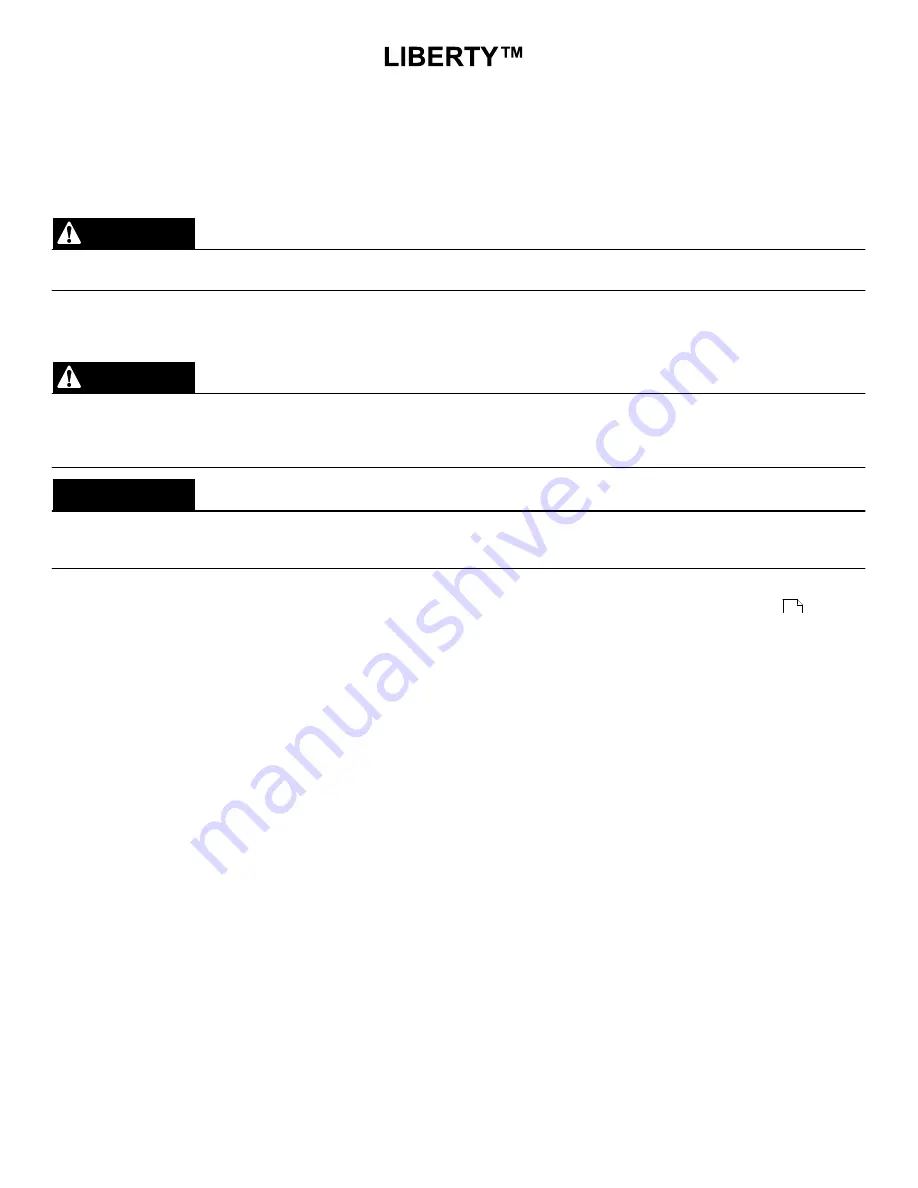
Issued May 2020
Maintenance and Adjustment
Copyright 2020, Heil Environmental
Printed in the U.S.A.
Maintenance and Adjustment
84
DRAIN AND CLEAN THE HYDRAULIC OIL TANK
Change the hydraulic oil when the oil sample shows to change it.
