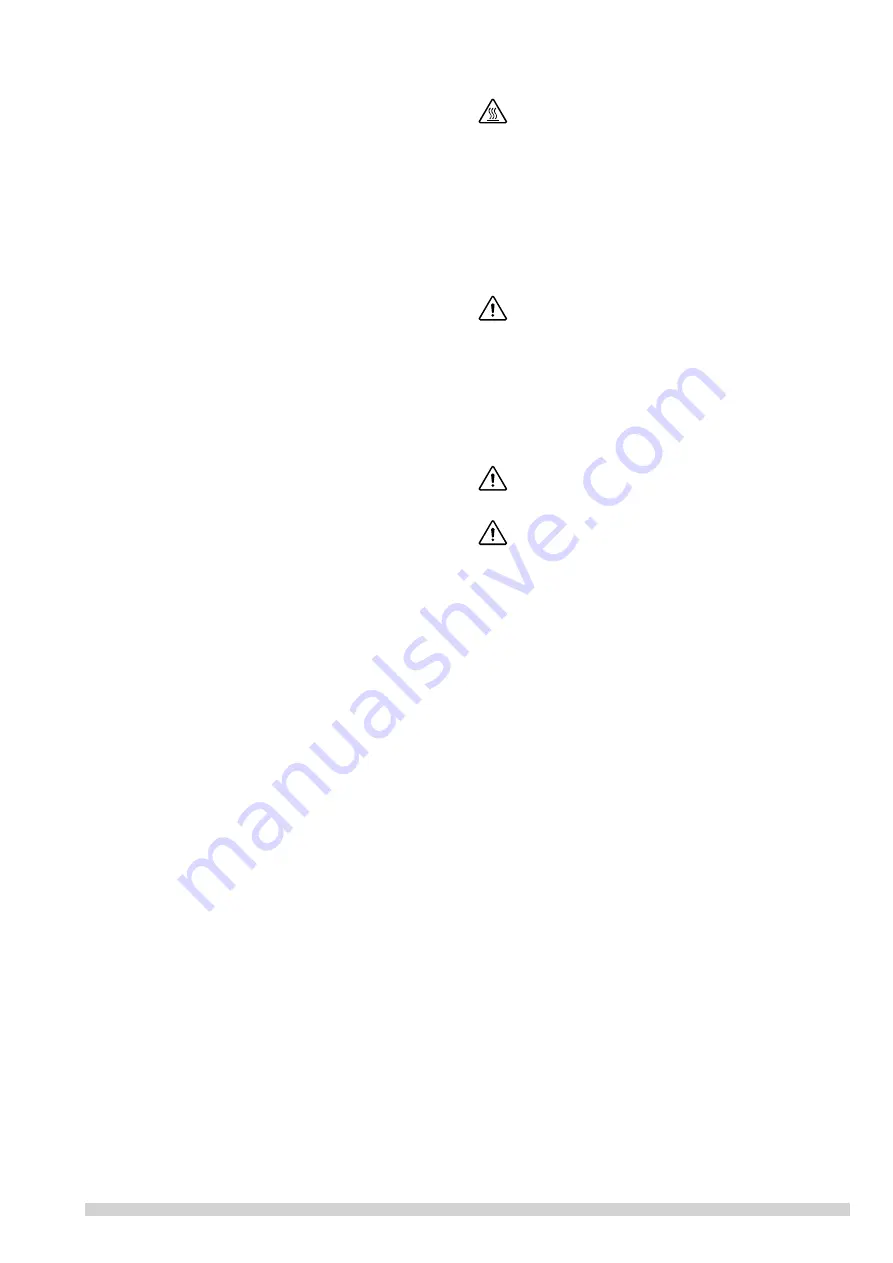
- 5 -
4. Installation and Commissioning
4.1 Mechanical installation
4.1.1 Installation
Pumps that have reached operating temperature may
have a surface temperature of more than 70°C de-
pending on a set temperature at the thermostat. WARNING!
Do Not Touch.
VLV vacuum pumps do not vibrate and do not require special
floor fixings. Care should be taken to align the pump correctly
during installation. Cooling air inlet and outlet must be at least
0.5 m from the nearest wall. The ambient temperature in the
installation area should not exceed 35°C. The pump should be
easily accessible for maintenance and repairs.
The VLV pumps can only be operated reliably if they are
installed vertically.
For operating and installation follow any relevant
national standards that are in operation.
4.1.2 Suction side
Connect suction pipe to A (see D 140 and D 141) (standard ISO
flange). This pipe should be as short as possible. If it is longer
than about 5 m, it must have a greater nominal width than the
pump flange. Pumps must not be stressed during installation
(intermediate expansion joints may be fitted). Appropriate
separators should be installed on the suction side for protection
against solids and liquids (accessories).
Solid particles of more than 5 µm and liquid slugs are
able to destroy the compressor stages.
4.1.3 Exhaust
The exhaust resistance within the pipework should
not exceed 0.3 bar overpressure.
3.2.9 Optional extras
Suction side:
• Non-return valve
• Bleed valve
• Solid/liquid separator
Exhaust side:
• Halar-coated oil mist separator
General:
• Electric control system with pre-run and post-run
• Flushing system
• Auxiliary oil reservoir
• Automatic condensate outlet
• Gauge for separator monitoring
3.2.10 Typical applications
• Vacuum for printed circuit board production
• Carbonisation in drink production
• Vacuum packaging of moist products
• Vacuum cooling of foods
• Vacuum filtration
• Vacuum drying
• Vacuum crystallisation
• Thickening of liquids, juices and extracts
3.2.11 VLV pumps with Roots blowers
VLV machines may be used as auxiliary pumps in conjunction
with Roots blowers.
Suction capacities of up to 1,500 m³/hr and final pressures of up
to 1 x 10
-4
mbar (abs). are achieved according to size and
number of Roots blowers.
3.2.12 Advantages of the VLV range
• Simple installation, no water supply, low motor power
• consumables, no coolant required
• minimum problems of disposal due to minimum
consumables
• environment-friendly oil mist separator
3.2.13 Conditions for use of VLV vacuum pumps
• suction medium should be free from liquids and solids
• pump should be installed, if possible with intake and deliv-
ery pipe draining away from the pump. This prevents
condensate returning to the pump.
• Pre-run and post-run of the pump always necessary when
handling aggressive media. Pre-run and post-run require
closed suction valve but open bleed valve at about 80 mbar
intake pressure. The pump is brought to operating tem-
perature to avoid condensation in the cold pump (pre-run).
• After the process, aggressive residues are flushed out by
the injected fresh oil, and the pump is purged before a
stoppage (post-run). The pre-run and post-run last about
20 to 30 minutes.
• Adequate pump cooling must be provided (see 4.1.1 Instal-
lation).
• Check whether ambient air is aggressive as aluminium and
brass parts may be corroded (avoided by coating and
special steel parts).
3.2.14 VLV capability
Use of this pump is generally restricted by the following criteria:
1. Intake temperatures:
• 60°C
(low vacuum > 10 mbar)
• 100°C
(high vacuum < 10 mbar)
2. Intake pressures
3. Suction capacity
4. Product restrictions:
• pump corrosion
• reaction product - oil
• reaction product - metal