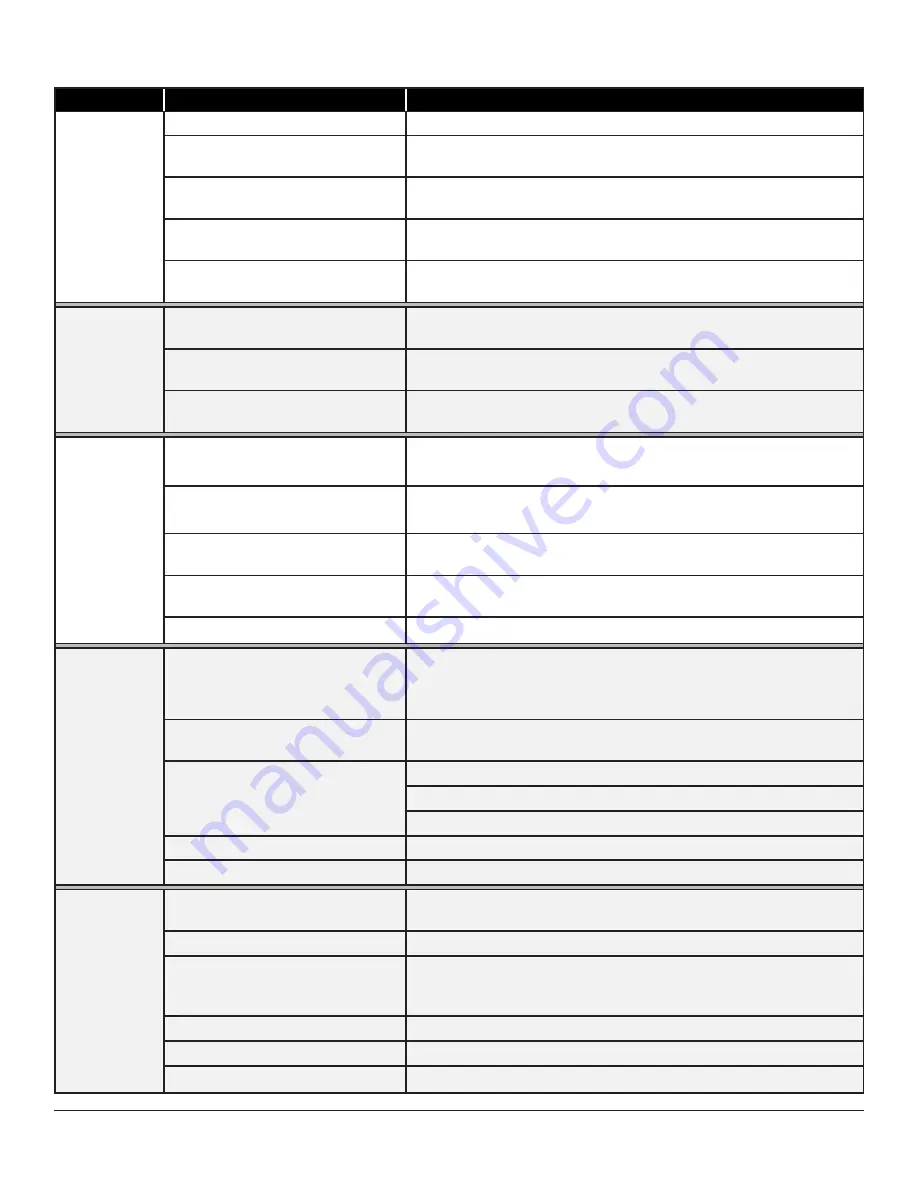
To order parts and supplies: 800.343.9353 >> eastwood.com
33
MIG WELDING TROUBLESHOOTING
PROBLEM
CAUSE
CORRECTION
Wire Will
Not Feed
Mode Not Set to MIG
Press the Mode Selection Button until it cycles to MIG mode.
Welder is in Spool Gun Mode
Take Welder out of Spool Gun mode.
See
MIG MODE USER INTERFACE OPERATION
for further details.
Drive Motor Wire Tension is Insufficient,
Allowing Wire Slippage
Tighten Drive Roller Tensioner.
Duty Cycle Exceeded
Allow the Welder to cool for a minimum of 15 minutes before attempting to
use again.
Welder is in not in Spool Gun Mode When
Attempting to Utilize a Spool Gun
Put the Welder into Spool Gun mode.
See
MIG MODE USER INTERFACE OPERATION
for further details.
Wire Burning
Back to
Contact Tip
Drive Motor Wire Tension is Insufficient,
Allowing Wire Slippage
Tighten Drive Roller Tensioner.
Wire Speed Setting May not be Adequate
for Welding Voltage Setting.
Decrease voltage setting.
Wire Stick Out from End of Contact Tip
Too Short
Cut wire stick out to 1/4” for welding with the MIG Gun or 3/4” if welding with
a Spool Gun.
Welder Will Not
Produce an Arc
Ground Cable not Attached to Metal Being
Welded
Attach Ground Clamp to metal being welded.
Ground Clamp Attached to a Contami-
nated or Rusty Work Piece
Prepare a thoroughly cleaned spot for the Ground Clamp.
Ground Cable Connector not Fully Secured
to Welder Terminal
Check Ground Clamp connection at Welder for tight connection.
Wrong Ground Clamp from Another
Device is Attached to Work Piece
Check that the correct welding ground from Welder being used is attached to
the work piece.
MIG Gun Contact Tip is Excessively Worn Replace MIG Gun Contact Tip.
Intermittent
Welding Arc
Incorrect Input Voltage
Check power supply. The Elite AC/DC MP200i requires a properly grounded,
240 Volt AC, 50 Amp power supply or a properly grounded 120 Volt AC,
20 Amp power supply.
Wrong Size Drive Roller Groove
Check Drive Roller size and install Drive Roller as required to match wire size
being run. See
DRIVE ROLLER under MIG WELDING SET-UP
for more details.
Poor Ground
Prepare a thoroughly cleaned spot for the Ground Clamp.
Check condition of Ground Clamp and clean clamping surfaces if necessary.
Check Ground Clamp attachment at Welder for tight connection.
Wire Slipping in Drive Roller
Tighten Driver Roller Tensioner.
Wrong Size or Worn Contact Tip
Replace the Contact Tip for one of correct size or new condition.
Shielding Gas
Not Flowing Out
of MIG Gun
Gas Regulator or Gas Bottle Valve not
Opened Enough
Ensure the gas bottle valve is fully opened and open the Gas Regulator Knob
further to allow more gas flow through.
Gas Cylinder Empty
Refill the welding gas bottle.
MIG Gun Connector not Fully Inserted into
Socket of Welder.
Loosen MIG Gun Thumb Screw and full insert the connector into the socket
before re-tightening the Thumb Screw. If insertion is difficult, lubricate the
O-rings with a silicon based lubricant or dish soap.
O-rings on MIG Gun Damaged or Missing Replace MIG Gun O-rings.
Gas Leaking From Hose or Fittings
Tighten fittings or replace damaged parts as necessary.
Gas Diffuser Plugged with Spatter
Replace Gas Diffuser.
Содержание MP200i
Страница 1: ...AC DC MP200i WELDER ASSEMBLY AND OPERATING INSTRUCTIONS Item 65375 ...
Страница 31: ...To order parts and supplies 800 343 9353 eastwood com 31 DATA CHART ...
Страница 38: ...38 Eastwood Technical Assistance 800 343 9353 tech eastwood com NOTES ...
Страница 39: ...To order parts and supplies 800 343 9353 eastwood com 39 NOTES ...