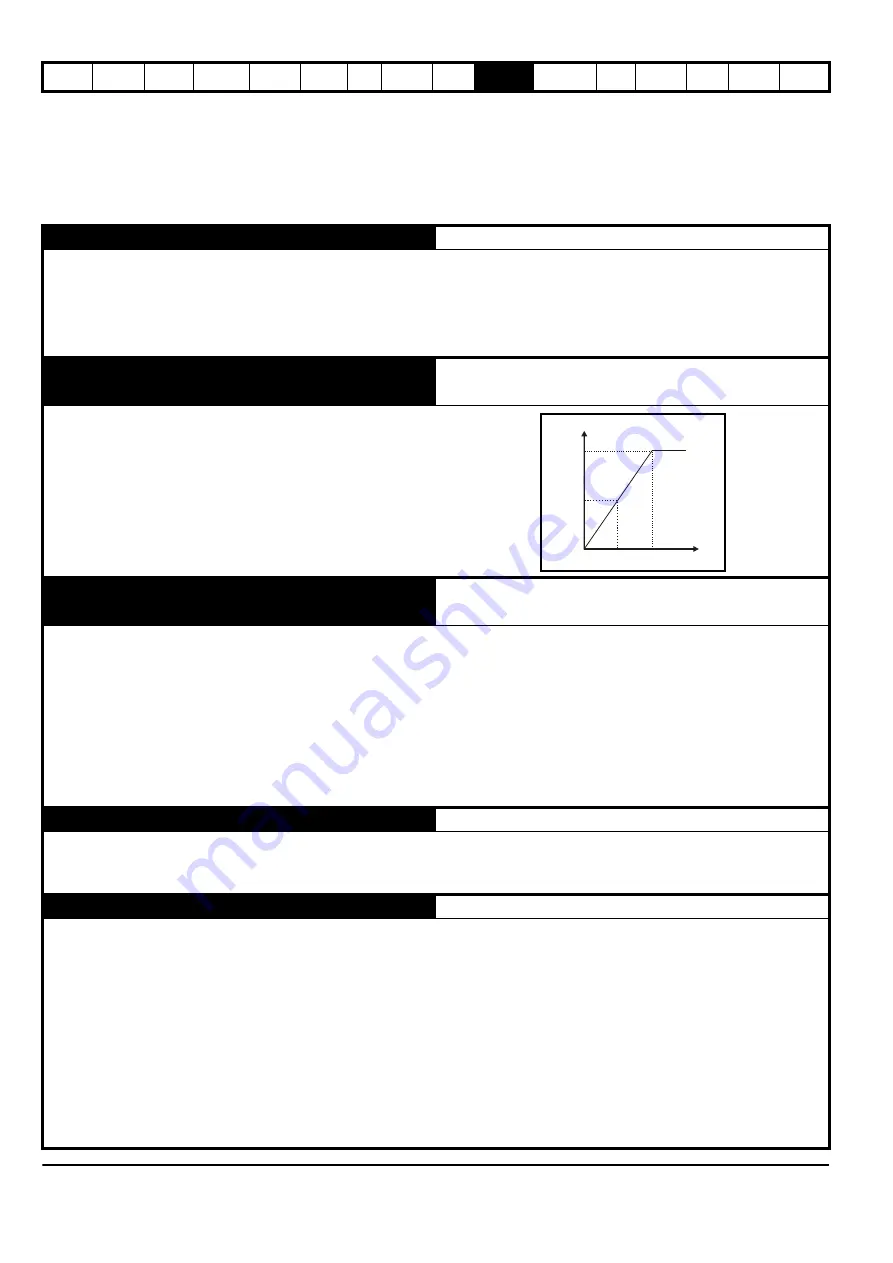
Safety
Information
Introduction
Product
Information
System
configuration
Mechanical
Installation
Electrical
Installation
Getting
Started
Basic
parameters
Running
the motor
Optimization
SMARTCARD
operation
Onboard
PLC
Advanced
parameters
Technical
Data
Diagnostics
UL Listing
Information
136
Unidrive SPM User Guide
www.controltechniques.com Issue Number: 3
10 Optimization
This chapter takes the user through methods of optimizing the product
set-up, maximizing performance. The auto-tuning features of the drive
simplify this task.
