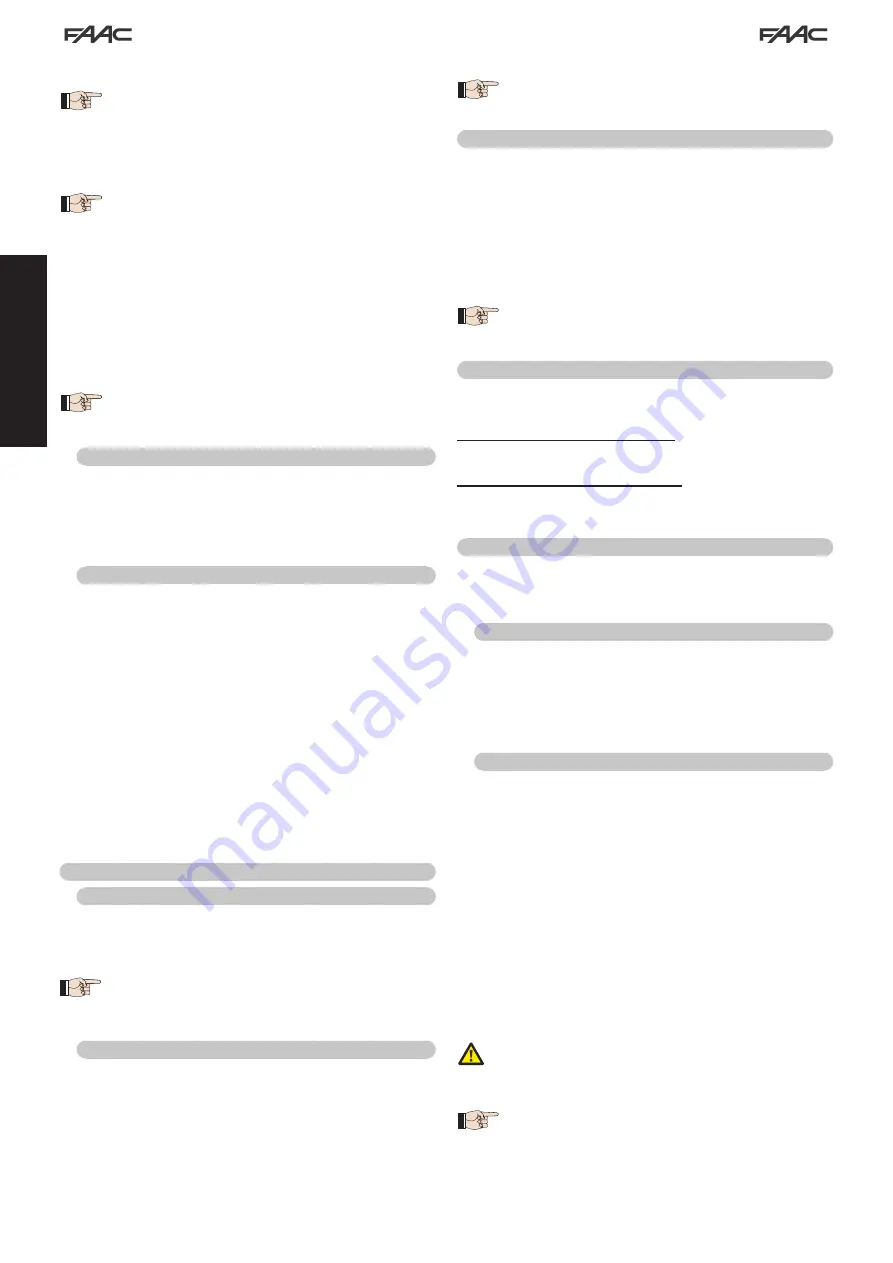
4
ENGLISH
•
Secure the piston without spring in the same hole shown above.
With the barrier open, the spring must NOT be
compressed.
•
Install the beam and its fixing pocket using the provided screws,
as shown in Fig. 17, ref. from
a
to
h
(the rubber profile of the
beam must face the closing direction)
Do not grease the fixing screw of the bar.
•
If the application requires a segmented bar, once the first
segment and fixing pocket have been assembled, close
the automatic system, lock it and follow the instructions for
additional segment assembly, as shown in Fig. 20, ref. from
a
to
d
•
Adjust the opening and closing mechanical stops as shown in
Fig. 15, and tighten the lock nut.
•
Ensure that the beam is balanced following the instructions
contained in paragraphs 4.5 and 4.6.
The compartment should be fixed, as shown in the
sequence in Fig. 21, when all mechanical installations,
wiring and start-up have been completed.
4.5 Fixing the plunging pistons
Barrier balancing is obtained by correctly adjusting the spring preload
ring nut (see next paragraph) but also by setting the two plunging
pistons in the most suitable position. This position is determined by
the length of the beam and the presence of any accessories that
may be applied to it (see paragraph 11).
