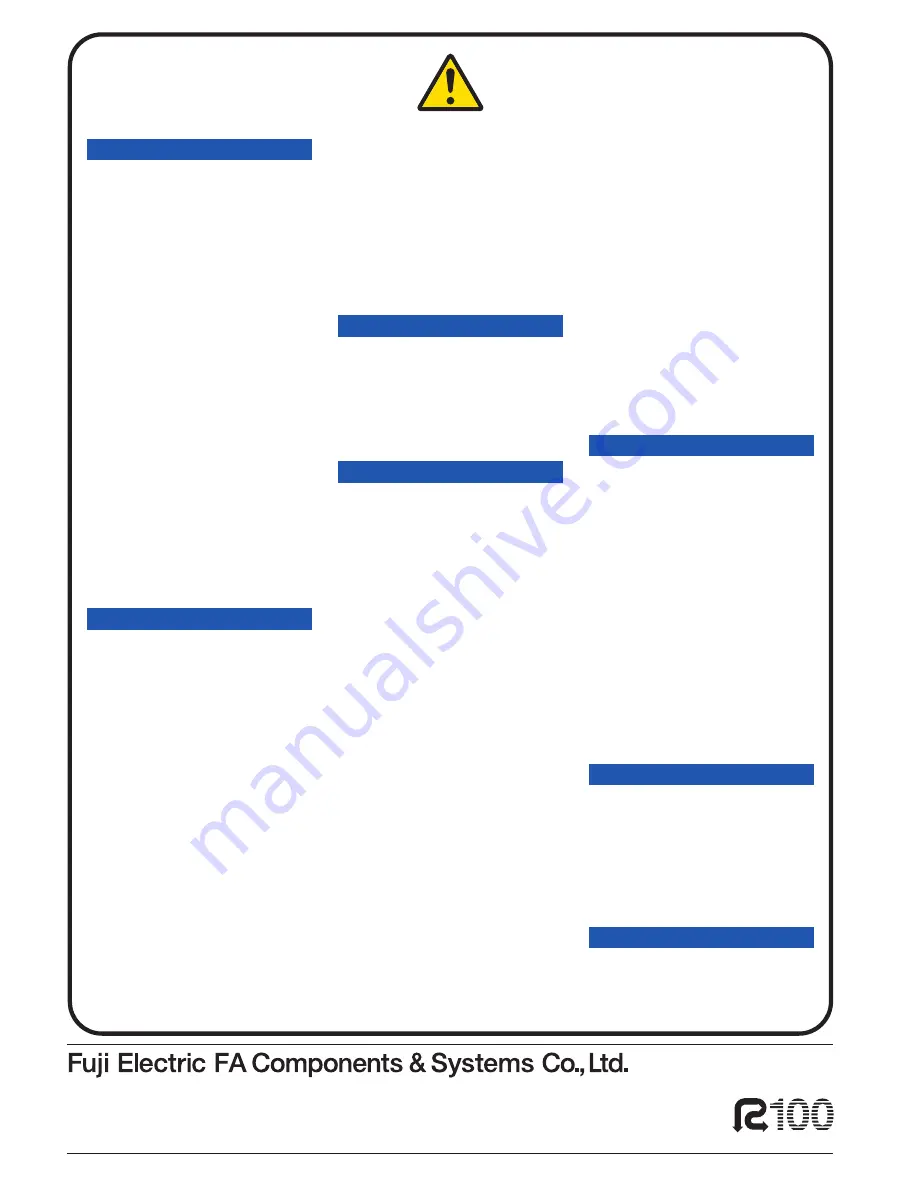
NOTES
When running general-purpose motors
•
Driving a 460V general-purpose motor
When driving a 400V general-purpose motor with
an inverter using extremely long cables, damage to
the insulation of the motor may occur. Use an
output circuit filter (OFL) if necessary after checking
with the motor manufacturer. Fuji's motors do not
require the use of output circuit filters because of
their reinforced insulation.
•
Torque characteristics and temperature rise
When the inverter is used to run a general-purpose
motor, the temperature of the motor becomes
higher than when it is operated using a commercial
power supply. In the low-speed range, the cooling
effect will be weakened, so decrease the output
torque of the motor. If constant torque is required in
the low-speed range, use a Fuji inverter motor or a
motor equipped with an externally powered
ventilating fan.
•
Vibration
When the motor is mounted to a machine,
resonance may be caused by the natural
frequencies, including that of the machine.
Operation of a 2-pole motor at 60Hz or more may
cause abnormal vibration.
* Study use of tier coupling or dampening rubber.
* It is also recommended to use the inverter jump
frequency control to avoid resonance points.
•
Noise
When an inverter is used with a general-purpose
motor, the motor noise level is higher than that with
a commercial power supply. To reduce noise, raise
carrier frequency of the inverter. High-speed
operation at 60Hz or more can also result in more
noise.
When running special motors
•
High-speed motors
When driving a high-speed motor while setting the
frequency higher than 120Hz, test the combination
with another motor to confirm the safety of high-
speed motors.
•
Explosion-proof motors
When driving an explosion-proof motor with an
inverter, use a combination of a motor and an
inverter that has been approved in advance.
•
Submersible motors and pumps
These motors have a larger rated current than
general-purpose motors. Select an inverter whose
rated output current is greater than that of the
motor.
These motors differ from general-purpose motors in
thermal characteristics. Set a low value in the
thermal time constant of the motor when setting the
electronic thermal facility.