10.1 Motor map parameters
10.1.1 Open loop motor control
Pr 0.46 {5.07} Motor rated current
Defines the maximum continuous motor current
The motor rated current parameter must be set to the maximum continuous current of the motor. (See section 10.2
Maximum motor rated current
on
page 146, for information about setting this parameter higher then the maximum Heavy Duty current rating.) The motor rated current is used in the following:
•
Current limits (see section 10.3
Current limits
on page 146, for more information)
•
Motor thermal overload protection (see section 10.4
Motor thermal protection
on page 146, for more information)
•
Vector mode voltage control (see Voltage mode Pr
0.07
, later in this table)
•
Slip compensation (see Slip compensation Pr
5.27
, later in this table)
•
Dynamic V/F control
Pr 0.44 {5.09} Motor rated voltage
Defines the voltage applied to the motor at rated frequency
Pr 0.47 {5.06} Motor rated frequency
Defines the frequency at which rated voltage is applied
The motor rated voltage Pr
0.44
and the motor rated frequency Pr
0.47
are used to define the voltage to frequency characteristic applied to the
motor (see voltage mode Pr
0.07
, later in this table). The motor rated
frequency is also used in conjunction with the motor rated speed to
calculate the rated slip for slip compensation (see motor rated speed Pr
0.45
, later in this table).
Pr 0.45 {5.08} Motor rated speed
Defines the full load rated speed of the motor
Pr 0.42 {5.11} Motor number of poles
Defines the number of motor poles
The motor rated speed and the number of poles are used with the motor rated frequency to calculate the rated slip of induction machines in Hz.
Rated slip (Hz) = Motor rated frequency - (Number of pole pairs x [Motor rated speed / 60]) =
If Pr
0.45
is set to 0 or to synchronous speed, slip compensation is disabled. If slip compensation is required this parameter should be set to the
nameplate value, which should give the correct rpm for a hot machine. Sometimes it will be necessary to adjust this when the drive is commissioned
because the nameplate value may be inaccurate. Slip compensation will operate correctly both below base speed and within the field-weakening
region. Slip compensation is normally used to correct for the motor speed to prevent speed variation with load. The rated load rpm can be set higher
than synchronous speed to deliberately introduce speed droop. This can be useful to aid load sharing with mechanically coupled motors.
Pr
0.42
is also used in the calculation of the motor speed display by the drive for a given output frequency. When Pr
0.42
is set to ‘Auto’, the number
of motor poles is automatically calculated from the rated frequency Pr
0.47
, and the motor rated speed Pr
0.45
.
Number of poles = 120 x (Motor rated frequency Pr
0.47
/ Motor rated speed Pr
0.45
) rounded to the nearest even number
Pr 0.43 {5.10} Motor rated power factor
Defines the angle between the motor voltage and current
The power factor is the true power factor of the motor, i.e. the angle between the motor voltage and current. The power factor is used in conjunction
with the motor rated current Pr
0.46
, to calculate the rated active current and magnetising current of the motor. The rated active current is used
extensively to control the drive, and the magnetising current is used in vector mode stator resistance compensation. It is important that this
parameter is set up correctly. The drive can measure the motor rated power factor by performing a rotating autotune (see Autotune Pr
0.40
, below).
Pr 0.40 {5.12} Autotune
There are two autotune tests available in open loop mode, a stationary and a rotating test. A rotating autotune should be used whenever possible so
the measured value of power factor of the motor is used by the drive.
•
A stationary autotune can be used when the motor is loaded and it is not possible to remove the load from the motor shaft. The stationary test
measures the stator resistance (Pr
5.17
) and voltage offset (Pr
5.23
), which are required for good performance in vector control modes (see
Voltage mode Pr
0.07
, later in this table). The stationary autotune does not measure the power factor of the motor so the value on the motor
nameplate must be entered into Pr
0.43
. To perform a Stationary autotune, set Pr
0.40
to 1, and provide the drive with both an enable signal (on
terminal 31) and a run signal (on terminal 26 or 27).
•
A rotating autotune should only be used if the motor is unloaded. A rotating autotune first performs a stationary autotune, as above, before rotating the
motor at
2
/
3
base speed in the direction selected for several seconds (regardless of the speed reference). In addition to the stator resistance (Pr
5.17
)
and voltage offset (Pr
5.23
), the rotating autotune measures the power factor of the motor and updates Pr
0.43
with the correct value. To perform a
Rotating autotune, set Pr
0.40
to 2, and provide the drive with both an enable signal (on terminal 31) and a run signal (on terminal 26 or 27).
Following the completion of an autotune test the drive will go into the inhibit state. The drive must be placed into a controlled disable condition
before the drive can be made to run at the required reference. The drive can be put in to a controlled disable condition by removing the SAFE
TORQUE OFF (SECURE DISABLE) signal from terminal 31, setting the drive enable parameter Pr
6.15
to OFF (0) or disabling the drive via the
control word (Pr
6.42
& Pr
6.43
).
Output
voltage
Pr
/ 2
0.44
Pr
0.44
Pr
/
2
0.47
Pr
0.47
Output
frequency
Output voltage characteristic
0.47
0.42
2
-----------
0.45
60
-----------
×
⎝
⎠
⎛
⎞
–