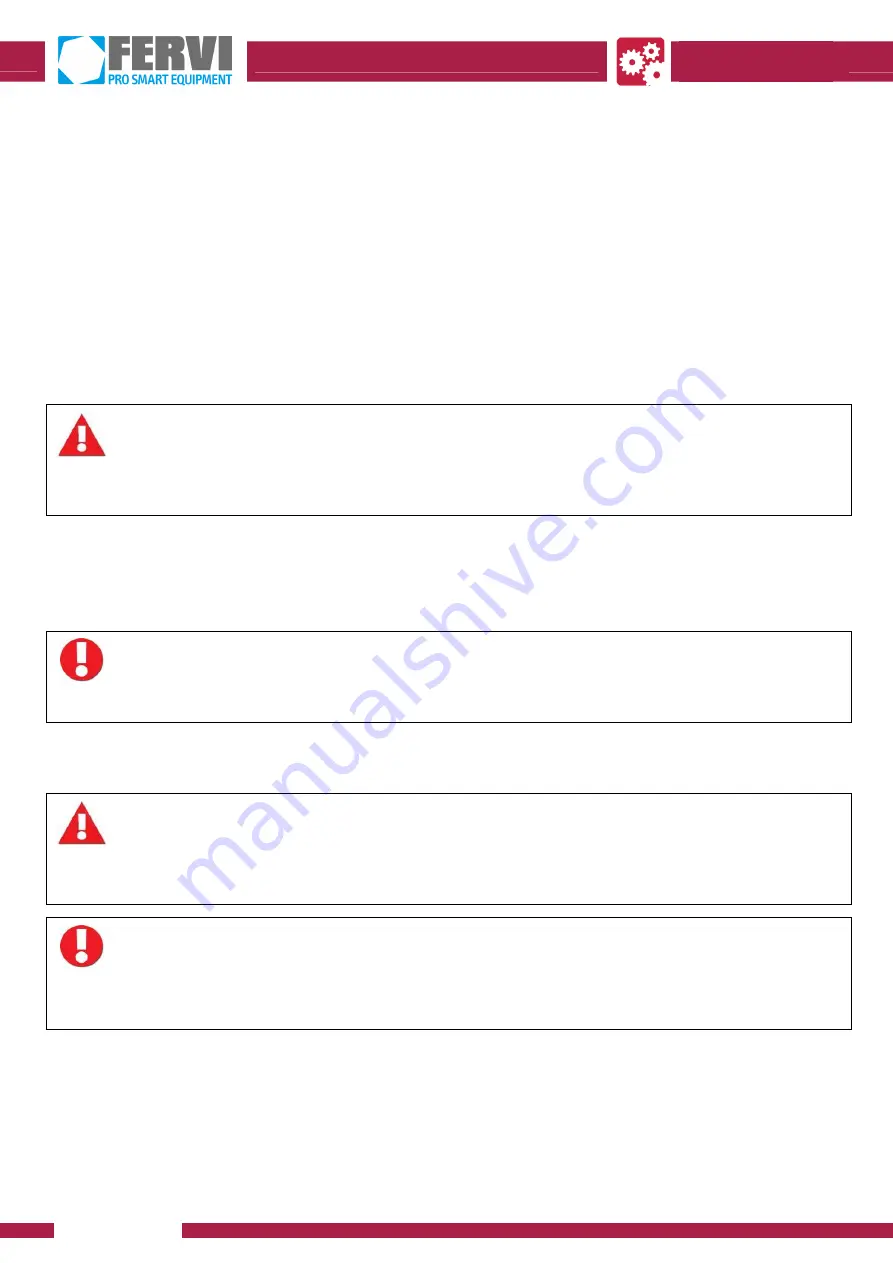
MACHINES AND
ACCESSORIES
Page 38 of 55
Al
lr
ig
ht
s
ar
e
re
se
rv
ed
of
re
pr
od
uc
tio
n
an
d
di
ss
em
in
at
io
n
of
th
is
Te
ch
ni
ca
lM
an
ua
la
nd
do
cu
m
en
ta
tio
n
ci
te
d
an
d/
or
at
ta
ch
ed
.I
ti
s
ex
pr
es
sl
y
fo
rb
id
de
n
to
re
pr
od
uc
e,
pu
bl
is
h
or
di
st
rib
ut
e
an
y
in
fo
rm
at
io
n
fr
om
th
is
M
an
ua
l.
Co
py
rig
ht
by
FE
RV
I
11 MAINTENANCE
Any maintenance, except for that specifically listed in this manual should be performed by
qualified staff authorized by the manufacturer.
This manual does not elaborate information on disassembly and maintenance, as these
operations should always be carried out exclusively by Technical Assistance staff.
11.1Routine maintenance
11.1.1
At the end of each machining
Electric shock
Before maintenance or checks, turn off the machine and ALWAYS unplug the plug from the
power outlet.
Regularly clean and take care of the machine to guarantee proper efficiency and a long
working life.
Use a compressor to blow off shavings, chips and sawdust accumulating inside the machine
and on work surfaces at the end of each machining operation
Working with compressed air
ALWAYS wear the protective goggles when using compressed air.
Check the state of the Planer and CE plate and warning plate at the same time; If they are no
longer legible ask for more.
Faults or defects
Disable the machine and affix a warning sign to forbid its use, until it works properly again
and it is safe to use.
Cleaning the machine
DO NOT use detergents or any solvents; the plastic parts are easily damaged by chemical
agents.
11.1.2
Periodically
Every 6 months
of the machine’s life, perform a thorough inspection of operation and wear.
Disconnect the plug from the mains and check the length and the efficiency of the electric
motor brushes. If necessary, replace them with identical ones.
fervi.com