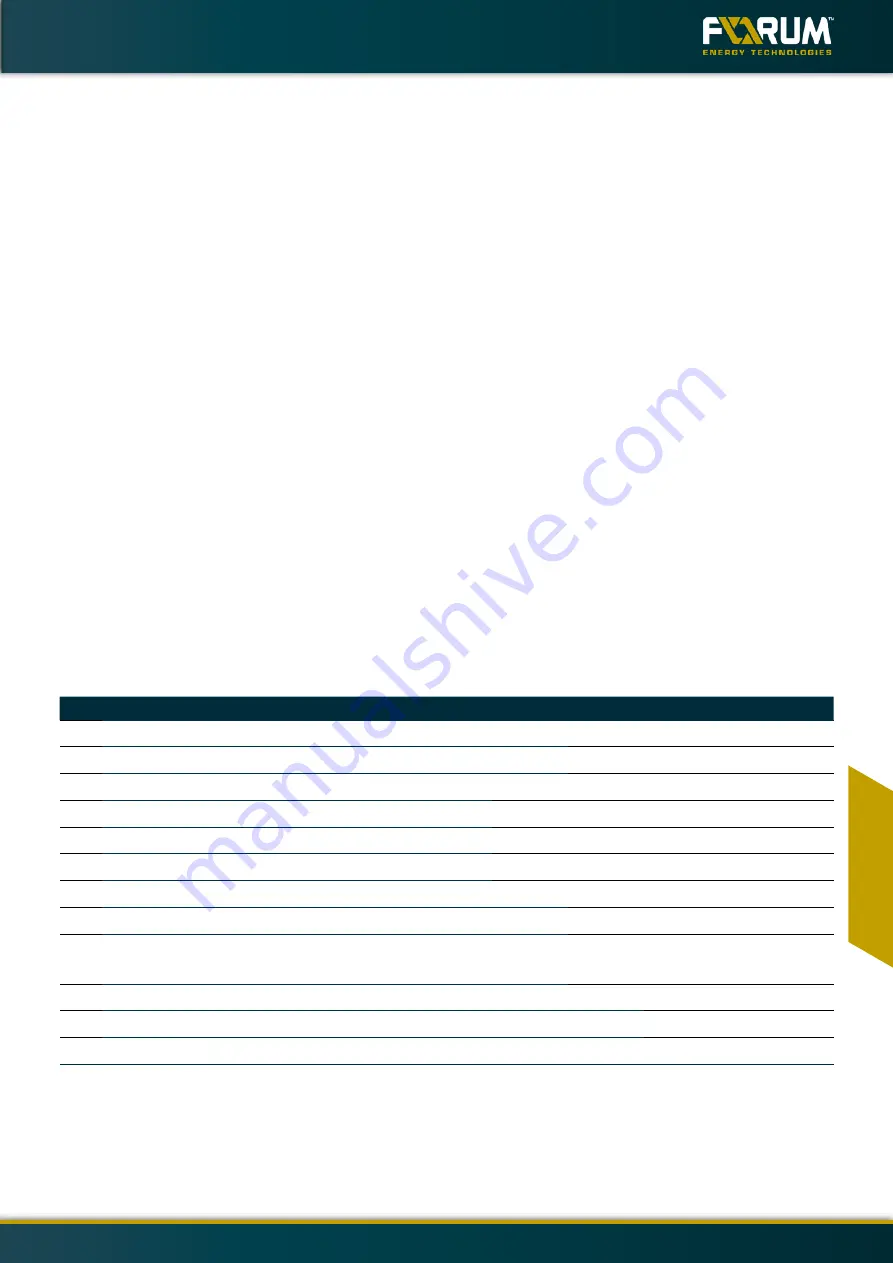
Operation Maintenance Manual
2018-05
PN 9GV73109-D - Revision: 02
Safety Spinning Wrench
75
IN
SP
EC
TI
O
N /
M
AI
N
TE
NAN
C
E
6.4
Inspection Categories
6.4.1
Inspection Category I
This category consists of observing the machine during
operation for signs of inadequate operation.
Scope/Prerequisites
- During operation, check the machine daily for visible
damage such as cracks, breaks, loose connecting
elements and obvious signs of wear.
Procedure:
- Visual check.
- Put all parts indicating such signs out of service and
check for proper function.
- Ensure that a person with appropriate technical
knowledge accomplishes this check.
6.4.2
Inspection Category II
Category II includes additional tests not included in
Category I inspections.
Scope/Prerequisites
- Check for signs of corrosion, deformation, lose or
missing parts, aging processes, proper lubrication,
externally visible cracks and adjustment work.
Procedure:
- Category II inspections may require removal of certain
parts to assess the wear limits according to the
specified tolerances.
6.4.3
Inspection Category III
Category III includes additional tests not included in
Category II inspections.
Scope/Prerequisites
- Before inspection remove all foreign material such
as dirt, paint, lubricants, oil, abrasion, etc. from the
affected parts. Use suitable methods such as stripping
off paint, steam cleaning, sand blasting, etc.
Procedure:
- A removal of certain parts to determine the wear limits
according to the specified tolerances (API) is necessary.
6.4.4
Inspection Category IV
In addition to the inspections in Category III, Category IV
includes a check and exchange op pneumatic pipes and
equipment.
Scope/Prerequisites
- Appropriately equipped workshop
- Inspect all parts for excessive wear, cracks, deformation
and other damage
- a removal of certain parts to determine the wear limits
according to the specified tolerances
Procedure:
- Ensure that all tests are performed according to the
manufacturer‘s specifications.
- Before inspection remove all foreign material such
as dirt, paint, lubricants, oil, abrasion, etc. from the
affected parts. Use suitable methods such as stripping
off paint, steam cleaning, sand blasting, etc.
6.4.5
Inspection intervals und Inspection tasks - SSW-40 Elevator
Pos. Task
Daily
Weekly Semiannually Annually
1
Function test and ongoing observation.
'
'
'
'
2
Functionality of Feedback.
'
'
'
'
3
Checks for cracks and loose fittings/hoses.
'
'
'
'
4
Checks for signs of deformations and leakages.
'
'
'
'
5
Check for signs of wear and corrosion.
'
'
'
'
6
Check for state of lubrication and conservation.
'
'
'
'
7
Check for no loose components and presence of all warning signs.
"
'
'
'
8
Check all possible settings (eg. valves) on the SSW-40.
"
'
'
'
9
Checking the condition of the overall structure (Elevator-Links, hydraulic
system) and the interaction of all components and possible attachments
with the SSW-40.
"
'
'
'
10
Checking wear limits (component measurement).
"
"
'
'
13
Exchange of selected hydraulic components.
"
"
"
'
14
Replacement of wear-intensive components (recommended spare parts).
"
"
"
'
'
Necessary
"
Unnecessary