4.6 Balancing the barrier
WARNING: This procedure must be carried out as the barrier is
not internally balanced. The beam is balanced when, operating
manually (ref. paragraph 6) the beam remains stationary in the
45° position.
To balance the barrier, proceed as follows:
•
Install the bar and all related accessories on the barrier structure,
as required by the final configuration of the system.
•
Ensure that the operator is released: see paragraph 6.
•
Ensure that the plunging pistons are secured on the rocker arm
according to the instructions in paragraph 11 in Table 2 or Table
3, depending on the installed beam model (S or L, respectively)
•
Manually move the bar to the 45° position and verify it remains
stationary. If the bar tends to open, turn the spring preload ring
nut anti-clockwise (Fig. 16 ref.
a
); if it tends to close, turn the ring
•
nut clockwise (Fig. 16 ref.
b
).
5. START-UP
5.1 Connecting the control equipment
WARNING: Before carrying out any work on the control board
(connections, maintenance, etc.) always cut off the electrical
power.
For all automatic system connections and testing, refer
to the section dedicated to the electronic equipment,
paragraph 1 on page 6 and following.
5.2 Testing the automated system
Once installation has been completed, apply the "danger" sign sticker
(ref. Fig. 29) to the top of the upright profile. Proceed to ensure correct
operation of the automated system and all the accessories
connected to it.
Give the Customer the “User’s Manual”, the
documentation required by current law and show how
to correctly operate the barrier, pointing out the areas
of potential danger.
6. MANUAL OPERATION
Should manual operation of the barrier be required due to electrical
power cut-offs or automated system inefficiency, use the release
device with the provided key.
The provided unlocking key is either triangular (Fig. 1
8
ref.
a
) or
customised (Fig. 1
8
ref.
b
optional).
•
Insert the unlocking key in the lock and turn the key
anticlockwise
until it clicks into place, as shown in Fig. 1
8
•
Open or close the beam manually.
With the bar released, the motor may start for
approximately 3 seconds. This is normal and determined
by the parameter Hold Close / Hold Open
7. RESTORING NORMAL OPERATION
To avoid an accidental pulse opening the barrier during this operation,
before activating the locking system, cut off all power to the system.
triangular unlocking key (standard):
- turn the key
clockwise
until it stops and then remove it (Fig. 18
ref.
a
).
customised unlocking key (optional):
- turn the key
clockwise
until it stops and then remove it(Fig. 18 ref.
b
).
8. MAINTENANCE
When performing six-month maintenance, always check the correct
balancing of the system and the correct operation of the safety
devices.
8.1 Topping up the oil
Check the amount of oil in the tank every 6 months.
The level must be included between the two notches on the inspection
rod.
To top up, unscrew the filler cap (Fig. 12 ref.
a
) and pour oil up to
the indicated level.
Use only FAAC HP OIL.
8.2 Air bleeding
FAAC products are delivered already bled of any air in the hydraulic
circuit. Maintenance operations, replacing spare parts (e.g.
connection pipes) or careless transport can cause entry of air in the
hydraulic circuit, which in turn can cause operator irregular movement
or reduce its torque. Should beam movement be irregular, release
the air from the hydraulic system following the instructions below:
•
Electrically operate the beam:
•
When opening is completed, slightly loosen and tighten the
bleeder screw of the piston with the balance spring (Fig. 5
ref.
d
).
•
When closing is completed, slightly loosen and tighten the
bleeder screw of the piston without the balance spring (Fig. 5
ref.
l
).
If necessary, repeat the operation until regular movement of the
beam is obtained.
Care needs to be taken at this stage as the pistons
contain oil under pressure which could leak out if the
screws are loosened too much.
If the parameters
FO
and
FC
in Advanced
Configuration have been changed and set to a value
lower than default, during bleeding we recommend
setting them to an equal or greater value, to facilitate
air bleeding
Содержание B680H
Страница 1: ...B680H ...
Страница 2: ......
Страница 4: ......
Страница 150: ...26 a b DX SX a b c Fig 10 Fig 11 M M L1 L2 L3 L1 L2 L3 Fig 12 d Fig 13 Fig 14 Fig 15 a b Fig 16 ...
Страница 151: ...27 a b c d e f g h Fig 17 L ...
Страница 152: ...28 Fig 18 a b a b d Fig 19 c 1 2 Fig 20 ...
Страница 153: ...29 a b Fig 21 d e f c ...
Страница 156: ...32 Fig 31 a b c d e ...
Страница 157: ...33 Fig 32 f g ...
Страница 158: ......
Страница 163: ...5 1 2 Fig 18 ...
Страница 164: ......
Страница 165: ......