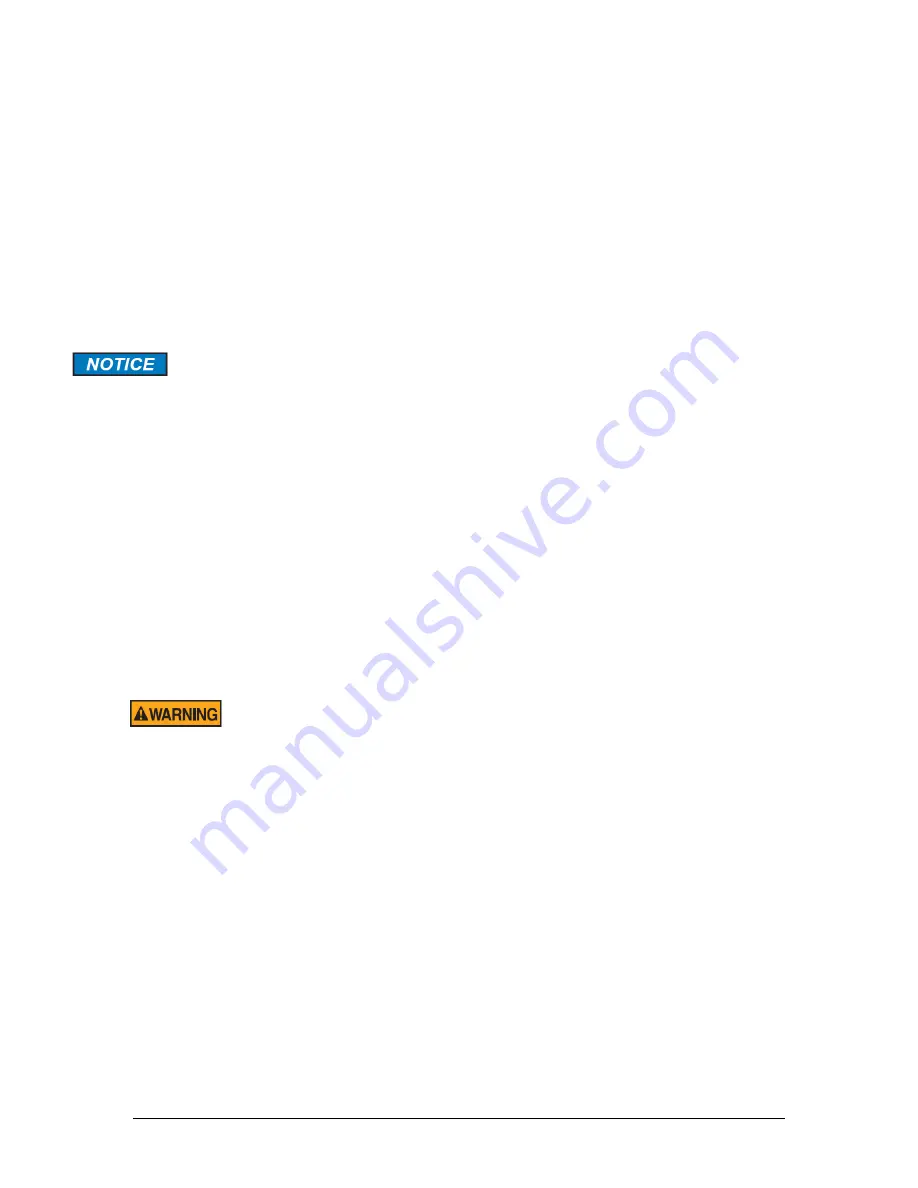
Revision 5
119
August 2021
Once the lamp has been switched off, it will not restart for a period of time as ignition of a hot
lamp can cause serious problems. If the lamp is turned off or is no longer lit, it may be worthwhile
to wait for 15-20 minutes before restarting it. If the lamp does not start after the cool down period,
and it has been more than six months since the lamp has been replaced, then it should be
replaced. The normal lifespan of a UV Source Lamp
is about 10 months (standard lifespan lamp
BA7195) or 20 months (long lifespan lamp BA7532), but longer life spans are possible in
circumstances where the restart count is low.
If the lamp was replaced <8 months (standard lifespan lamp BA7195) or <16 months ago (long
lifespan lamp BA7532), it is advisable to investigate the other potential causes listed in Table
33 prior to replacing the lamp.
The lamp life is inversely proportional to the number of restarts on a particular lamp.
The lamp should ONLY be turned off when absolutely necessary to preserve lamp
lifespan.
An
iris
is installed on the lamp holder between the lamp and the fluid holder. The iris is preset
at the factory with clean optics and a new lamp to obtain 28,000 counts at a <100 ms integration
period. The setting of the iris is only to be changed in extreme situations. Please contact
Galvanic Applied Sciences Inc. prior to making any changes to the iris position.
To change the UV Source Lamp, follow the procedure below.
1. Place the analyzer in Offline mode by toggling the
Online / Offline
control toggle
(Section 4.3.1) on the
Analysis 2
panel to
Offline
(red).
2. Place the analyzer in back purge mode by pressing the F6 key on the keypad OR by
placing the X in the
Back Purge
check box on the
Analysis 1
panel.
3. Access the purged control cabinet following proper user company and/or regulatory
agency procedure.
The control cabinet door may NOT be opened while the analyzer is
energized UNLESS the area is known to be non-hazardous. Observe all the
warning labels on the analyzer enclosures. The EPCU must be bypassed
prior to opening the control cabinet door. Refer to section 3.3.
4. Lift the fuse terminal tab opening the terminal block and disconnect the UV Lamp
Power Supply fuse, located at ACTS:28, next to the cell heater fuse tab indicated in
Figure 74. Alternatively, place the UV Lamp power switch to the Off position. The
location of the lamp power switch is indicated in Figure 75.
Содержание 943-TGS-CE
Страница 137: ...Revision 5 137 August 2021 Figure 84 Oven Cabinet Details...
Страница 138: ...Revision 5 138 August 2021 Figure 85 Control Cabinet Door Closed...
Страница 139: ...Revision 5 139 August 2021 Figure 86 Control Cabinet Door Removed...
Страница 140: ...Revision 5 140 August 2021 Figure 87 Power Steam Air Signals Connection Details...
Страница 141: ...Revision 5 141 August 2021 Figure 88 AC Wiring Schematic...
Страница 142: ...Revision 5 142 August 2021 Figure 89 DC Signals and Wiring Diagram...
Страница 143: ...Revision 5 143 August 2021 Figure 90 Flow Diagram...
Страница 144: ...Revision 5 144 August 2021 Figure 91 Control and Oven Cabinets Interconnect Wiring...