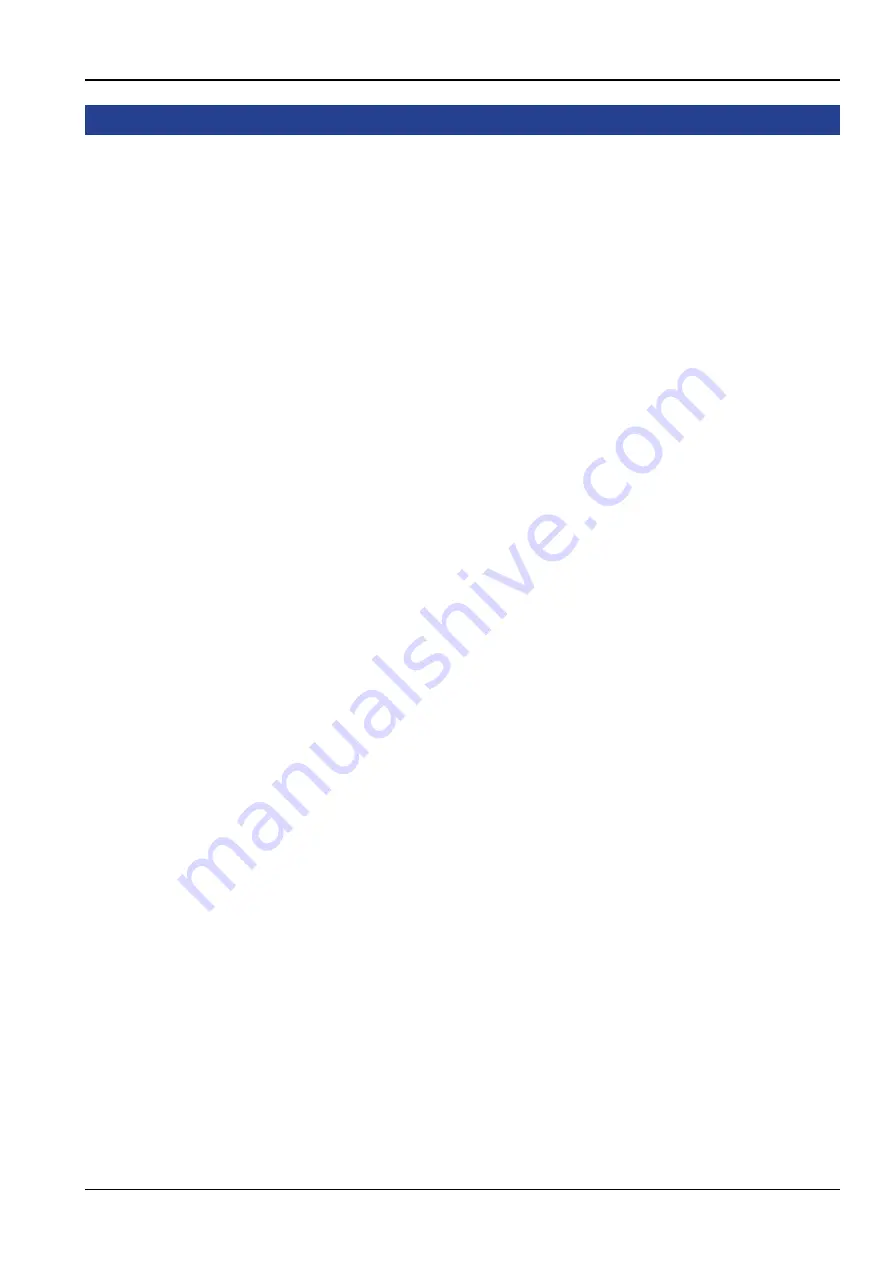
VMP-IOMM-2018-2
Fulton Ltd
Page 19
INSTALLATION - 2
2.7.1
GLOSSARY OF WATER SUPPLY TERMS
Dissolved Oxygen:
Oxygen that is dissolved in
the feedwater will cause the steel in the boiler and
the feedwater system to be attacked by the water
in a manner described as “pitting”. The pits that are
produced can vary from tiny depressions to holes large
enough to penetrate the boiler metal and are usually
covered with tubercles of iron oxide. Once pitting
starts, it may be extremely hard to arrest. Pitting can
proceed at a surprisingly rapid rate and can occur
not only in the boiler proper, but also in pre-boiler
equipment such as economizers, feedwater tanks, and
feedwater lines.
