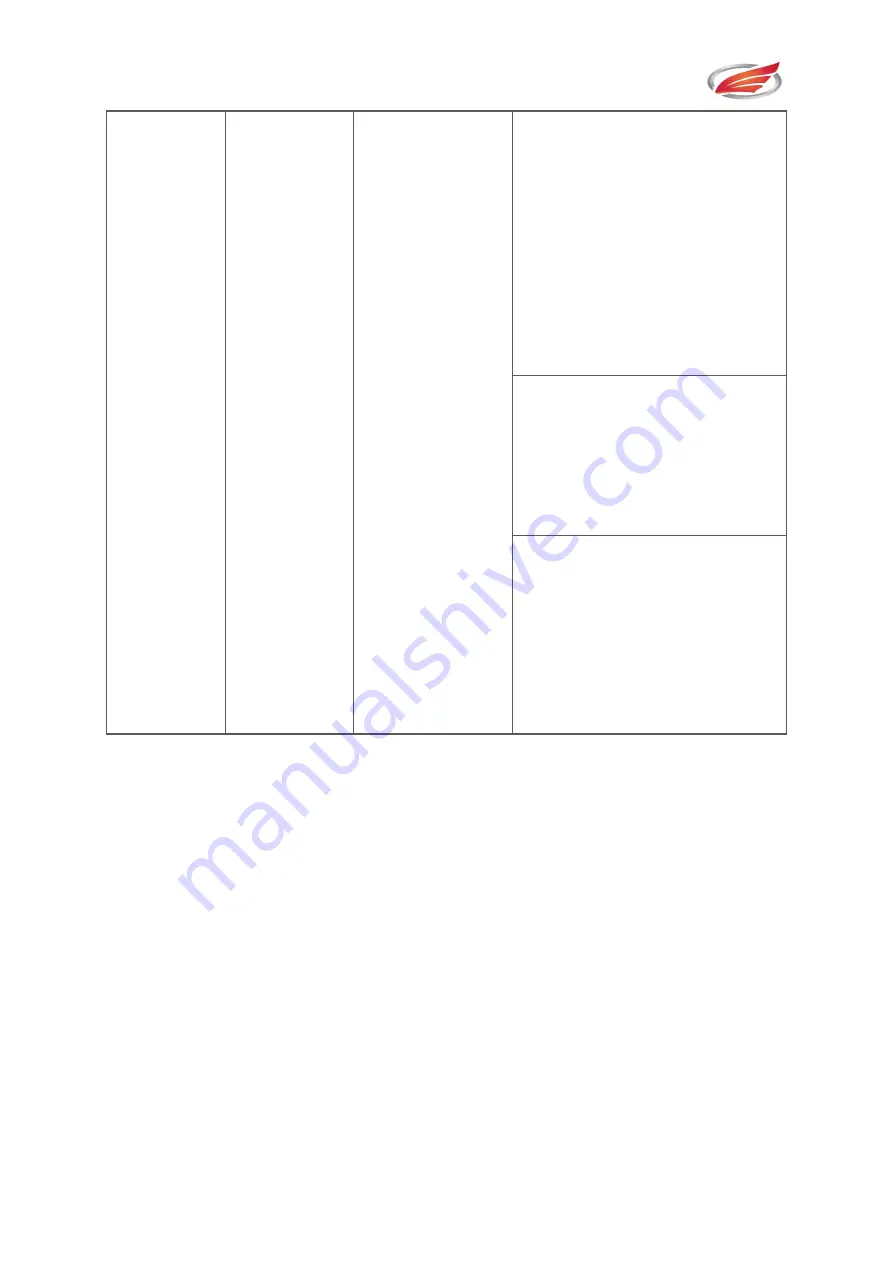
Appendix
EFORT INTELLIGENT EQUIPMENT CO.,LTD
294
11. Update the content of 5.2.
5 Safety Restriction
;
12. Update the content of 5.4.
1 TCPIP
;
13. Add the function of 5.4.3
EtherCAT Settings
14. Add the function 5.4.4 Et
hernetIP Settings
;
Chapter Six Motioning Tab In
terface
1. Update the default position
button to home position but
ton
Chapter Seven Monitoring Tab
Interface
1. Update the content of 7.2 I
O Monitoring
2. Add the function of 7.3 O
n-site monitoring of bus data