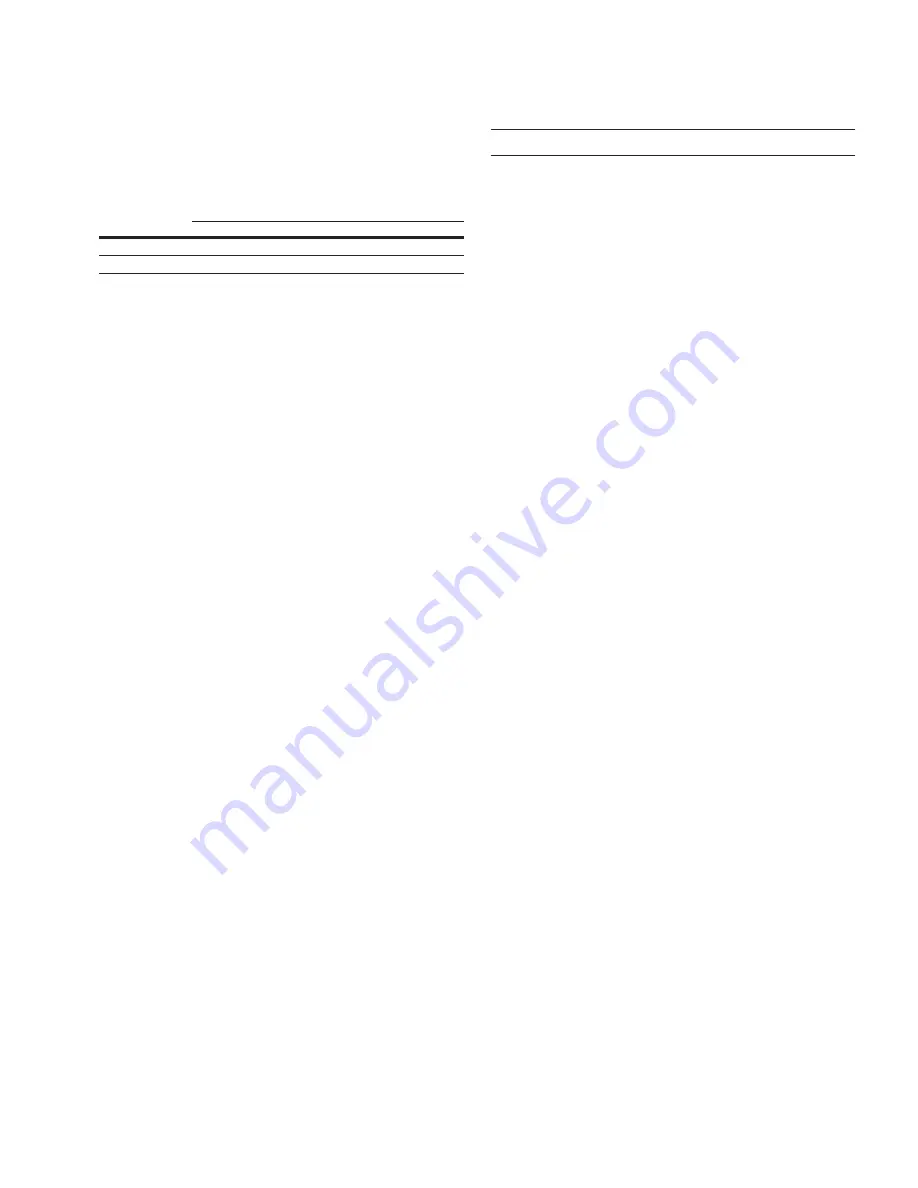
3
Installation and electrical connections
DPCT IOM InsTruCTIOn OPeraTIOn Manual
MN124018EN January 2023 www.eaton.com
Refer to Table 1 below for the recommended torque values
for the respective screw terminal blocks in the controller.
Table 1.
Terminal Block Torque Values
Terminal Block
Designation
Torque
n·m
In-lbs
P13, P15, P17
0.5
4.4
P14, P16
1.2
10.6
2.3.2 Electrical Checkout Instructions
Adjust the pressure set points detailed in Appendix E.
With the controller isolated and the ‘Start Pressure’
and ‘Stop Pressure’ values programmed, energize the
controller. If the system water pressure is lower than
the start pressure, the controller will start the pump.
If the controller is set up for fully automatic operation,
the controller will stop the pump when the pressure is
above the stop point and the minimum run timer (MRT)
has completed its timed interval. The system pressure
must be equal to or greater than the programmed stop
pressure value, otherwise the pump will stop only when
the pushbutton is pushed or if the MANUAL/OFF/AUTO
switch is placed in the OFF position. If the controller is
not setup for automatic shutdown operation (programmed
for manual stop mode), the stop pushbutton must be
operated to stop the pump, or the MANUAL/OFF/AUTO
switch is placed in the OFF position.
If required, the minimum run time (MRT) must be set for
a minimum of thirty (30) minutes. Refer to Appendix F for
programming of the MRT.
If the sequential start timer (SST) is required refer to
Appendix F. If not required set the SST to disabled. If
required, the lead pump SST should be set to disabled and
the lag SST to five (5) to ten (10) seconds. If there are more
than two pumps in the system, allow a ten (10) second
delay between pumps.
If the Undervoltage/Overvoltage alarms are present, check
the programmed values by referring to Appendix H. If the
values are programmed to their maximum and the alarms
continue to occur, check the main voltage supply to ensure
that the power available is dependable as per NFPA,
Pamphlet 20 standards.
2.4 System pressure connection
The DPCT is supplied with a Pressure Sensor, or as an
option, a Pressure Switch.
The “TEST” drain connection, located to the left of the
system pressure connection, should be piped to a drain or
to waste.
NOTE
Water supply lines to the drain valve and pressure sensor or
pressure switch must be free from dirt and contamination.
The controller interfaces with either a pressure sensor
or inputs from a remote device. The controller will come
pre-programmed for the correct model and the correct
pressure device.
On controllers that use the pressure sensor option the
sensor will be used to measure the system pressure. The
measured current system pressure value will be displayed
on the touch screen user interface at the “Home” screen
to the right-center of the display. Precise START and STOP
pressure set points can be programmed into the controller
via the touch screen user interface (Refer to section 5.6).
Pressure readings are also captured and recorded in the
memory of the controller during alarm conditions and
pressure deviations.
On foam additive controllers that use a remote device input
the touch screen user interface will display “OK” if the
pressure is within the setting of the remote device setting.
If the pressure falls below the remote device’s setting the
switch’s contacts will change state and the touch screen
user interface will display a “LOW” warning. The message
history will record “Low Pressure” when the pressure drops
below the set point.