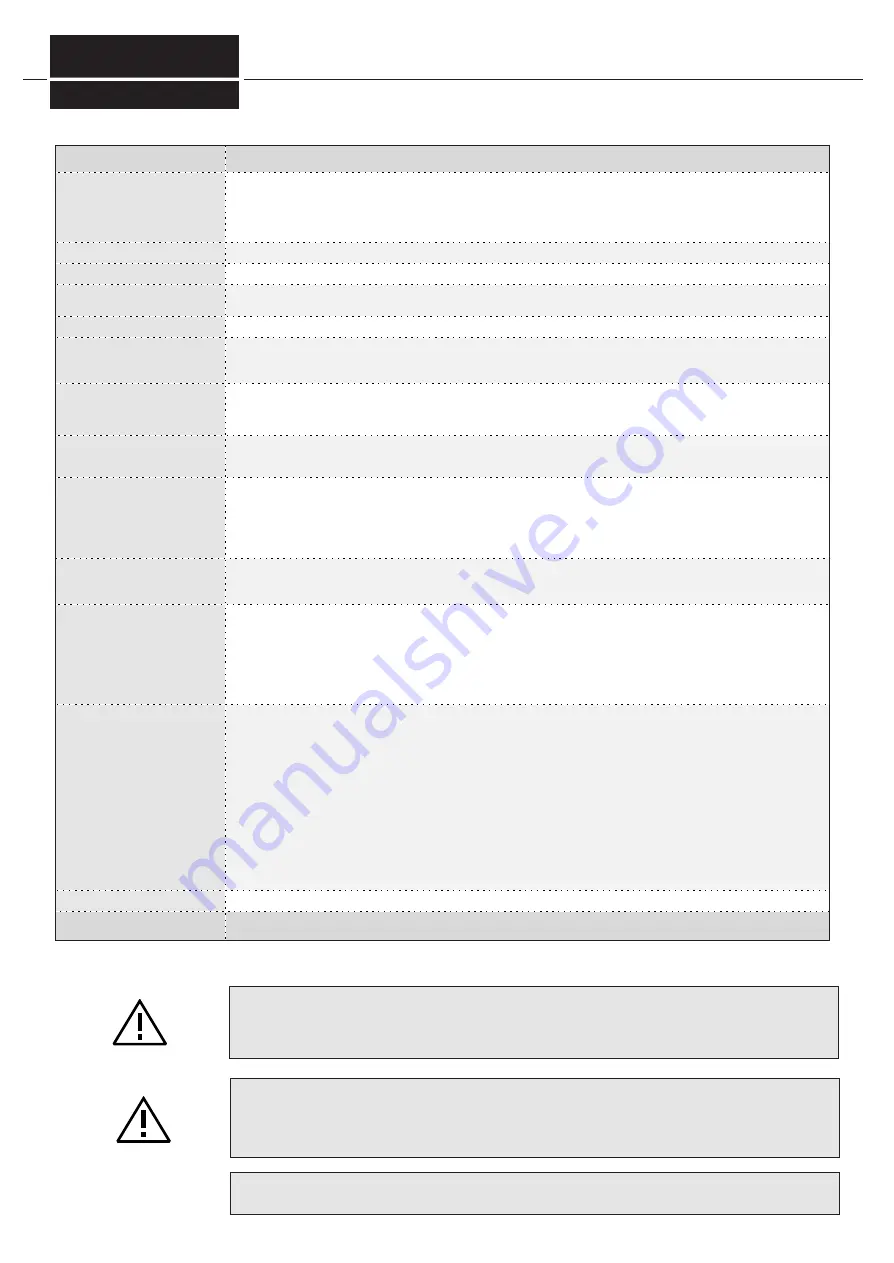
Electrical data
Safety Category
Performance Level
Safety Integrity Level
operation voltage
4 (EN ISO 13849-1:2008) and EN 61496 or IEC 61496 and prEN 12622
PL e (EN ISO 13849-1:2008), MTTFD > 300
SIL3 (EN 62061:2005), PFH = 2,38 x 10
-10
1/h
24 V DC, +/- 20 %, SELV
max. power cunsumption
protection from incorrect
connection
protection class
electrical connection
(no charge)
:
max. 0,5 A
Protection against all possibilities of errors is not provided.