•
Brake motors
For motors equipped with parallel-connected
brakes, their braking power must be supplied from
the primary circuit (commercial power supply). If the
brake power is connected to the inverter power
output circuit (secondary circuit) by mistake,
problems may occur.
Do not use inverters for driving motors equipped
with series-connected brakes.
•
Geared motors
If the power transmission mechanism uses an oil-
lubricated gearbox or speed changer/reducer, then
continuous motor operation at low speed may
cause poor lubrication. Avoid such operation.
•
Synchronous motors
It is necessary to use software suitable for this
motor type. Contact Fuji for details.
•
Single-phase motors
Single-phase motors are not suitable for inverter-
driven variable speed operation. Use three-phase
motors.
* Even if a single-phase power supply is available,
use a three-phase motor as the inverter provides
three-phase output.
Environmental conditions
•
Installation location
Use the inverter in a location with an ambient
temperature range of -10 to 50
˚
C(14 to 122
˚
F).
The inverter and braking resistor surfaces become
hot under certain operating conditions. Install the
inverter on nonflammable material such as metal.
Ensure that the installation location meets the
environmental conditions specified in "Environment"
in inverter specifications.
Combination with peripheral devices
•
Installing a molded case circuit
breaker (MCCB)
Install a recommended molded case circuit breaker
(MCCB) or a groud-fault circuit interrupter (GFCI) in
the primary circuit of each inverter to protect the
wiring. Ensure that the circuit breaker capacity is
equivalent to or lower than the recommended
capacity.
•
Installing a magnetic contactor (MC)
in the output (secondary) circuit
If a magnetic contactor (MC) is mounted in the
inverter's secondary circuit for switching the motor
to commercial power or for any other purpose,
ensure that both the inverter and the motor are fully
stopped before you turn the MC on or off. Remove
the surge killer integrated with the MC.
•
Installing a magnetic contactor (MC)
in the input (primary) circuit
Do not turn the magnetic contactor (MC) in the
primary circuit on or off more than once an hour as
an inverter fault may result. If frequent starts or
stops are required during motor operation, use
FWD/REV signals.
•
Protecting the motor
The electronic thermal facility of the inverter can
protect the motor. The operation level and the motor
type (general-purpose motor, inverter motor) should
be set. For high-speed motors or water-cooled
motors, set a small value for the thermal time
constant to protect the motor.
If you connect the motor thermal relay to the motor
with a long cable, a high-frequency current may
flow into the wiring stray capacitance. This may
cause the relay to trip at a current lower than the
set value for the thermal relay. If this happens,
lower the carrier frequency or use the output circuit
filter (OFL).
•
Discontinuance of power-factor correcting capacitor
Do not mount power factor correcting capacitors in
the inverter (primary) circuit. (Use the DC
REACTOR to improve the inverter power factor.) Do
not use power factor correcting capacitors in the
inverter output circuit (secondary). An overcurrent
trip will occur, disabling motor operation.
•
Discontinuance of surge killer
Do not mount surge killers in the inverter output
(secondary) circuit.
•
Reducing noise
Use of a filter and shielded wires are typical
measures against noise to ensure that EMC
Directives are met.
•
Measures against surge currents
If an overvoltage trip occurs while the inverter is
stopped or operated under a light load, it is
assumed that the surge current is generated by
open/close of the phase-advancing capacitor in the
power system.
We recommend connecting a DC REACTOR to the
inverter.
•
Megger test
When checking the insulation resistance of the
inverter, use a 500V megger and follow the
instructions contained in the Instruction Manual.
Wiring
•
Wiring distance of control circuit
When performing remote operation, use the twisted
shield wire and limit the distance between the
inverter and the control box to 65.6ft(20m).
•
Wiring length between inverter and motor
If long wiring is used between the inverter and the
motor, the inverter will overheat or trip as a result of
overcurrent (high-frequency current flowing into the
stray capacitance) in the wires connected to the
phases. Ensure that the wiring is shorter than
164ft(50m). If this length must be exceeded, lower
the carrier frequency or mount an output circuit filter
(OFL).
•
Wiring size
Select cables with a sufficient capacity by referring
to the current value or recommended wire size.
•
Wiring type
Do not use multicore cables that are normally used
for connecting several inverters and motors.
•
Grounding
Securely ground the inverter using the grounding
terminal.
Selecting inverter capacity
•
Driving general-purpose motor
Select an inverter according to the applicable motor
ratings listed in the standard specifications table for
the inverter. When high starting torque is required
or quick acceleration or deceleration is required,
select an inverter with a capacity one size greater
than the standard.
•
Driving special motors
Select an inverter that meets the following condition:
Inverter rated current > Motor rated current.
Transportation and storage
When transporting or storing inverters, follow the
procedures and select locations that meet the
environmental conditions that agree with the
inverter specifications.
Printed in Japan 2007-7 (G07/G07) CM 30 FIS
Printed on 100% recycled paper
Fuji Electric Corp. of America
Information in this catalog is subject to change without notice.
47520 Westinghouse Drive Fremont, CA 94539, U.S.A.
Tel.+1-510-440-1060 Fax.+1-510-440-1063
http://www.fujielectric.com
Содержание FRN001E1E-2U
Страница 1: ...MEH531 High Performance Compact Inverters...
Страница 38: ...MEMO...
Страница 39: ...MEMO...