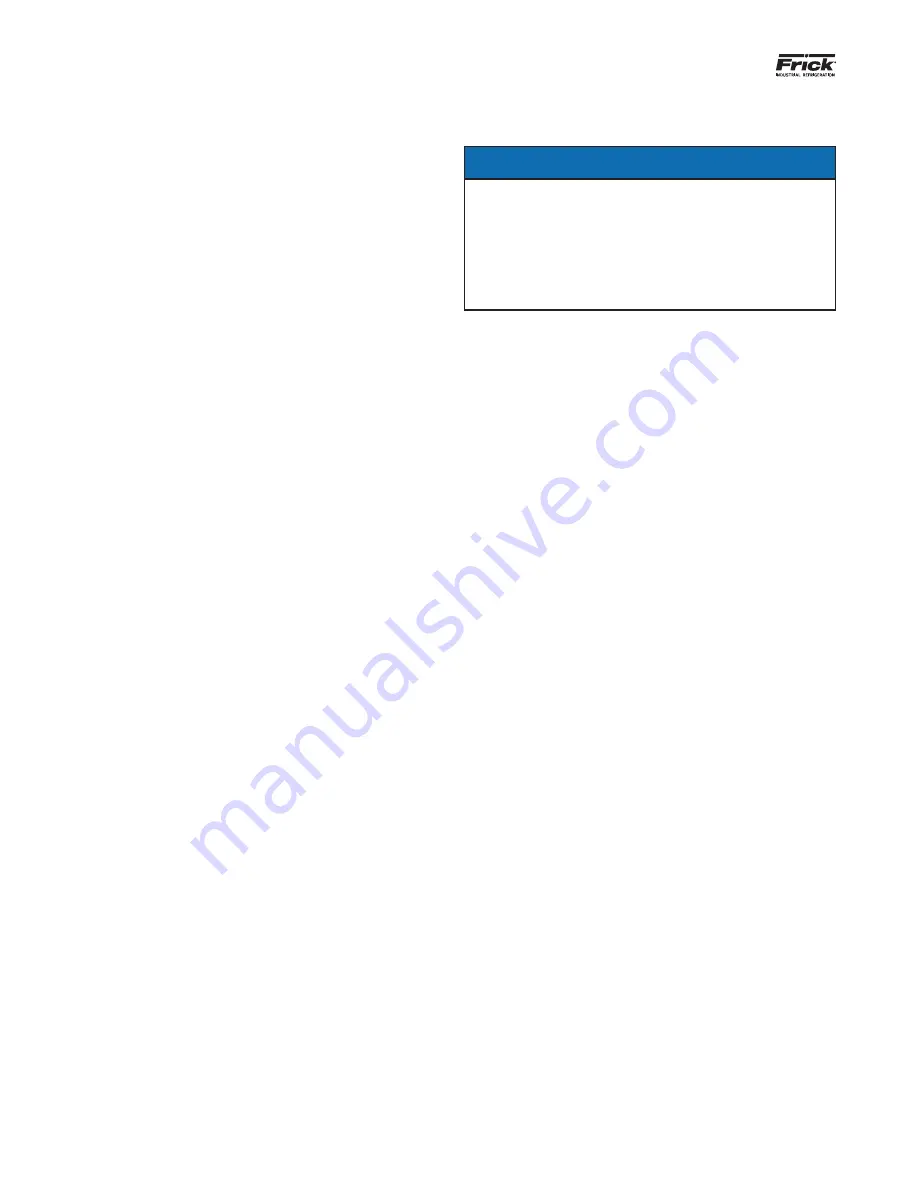
140.925-IOM (APR 2019)
Page 28
XLP3 EVAPORATIVE CONDENSERS
MAINTENANCE
L.E.D. Status Codes
•
L.E.D. on steady:
Indicates normal operation.
•
Steady one second flashing:
Indicates dirty probes,
reading in the capacitance mode. The unit will still operate
but will give the following status code of 1 second on, 1
second off (steady 1 second flashing). This status code
continue until the probes are cleaned and the power has
been reset. Note: No other status codes will be displayed
until the dirty probes are cleaned.
•
Two flashes and off for 5 seconds:
Indicates make-up
valve ran for more than 1 hour. The unit will continue to fill,
with the following status code of 1 second on, 1 second off,
1 second on and then off for 5 seconds before repeating.
This status will continue until power has been reset.