Remember that almost all hydraulic system malfunctions can be traced to dirt in the fluid. When working with the hydraulic
system, the hands, tools, working area and parts must be as clean as possible.
CAUTION
Wear proper eye protection when you are working on or around hydraulic lines or components. Wear proper eye
protection and avoid contact with hydraulic oil if possible. Never check for oil leaks with your hands.
To drain and clean the hydraulic oil tank, follow these steps:
1. Disengage the pump, shut off the engine and remove the ignition key.
WARNING
Make sure the unit is in the Lock-Out/Tag-Out mode when you do maintenance or service procedures, or when you go in
the hopper, climb in or on the body or on equipment. Equipment can be operated when the unit is not in the Lock-Out/Tag-
Out mode. When the unit is not in the Lock-Out/Tag-Out mode, equipment operated while you do maintenance or service
procedures, go in the hopper or climb in or on the body or on equipment can cause serious injury or death.
NOTICE
If your employer or company has Lock-Out/Tag-Out procedures that are different from the following procedures, use your
employer’s or company’s procedures. If your employer or company does not have Lock-Out/Tag-Out procedures, use the
procedures that follow.
2. Contact your supervisor if you have any questions about Lock-Out/Tag-Out procedures. If your supervisor has any
questions, that person can contact ESG Technical Service. Perform the
.
3. Remove the fill cap from the top of the tank.
4. Remove the drain plug from the bottom of the tank so that the oil drains into a container.
5. While fluid is draining from the tank, remove and replace the filter/breather assembly. Change the assembly every
time the in-tank filter is replaced.
6. To drain the entire hydraulic system, disconnect all hoses at the adapter and drain the hoses into a container.
7. Remove and replace the in-tank filter as described in
Change the Hydraulic Oil Filter
.
8. Remove the outlet flange and 100 mesh suction strainer to gain access to the tank inside.
9. Remove sediment from the tank bottom.
10.Install the outlet flange with a new gasket and the 100 mesh suction strainer into the tank.
11.Install the drain plug in the tank bottom.
12.Reconnect and tighten all hose connections that were disconnected.
15
Содержание HEIL LIBERTY TP1L-SM-0520
Страница 6: ...NOTES Issued May 2020 Copyright 2020 Heil Environmental Printed in the U S A ...
Страница 8: ...2 NOTES Issued May 2020 General Information Copyright 2020 Heil Environmental Printed in the U S A ...
Страница 43: ...Issued May 2020 Pumps Copyright 2020 Heil Environmental Printed in the U S A Pumps 37 SECTION 2 PUMPS ...
Страница 48: ...42 NOTES Issued May 2020 Lift Arm Copyright 2020 Heil Environmental Printed in the U S A ...
Страница 49: ...Issued May 2020 Lift Arm Copyright 2020 Heil Environmental Printed in the U S A Lift Arm 43 SECTION 3 LIFT ARM ...
Страница 80: ...74 NOTES Issued May 2020 Maintenance and Adjustment Copyright 2020 Heil Environmental Printed in the U S A ...
Страница 98: ...92 NOTES Issued May 2020 Body Controller Software Copyright 2020 Heil Environmental Printed in the U S A ...
Страница 110: ...104 NOTES Issued May 2020 Schematics Copyright 2020 Heil Environmental Printed in the U S A ...
Страница 111: ...Issued May 2020 Schematics Copyright 2020 Heil Environmental Printed in the U S A Schematics 105 SECTION 9 SCHEMATICS ...
Страница 112: ......
Страница 113: ......
Страница 114: ......
Страница 115: ...2 15 2018 Rev A2 ...
Страница 116: ...REV ...
Страница 117: ...REV ...
Страница 124: ......
Страница 131: ...Issued May 2020 Schematics Copyright 2020 Heil Environmental Printed in the U S A Schematics 125 ...
Страница 132: ...126 NOTES Issued May 2020 Schematics Copyright 2020 Heil Environmental Printed in the U S A ...