Suspended Solids:
Suspended solids are the
undissolved matter in water, including dirt, silt,
vegetation, iron oxides, and any other insoluble matter.
Normally suspended solids are expressed in terms
of turbidity. Suspended solids may also deposit in
low velocity areas and create fouling. In line filters, or
various types of pretreatment can be used to lower
the suspended solids level. Periodic blowdowns will
eliminate suspended solids.
Alkalinity:
Alkalinity is the capacity of a water to
neutralize acids. Common water alkalinities consist of
bicarbonate, carbonates, hydroxide, phosphate, and
silicate. These alkalinities, especially bicarbonates
and carbonates, break down to form carbon dioxide
in steam, which is a major factor in the corrosion on
condensate lines. High alkalinity also causes foaming
and carry over in boilers. Both foaming and carry over
cause erratic boiler operation. The reason for the high
alkalinity should be determined. It may result from lack
of sufficient blow off. The source of alkalinity may be
due to an overdose of alkaline internal water treatment
chemical.
pH:
pH is a measure of the degree of acid or base of
solution. A pH range of 8.5-10.5 will have little influence
on the corrosion rate of carbon steel. A low pH can
result in corrosion of metals, while a high pH can result
in scale formation or caustic embrittlement. In order
to control boilers and equipment used for the external
treatment of make-up water, it is essential that reliable
pH measurements be made. RO/DI water will have a
pH of 6.0 - 6.5 and will require neutralization if used in
a carbon steel vessel. It is critical that the boiler pH be
alkaline (8.5-10.5) whenever water is in the boiler.
Chlorides:
If chloride levels are high enough to
cause severe corrosion, they can be controlled by
limiting the cycles of concentration and increasing
boiler blowdowns. Corrosion from chlorides can also
be controlled by increasing the amount of corrosion
inhibitor, or changing to a more effective inhibitor.
Oil:
Oil is not a natural constituent of boiler water;
still it can frequently enter a system through leaks in
a condenser or other heat exchanger. Oil can also
enter a system through the lubrication of steam driven
reciprocating equipment. Whatever the source, the
presence of oil in boiler water is undesirable. Oil can
act as a binder to form scale. In high heat-transfer
areas oil can carbonize and further contribute to
the formation of scale and low pH. Foaming is one
indication of oil in boiler water. Its presence can also
be confirmed by first shaking a bottle containing
boiler water. If oil is present foam will result. Often oil
in boiler water will originate in the condensate. This
contaminated condensate should be directed to the
sewer until the source of the oil is determined and
corrective steps taken.
Iron (oxides):
Iron in any of its oxide or complex forms
is undesirable in boiler water. Iron in its various forms
can originate in the raw water makeup, condensate
return water, or form directly in the boiler as a result of
corrosion. It can concentrate in the boiler and it tends
to collect in stagnant areas.
Water Hardness:
Water hardness is the measure of
calcium and magnesium content as calcium carbonate
equivalents. Water hardness is a primary source of
scale in boiler equipment. Hardness is removed by
softening.
Periodically, the ion exchange resin bed requires
regeneration by flushing through with a brine solution
followed by rising with fresh water. The interval
between regeneration is dependent upon the raw water
hardness and flow rate.
In all cases the water hardness should be tested
periodically and prior to starting the generator to
ensure efficient operation of the softener. Unsoftened
water should not be allowed to enter the steam
generator unless sufficient scale inhibitor chemical is
used.
Feedwater:
Feedwater is the combination of fresh
makeup and returning condensate that is pumped to
the boiler.
Condensate:
Condensate is condensed steam that
is normally low in dissolved solids. Hence, it does
not contribute to the dissolved solid content of the
feedwater. In addition, condensate is very expensive to
waste. It’s been chemically treated, heated, pumped,
converted to steam, and condensed.
Содержание VMP Series
Страница 8: ...VMP IOMM 2018 2 Fulton Ltd Page VIII...
Страница 25: ...VMP IOMM 2018 2 Fulton Ltd Page 17 INSTALLATION 2 Figure 10 Electrical Customer Terminal Connections...
Страница 30: ...VMP IOMM 2018 2 Fulton Ltd Page 22...
Страница 66: ...VMP IOMM 2018 2 Fulton Ltd Page 58...
Страница 100: ...VMP IOMM 2018 2 Fulton Ltd Page 92...
Страница 102: ...VMP IOMM 2018 2 Fulton Ltd Page 94 APPENDIX C...