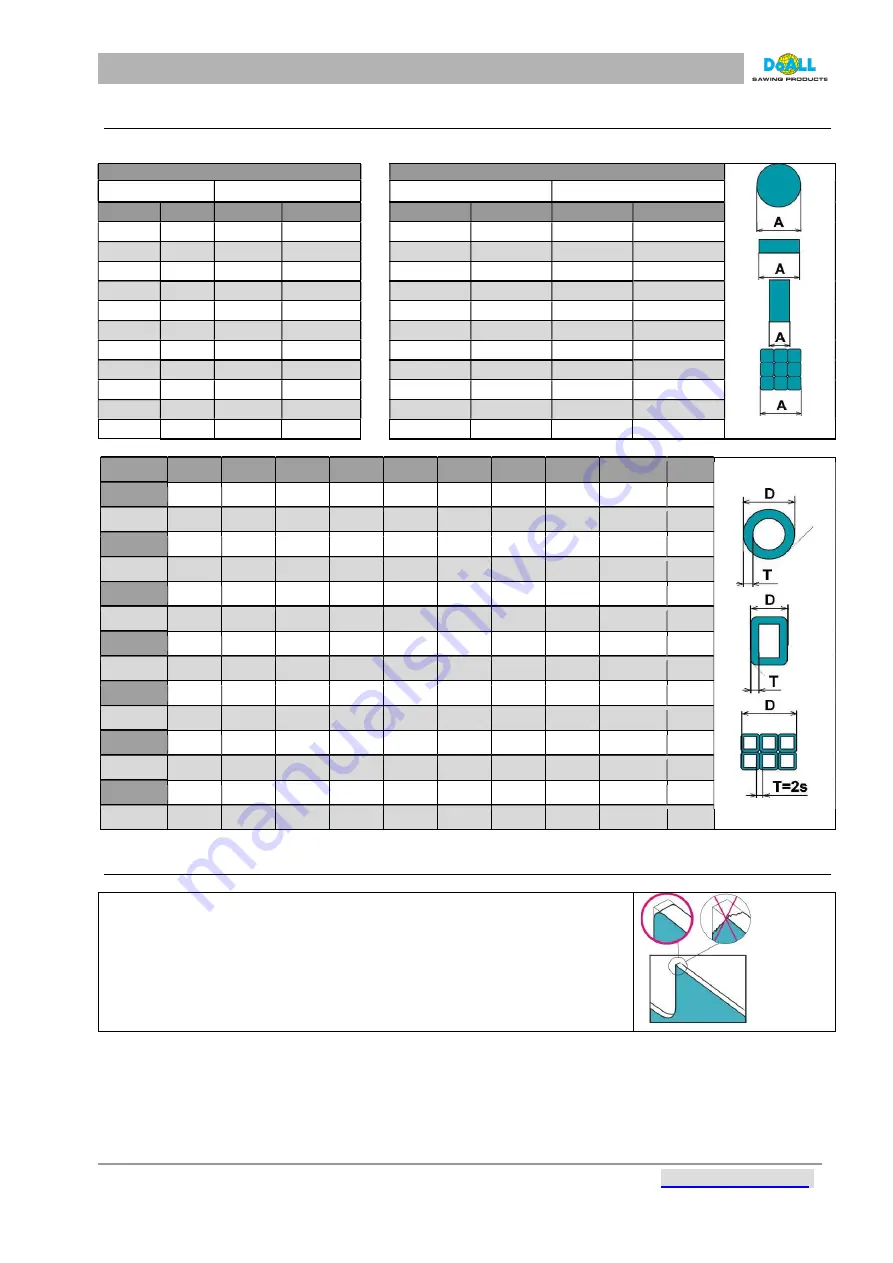
DS-320SA
Instruction Manual
- 50 -
www.doallsaws.com
12.2
HOW TO CHOOSE THE RIGHT TEETH FOR CUTTING
The table for choosing saw-blade is attached to the machine.
CONSTANT
VARIABLE
CONSTANT
VARIABLE
A
teeth
A
teeth
A
teeth
A
teeth
-0,25
22
-0,8
6/10
-0,6
14
- 0,6
10/14
0,25-0,4
18
0,8-1,6
5/8
0,6-1,6
10
0,6 – 1,6
8/12
0,4-0,8
14
1,6-3,2
4/6
1-2
8
1 – 2
6/10
0,8-1,2
10
3,2-6,5
3/4
1,4-2,8
6**
1,4 – 2,8
5/8
1,2-2
8
6,5-8
2/3
1,6-3,2
4**
1,6 – 3,2
5/6
2-3,2
6
8-16
1,4/2
2-4,7
3**
2 – 4,7
4/6 * **
3,2-4,8
4
16-25
1/1,3
3,2-7
2
3,2 – 7
3/4 * **
4,8-8
3
> 25
0,75/1,25
5-14
1,25
5 – 14
2/3
8-16
2
6-18
0,75
6 – 18
1,5/2
16-32
1,25
8-24
8 – 24
1,1/1,6
> 32
0,75
>20
> 20
0,75/1,25
tab. 12-1
T/D
0,8
1,6
2,4
3,2
4
4,8
6
8
12
20
0,08
14
10/14
10/14
10/14
10/14
8/12
8/12
8/12
8/12
5/8
0,12
14
10/14
10/14
8/12
8/12
8/12
8/12
6/10
6/10
5/8
0,16
10/14
10/14
8/12
8/12
8/12
6/10
6/10
5/8
5/8
4/6 S
0,2
10/14
10/14
8/12
8/12
6/10
6/10
5/8
4/6 S
4/6 S
4/6 S
0,24
10/14
8/12
8/12
6/10
6/10
5/8
5/8
4/6 S
4/6 S
4/6 S
0,32
10/14
8/12
8/12
6/10
5/8
5/8
4/6
4/6
4/6
4/6
0,4
8/12
6/10
5/8
4/6
4/6
4/6
4/6
4/6
4/5
0,5
8/12
6/10
4/6
4/6
4/6
4/6
4/6
4/6
4/5
0,6
8/12
6/10
4/6
4/6
4/6
4/6
4/5
4/5
4/5
0,8
4/6
4/6
4/6
4/6
4/6
4/5
4/5
3/4
1,2
4/6
4/6
4/5
4/5
4/5
4/5
2/3
2
4/5
3/4
2/3
2/3
3
3/4
2/3
2/3
> 4
2/3
1,5/2
tab. 12-2
12.3
RUN IN OF SAW-BLADE - WHEN HAVING A NEW SAW-BLADE
Run in is necessary
for achieving max. saw-blade life cycle. By running in
you prevent breaking microfragments of teeth, that damage other teeth and
increase stress to the saw-blade.
Let saw-blade run on no-load for about 30 seconds with the coolant pump
working ( due to right lubrication of saw-blade). Run in do if possible with easy
machined materials by min. speed of arm when cutting. After about 30
minutes increase the speed of feed continuously.