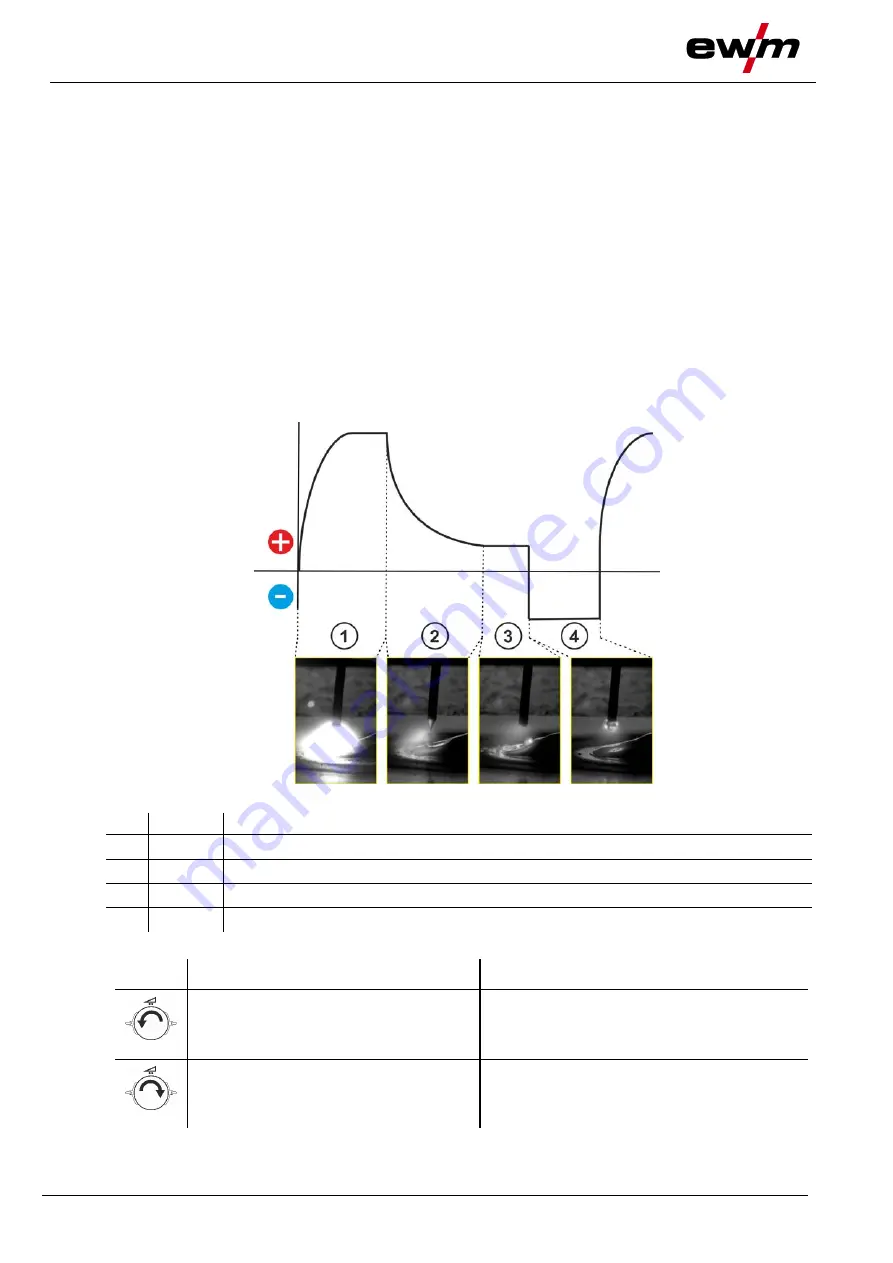
Welding procedure
MIG/MAG welding
48
099-00L104-EW501
17.01.2022
6.1.6 acArc puls XQ
The alternating current welding process acArc puls XQ makes MIG aluminium welding even easier in ma-
nual and automated modes. Clean weld seams with no traces of powder on the thinnest metal sheets,
even with AlMg alloys, are possible with acArc puls XQ.
Advantages
• Perfect aluminium welding, especially in thin sheet metal due to directed heat reduction
• Excellent gap bridging, also facilitates automated applications
• Minimised heat input - reduces the risk of burn-through
• Less welding fume emissions
• Clean weld seams due to greatly reduced magnesium burn-off
• Easy and safe handling of the arc for manual and automated welding
A constant change of polarity (see following figure) takes place during the process.
The heat input from the material shifts to the welding consumable and the drop size increases significa-
ntly (compared to the direct current welding process). This ensures excellent bridging of air gaps and re-
duced welding fume emissions.
Figure 6-10
Item Symbol Description
0
1
Droplet formation in the pulse phase
2
Droplet detachment after the pulse phase
3
Fundamental current phase
4
Cleaning and preheating the wire in the negative phase
With the rotary knob “arc dynamics”, the negative phase in the process can be influenced.
Setting of the dynamics
Welding properties
Left turn (more minus), negative phase
gets longer
• ---------- More power on the wire
• ---------- Droplet volume increases
• ---------- Process becomes cooler
Right turn (more plus), negative phase
gets shorter
• ---------- More power on the workpiece
• ---------- Droplet volume decreases
• ---------- Process becomes hotter