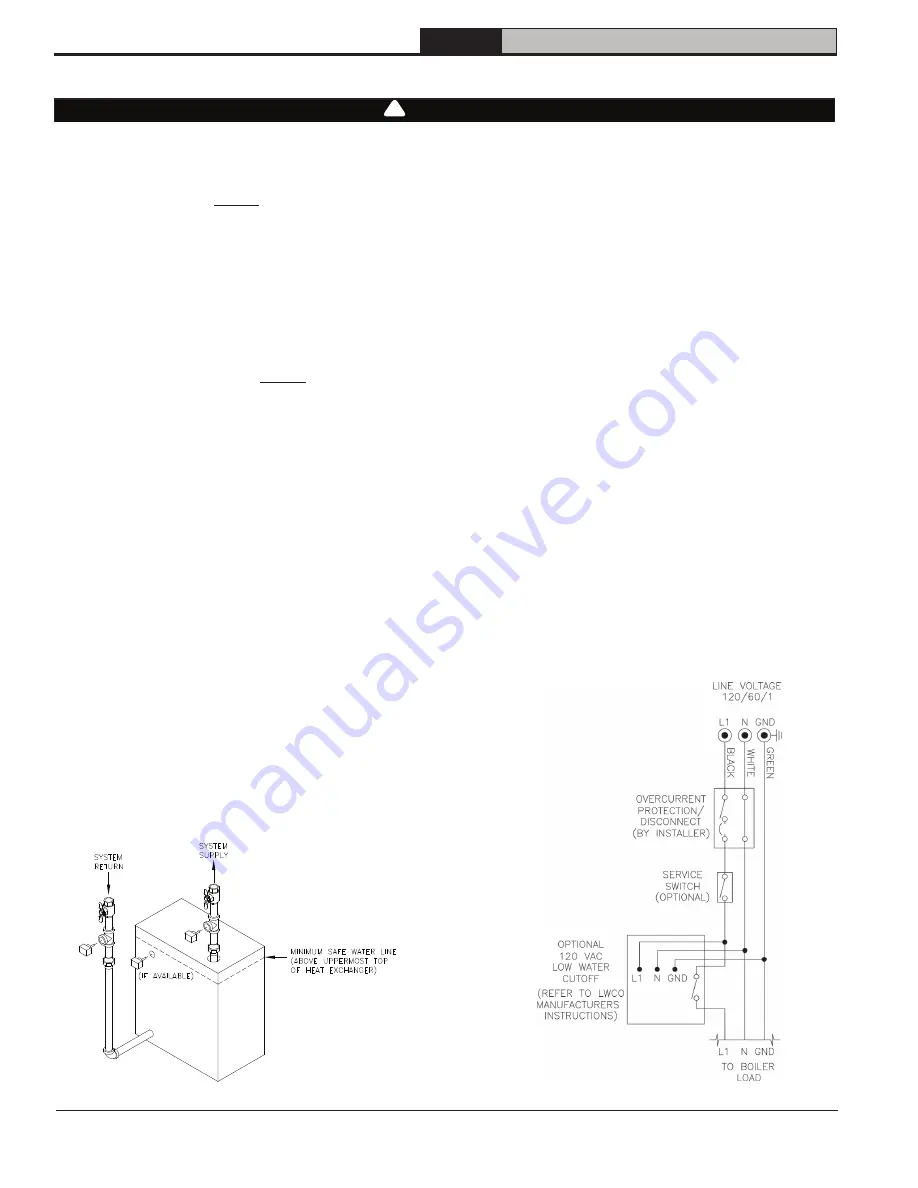
66
106346-06 - 8/19
FORCE
Installation, Operating & Service Manual
When
A low water cutoff is required to protect a hot
water boiler when any connected heat distributor
(radiation) is installed below the top of the hot
water boiler (i.e. baseboard on the same floor
level as the boiler). In addition, some jurisdictions
require the use of a LWCO with a hot water boiler.
Where
The universal location for a LWCO on both gas
and oil hot water boilers is above the boiler, in
either the supply or return piping. The minimum
safe water level of a water boiler is at the
uppermost top of the boiler; that is, it must be full
of water to operate safely.
It is recommended that the LWCO control
is installed above the boiler to provide the
highest level of protection. However, where
the LWCO control is approved by the LWCO
control manufacturer for installation in a high
boiler tapping of a water boiler, the use of the
listed LWCO control is permitted when it is
installed according to the LWCO manufacturer’s
instructions.
What Kind
Typically, in residential applications, a probe type
LWCO is used instead of a float type, due to their
relative costs and the simplicity of piping for a
probe LWCO.
How to Pipe
A “tee” is commonly used to connect the probe
LWCO to the supply or return piping, as shown
below.
LWCO Location
Wiring of Typical LWCO
Appendix A:
Aftermarket Low Water Cut Off (LWCO) On Hot Water Boilers
WARNING
•
DO NOT ATTEMPT to cut factory wires to install an aftermarket Low Water Cut Off (LWCO).
Only use connections specifically identified for Low Water Cut Off.
• In all cases, follow the Low Water Cut Off (LWCO) manufacturer's instructions.
!
Select the appropriate size tee using the LWCO
manufacturer’s instructions. Often, the branch
connection must have a
minimum
diameter
to prevent bridging between the probe and the
tee. Also, the run of the tee must have a minimum
diameter to prevent the end of the probe from
touching or being located too close to the inside
wall of the run of the tee.
Ideally, manual shutoff valves should be located
above the LWCO and the boiler to allow for
servicing. This will allow probe removal for
inspection without draining the heating system.
Many probe LWCO manufacturers recommend an
annual inspection of the probe.
How to Wire
LWCO’s are available in either 120 VAC or 24 VAC
configurations. The 120 VAC configuration can
be universally applied to both gas and oil boilers
by wiring it in the line voltage service to the boiler
(after the service switch, if so equipped).
The presence of water in a properly installed
LWCO will cause the normally open contact of the
LWCO to close, thus providing continuity of the
120 VAC service to the boiler.
It is recommended to supply power to the probe
LWCO with the same line voltage boiler service as
shown below.
Содержание FORCEOL115-E
Страница 56: ...56 106346 06 8 19 FORCE Installation Operating Service Manual Bare Boiler Assembly 15 Service Parts continued...
Страница 58: ...58 106346 06 8 19 FORCE Installation Operating Service Manual Jacket Assembly 15 Service Parts continued...
Страница 61: ...61 106346 06 8 19 FORCE Installation Operating Service Manual Beckett AFG Burner 15 Service Parts continued...
Страница 63: ...63 106346 06 8 19 FORCE Installation Operating Service Manual Beckett NX Burner 15 Service Parts continued...