III
transmitter: angular plug
receiver:
integrated plug-in connector with M 32 as strain relief
connecting cables
cable arrangement
outputs
inputs
transmitter: 3- core max. 1 mm
receiver:
10- bis 28-core (according to operating mode) max. 1 mm
Cables to be laid separately from high-voltage cables. The cable laying must be arranged in a way that no
mechanical damage of the cable is possible. For that reason the cable must be installed in a reinforced hose if
not protected by the machine.
OSSD 1 and 2: Fail-Safe PNP outputs , max. 0,5A, with short-cut and side-current monitoring
RXOK1 and 2: PNP-outputs with short-cut and side-current monitoring during switching on, max. 0,5 A
SGA , HUSP, SEU2K, KAST (KAST: only when using the external muting lamp): PNP-outputs max. 0,5A
TXD: RS 232 serial interface
FUO, FUS, SGO, SGS, SP, EDMO, EDMS, NA1, NA2, NA 3, NLW: 0 V / 24V DC +/- 20 %, 10 mA
KAST: : 0 V / 24V DC +/- 20 %, 25 mA
response times
time windows for the input
signals (basic tolerances)
Tolerance enhancement
environmental data
1,5 ms between the interruption of a light beam and the disabling of the OSSDs
10 ms between the release of the foot pedal orthe opening of a protective circuit and the disabling of the OSSDs
10 ms between the opering of a protective circuit and disabling of the release of the rear stoppers RXOK1 & -2
2,6 ms between the opeing of the overrun traverse cam switch and the disabling of the OSSDs during the over-
run traverse test
switch-over from stopped state into closing state after enabling of the OSSDs : 300 ms (only with operatiing mo-
de with contactor/valve control EDM).
switch-over into slow speed state when the start is carried out within the range of the safety point (at SP = 1):
100 ms after detection of the closing movement state by the EDM, i.e. 100 ms after enabling of the OSSDs
when the press is operating without the EDM.
switch-over into fast speed when the start of the press is outside the range of the safety point (at SP = 0): 100
ms after detection of the closing movement state by the EDM, i.e. 100 ms after enabling of the OSSDs when the
press is operating without the EDM.
switch-over into slow speed state when the start of the press with slow speed request (200 ms after SGA = 0
has been transmitted to NC): 70 ms after detection of the the closing movement state by the EDM, i.e. 70 ms
after enabling of the OSSDs when the press is operating without the EDM.
only with AKAS......F: max. 300 ms
Electrical connections - Description / Wiring diagrams
Electrical data
22
6
6.1
Doku Nr. 995 Stand 1.12.2011 / Aui
Caution!!!
Only if the accident preventing light barrier AKAS® has been installed according to the operating in-
structions and connected according to the wiring diagrams, and if all relevant national and international accident
prevention/safety regulations are observed , a safe operation is ensured !
Any modification of the specified circuits can cause hazardous states and is therefore forbidden.
Caution!!
The use of both AKAS® ...
without F
series and the AKAS®...
with F
series adjusted to "operation with
connection to an additional safety PLC" receiver is only permitted in combination with an additional safety PLC
(e.g.
FPSC
)
which provides the safe fast speed-/slow speed signals and closing request signals via cables with
short-cut and side-current monitoring and which provides a safe processing of the OSSD-Signals of the AKAS®.
If the press does not posssess any position-monitored contactors for the seitch-over from fast speed into slow speed,
a safe integration is possible using the Fiessler
AMS-System.
FIESSLER
E L E K T R O N I K