Possible causes: leaking tank, obstructed fill / defective
valve or reduced flow rate.
•
Three flashes and off for 5 seconds:
Indicates shorted
probes or highly conductive water. The unit will continue
to operate but will give the following status code of 1
second on, 1 second off, 1 second on, 1 second off, 1
second on and then off for 5 seconds before repeating.
This status will continue until the water is diluted or the
short is removed from the probes and power is reset.
•
Four flashes and off for 5 seconds:
Indicates black
probe (P6) reads covered, but white probe (P5) does not
read covered (white should also be covered because it
is longer than the black). This will cause the fill solenoid
valve to short cycle and lead to premature failure of the
fill valve. The unit will short cycle and give the status code
of 1 second on, 1 second off, 1 second on, 1 second off,
1 second on, 1 second off, 1 second on and then off for 5
seconds before repeating. The unit will continue to short
cycle until the condition has been corrected (clean white
probe) and the power reset.
•
L.E.D. does not come on after power up or resetting
power:
Indicates unit inoperative.
CORROSION PROTECTION
Frick products are constructed of corrosion-resistant materi-
als. Other materials listed below are used in the equipment
construction:
•
Galvanized Steel Components:
Inspect the galvanized
steel components for blemishes or corrosion. Wire brush
and recoat the affected areas with a cold galvanizing
compound such as zinc rich compound (ZRC).
•
Thermosetting Hybrid Polymer Components:
Galvanized
steel components protected with the thermosetting hybrid
polymer can be scratched, scraped, or blemished. To
touch up these areas use a repair kit (Frick Part # 160133)
available from your local Frick Representative.
•
Stainless Steel Components:
Inspect stainless steel
components for signs of blemishes or corrosion. See “Long
Term Care of Stainless Steel” on page 30 for cleaning and
care instructions.
•
TripleGuard® Corrosion Protection System:
Inspect
components protected with the TripleGuard® Corrosion
Protection System for signs of deep scratches or blemishes,
especially in areas with field penetrations. Touch these up
with 3M™ Windo-Weld™ Super Fast Urethane which is
available through your local Frick Representative (Frick Part
# RK1015).
NOTICE
Since the quality of the ambient air and make-up water
varies significantly from job site to job site, Frick strongly
recommends obtaining the services of a qualified water
treatment specialist prior to the initial start-up of the
evaporative cooling equipment. Additionally, to protect
against the risk of Legionella contamination, never
operate the cooling equipment without adequate
biological control.
Water Treatment
A proper water treatment program, administered under the
supervision of a competent water treatment specialist, is an
essential part of routine maintenance to ensure the safe opera-
tion and longevity of evaporative cooling equipment, as well as
other system components.
In evaporative cooling products, cooling is accomplished by
evaporating a small portion of the recirculating water as it
flows through the unit. As the water evaporates, the dissolved
solids originally present in the water remain behind and if not
controlled, the concentration of dissolved solids will increase
rapidly. This can lead to corrosion, scale or biological fouling
which may negatively affect heat transfer as well as the longevity
of system components.
•
Corrosion
– Red rust on steel components and white rust
on galvanized surfaces may affect the longevity of system
components.
•
Scale Formation
– Scale, typically a calcium or magnesium
based build-up, not only reduces heat transfer and system
efficiency, but also may lead to under deposit corrosion. If
scale is not controlled, it may continue building on critical
components such as the fill and severely impact thermal
performance.
•
Biological Fouling
– Slime and algae formations may
reduce heat transfer, promote corrosion, and harbor
pathogens such as Legionella.
Corrosion and Scale Control
• To control corrosion and scale, maintain the water
chemistry of the recirculating water within the parameters
listed in Table 5. The specific measures required vary from
system to system and are dependent on the chemistry of
the make-up water, the metallurgy of the piping and heat
transfer devices exposed to the recirculating water, and
the temperatures at which the system will be operating.
• Bleed/blowdown, the continuous flow of a small portion
of the recirculating water to a drain, is used to control
the concentration of dissolved solids. On rare occasions,
this may be adequate to control scale and corrosion.
More often, chemical scale and corrosion inhibitors are
necessary, which raise the allowable level of dissolved
solids without the risk of scale and corrosion.
• Keep the chemically treated water within the guidelines
given in Table 5. In cases where bleed/blowdown alone
is being employed for corrosion and scale control without
chemical treatment your water treatment specialist may
recommend more conservative limits than those shown in
Table 5.