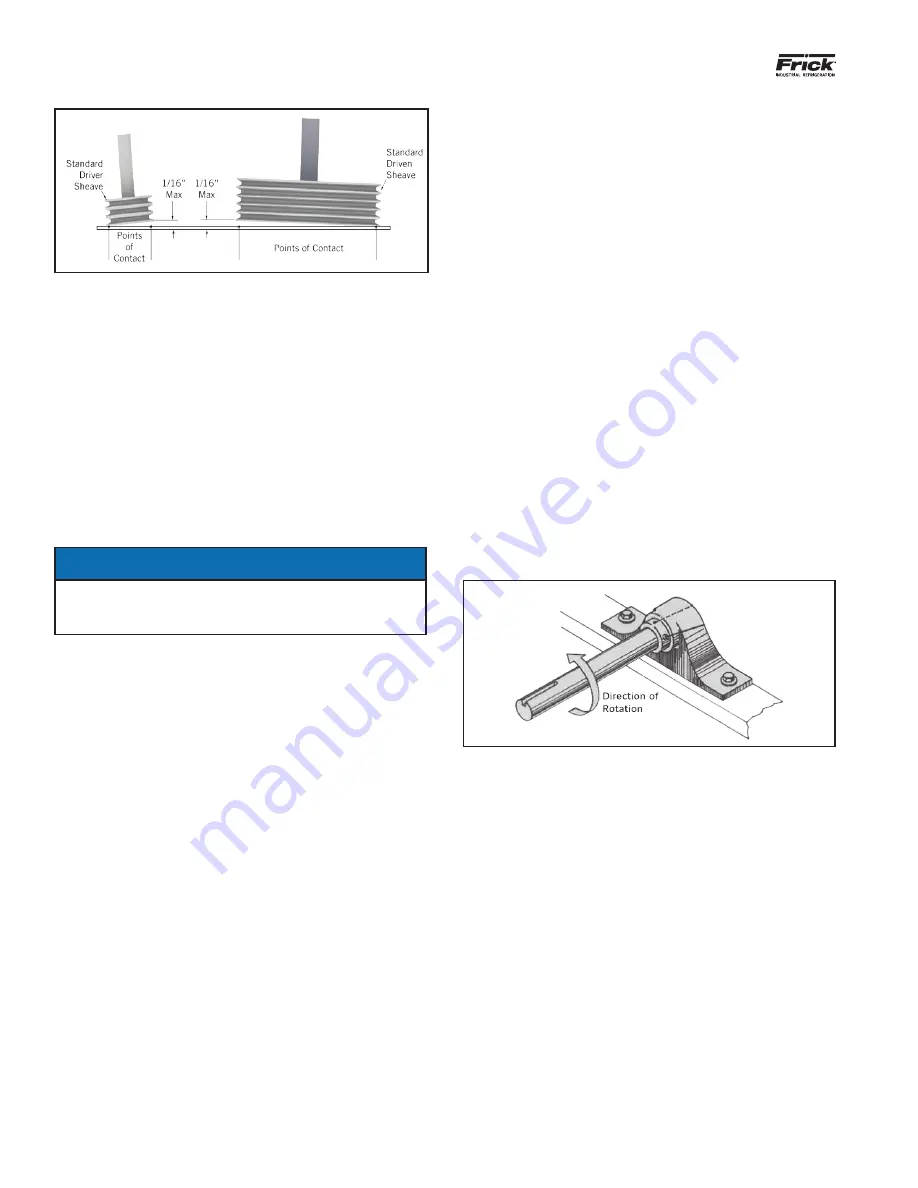
140.925-IOM (APR 2019)
Page 26
XLP3 EVAPORATIVE CONDENSERS
MAINTENANCE
Figure 24. Drive Alignment
Adjustable Motor Base
Coat the motor base slides and adjusting screws (refer to Figure
23) prior to start-up, every three months while in operation,
and following shutdown. Use good quality, corrosion inhibiting
grease such as one of those recommended for lubricating the
fan shaft bearings below.
Fan Motor Inspection & Maintenance
• Clean the outside of the motor at least quarterly to ensure
proper motor cooling.
• After prolonged shutdowns, check the motor insulation
with an insulation tester prior to restarting the motor.
• Check the motor voltage and current following start-up
and every three months while in operation.
NOTICE
Check to ensure the controls for the fan motor are set to
allow a maximum of six on-off cycles per hour to prevent
motor overload.
Fan Shaft Bearing Inspection & Maintenance
• For all units ordered with the Belt Drive Fan System, two
pillow block ball bearings support the fan shaft and are
provided with extended lube lines as standard on the XLP3
Evaporative Condenser. Each bearing is equipped with a
lubrication fitting and a locking collar to keep out moisture.
• Only lubricate the bearings with a manual grease gun or
Frick’s optional Automatic Bearing Greaser. Do not use
high-pressure grease guns since they may rupture the
bearing seals or the extended lubrication lines.
• Only lubricate the bearings with one of the following
compatible water resistant greases which are suitable for
ambient temperatures ranging from -65°F (-53.9°C) to
+250°F (121.1°C).
• Amoco - Rycon Premium #3
• Chevron - SRI
• Citgo - Polyurea MP2™
• Conoco - Polyurea 2™
• Exxon - Polyrex® EM
• Exxon - Unirex N™
• MobilGrease® - AW2
• Shell - Gadus S2 V100 3
• Shell - Gadus S3 T100 2
• SKF - LGHP2™
• Unocal 76 - Unilife Grease™
• Lubricate the bearings as follows:
•
Initial Start-Up:
Normally, no lubrication is required
since the bearings have been lubricated at the factory
prior to shipment. However, if the unit has been stored
at the job site for more than three months, both
bearings should be lubricated with new grease before
initial operation. When lubricating, purge the old grease
from the bearing by gradually adding grease until a bead
of new grease appears at the seal on the underside of
the bearing.
•
Seasonal Start-Up:
Purge the bearings with new
grease prior to start-up.
•
Operation:
Purge the bearings with new grease every
three months while in operation.
•
Extended Shutdown:
Purge the bearings with new
grease prior to any prolonged storage or downtime.
Locking Collars
Each eccentric locking collar should be checked quarterly to
ensure that the inner bearing race is secured to the fan shaft.
The locking collar can be set using the following procedure (see
Figure 25):
• Loosen the set screw.
• Using a drift pin or center punch, tap the collar (in the hole
provided) tangentially in the direction of rotation while
holding the shaft.
• Retighten the set screw.
Figure 25 — Locking Collar Assembly
Water Distribution System and Heat Transfer Section
Water is distributed through a corrosion resistant polyvinyl chlo-
ride (PVC) spray distribution system. The drift eliminators are
made of PVC, which requires no protection against rot, decay,
rust, or biological attack.
The inspection procedure is as follows:
• Shut off the fan and lock out and tag out the fan and pump
motors.
• Remove drift eliminators to allow a clear view of the spray
distribution system and nozzle patterns.
• Start the recirculating pump. Make sure the fan motor is
locked out and tagged out. Check to see if the nozzles are
all spraying consistently and producing the spray pattern
shown in Figure 26.
• Clean any nozzles that are clogged. If necessary, the
nozzle and rubber grommet may be removed for cleaning.
If additional cleaning is necessary the branch may be