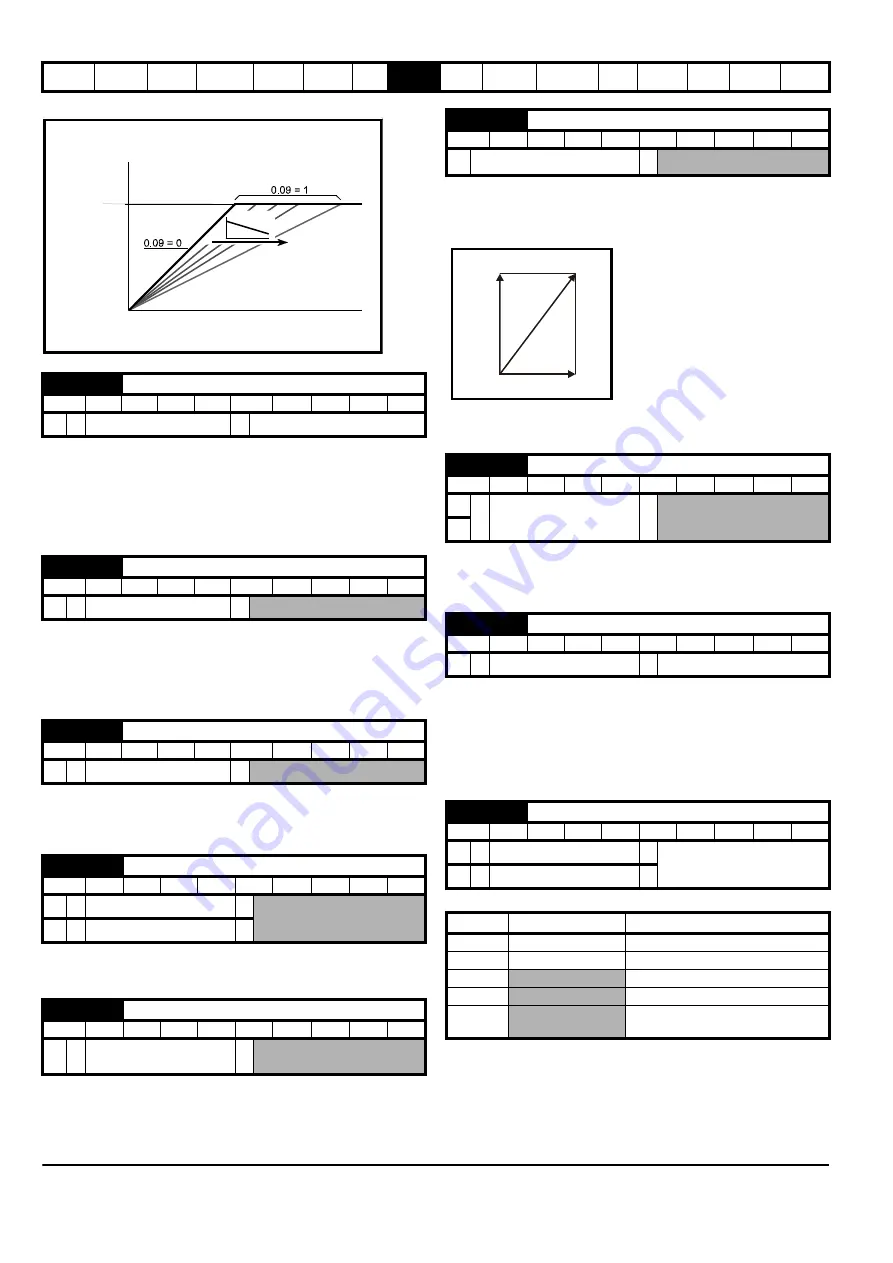
Safety
Information
Introduction
Product
Information
System
configuration
Mechanical
Installation
Electrical
Installation
Getting
Started
Basic
parameters
Running
the motor
Optimization
SMARTCARD
operation
Onboard
PLC
Advanced
parameters
Technical
Data
Diagnostics
UL Listing
Information
116
Unidrive SPM User Guide
www.controltechniques.com Issue Number: 3
Figure 8-2 Fixed and variable V/f characteristics
Closed-loop
Pr
0.09
(
3.12
) operates in the feedback path of the speed-control loop in
the drive. See Figure 13-4 on page 174 for a schematic of the speed
controller. For information on setting up the speed controller gains, refer
to Chapter 10
Optimization
on page 136.
8.2.5 Monitoring
Open-loop
Pr
0.10
(
5.04
) indicates the value of motor speed that is estimated from
the following:
0.12
Post-ramp frequency reference
0.42
Motor - no. of poles
Closed-loop
Pr
0.10
(
3.02
) indicates the value of motor speed that is obtained from
the speed feedback.
Open-loop & closed loop vector
Pr
0.11
displays the frequency at the drive output.
Servo
Pr
0.11
displays the position of the encoder in mechanical values of 0 to
65,535. There are 65,536 units to one mechanical revolution.
Pr
0.12
displays the rms value of the output current of the drive in each
of the three phases. The phase currents consist of an active component
and a reactive component, which can form a resultant current vector as
shown in the following diagram.
The active current is the torque producing current and the reactive
current is the magnetising or flux-producing current.
Open-loop & closed loop vector
When the motor is being driven below its rated speed, the torque is
proportional to [
0.13
].
Servo
Pr
0.13
can be used to trim out any offset in the user signal to analog
input 1.
8.2.6 Jog reference, Ramp mode selector, Stop and
torque mode selectors
Pr
0.14
is used to select the required control mode of the drive as follows:
0.09 {3.12}
Speed controller differential feedback gain
RW
Uni
US
CL
Ú
0.00000 to 0.65535(s)
Ö
0.00000
0.10 {5.04}
Estimated motor speed
RO
Bit
FI
NC
PT
OL
Ú
±180,000 rpm
Ö
0.10 {3.02}
Motor speed
RO
Bi
FI
NC
PT
VT
Ú
±Speed_max rpm
Ö
0.11 {5.01}
Drive output frequency
RO
Bi
FI
NC
PT
OL
Ú
±SPEED_FREQ_MAX Hz
Ö
VT
Ú
±1250.0 Hz
Ö
0.11 {3.29}
Drive encoder position
RO
Uni
FI
NC
PT
SV
Ú
0 to 65,535
1/2
16
ths of a revolution
Ö
Motor
voltage
Frequency
AC supply
voltage
I
MOTOR
0.12 {4.01}
Total motor current
RO
Uni
FI
NC
PT
Ú
0 to Drive_current_max A
Ö
0.13 {4.02}
Motor active current
RO
Bi
FI
NC
PT
OL
Ú
±Drive_current_max A
Ö
VT
0.13 {7.07}
Analog input 1 offset trim
RW
Bi
US
SV
Ú
±10.000 %
Ö
0.000
0.14 {4.11}
Torque mode selector
RW
Uni
US
OL
Ú
0 to 1
Ö
Speed control (0)
CL
Ú
0 to 4
Ö
Setting
Open-Loop
Closed-Loop
0
Frequency control
Speed control
1
Torque control
Torque control
2
Torque control with speed override
3
Coiler/uncoiler mode
4
Speed control with torque feed-
forward
Active
current
Total current
Magnetising current