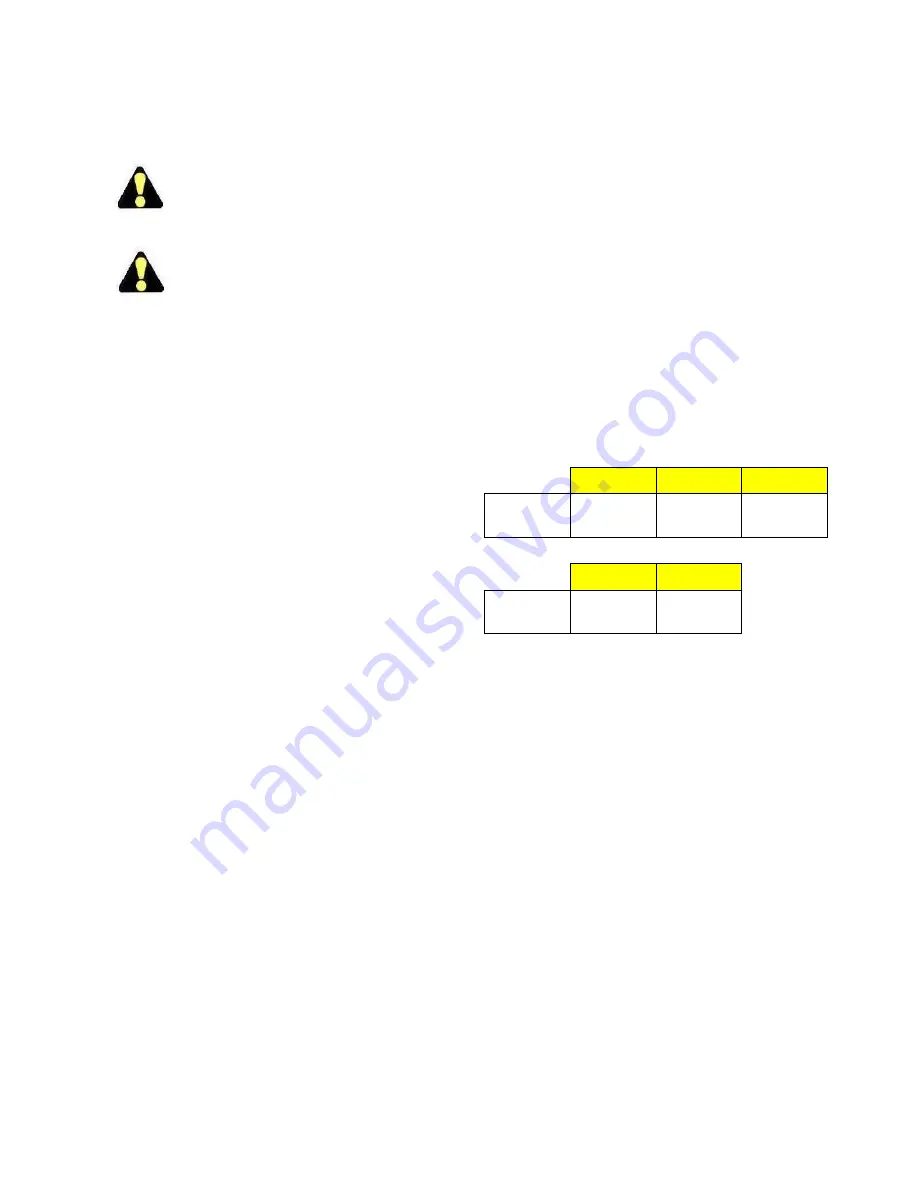
35
MAINTENANCE
REPLACING SAW GUIDE AND BACK‐UP INSERTS
These instructions can be used to replace
the saw guide inserts and back‐up rollers or
inserts on both saw guide arms.
The band drive motor must NOT be running
when replacing saw guide and back‐up
inserts or rollers.
1.
Loosen the insert adjustment screw on each saw
guide arm. Then: (a) remove the left saw band
guard (if necessary); (b) remove the adjustment
screw being very careful not to drop or lose the
insert, screw and washers; (c) loosen the socket cap
screw from the rear side of the saw guide arms and
remove the rear inserts.
2.
Thoroughly clean the saw guide arm and inserts
area. Then: (a) check the back‐up rollers or inserts
for wear and replace them in needed.
3.
Install the new fixed insert and tighten the screw.
Then: (a) thread the adjusting screw inward part
way; (b) install the adjustable insert; (c) tighten the
adjustment screw; (d) replace the left saw band
guard (if removed).
BAND DRIVE/BRUSH BELT REPLACEMENT
1.
To change the band drive belt, open the right band
wheel door. Then: (a) undo the guard clip and
remove the screws; (b) located in the rear of the
machine between the band drive motor and the
gearbox, turn adjustment knob counterclockwise to
relax belt tension; (c) remove the old belt and install
the new belt by stretching the belt over the desired
speed range set of pulley’s.
2.
Turn adjustment knob clockwise to tension the belt.
There should be very little deflection at the center
span of the belt.
3.
Flip the cover back up and engage the clip and
install the screws.
HYDRAULIC SYSTEM
1.
The machine’s hydraulic reservoir capacity depends
on machine model. Check the oil level daily by
referring to the side gauge located on the left side
of the machine behind the control console.
2.
Before changing the hydraulic oil: (a) lower the saw
head completely; (b) push the hydraulic stop button;
(c) place a container of sufficient capacity under the
drain port; (d) remove the drain plug; (e) allow the
reservoir to drain completely.
3.
Drain, clean and refill the reservoir. Change oil after
the first three months, and every six months
thereafter. Clean the suction strainer and filter
opening screen when necessary. Use high quality
hydraulic oil, type ISO‐VG 46.
System pressure
1.
Hydraulic system pressure is correctly set at the
factory and should not require adjustment for a
considerable period of time.
C‐3028NC
C‐4033NC
C‐420NC
System
pressure
30 bar
30 bar
40 bar
C‐5650NC
C‐560NC
System
pressure
40 bar
45 bar
COOLANT SYSTEM
1.
The machine’s coolant reservoir capacity depends
on machine model. A reservoir level sight gauge is
located at the machine’s right front side.
2.
Check the coolant often for signs of contamination
or breakdown. The reservoir and coolant system
should be drained and cleaned thoroughly when
the cutting fluid becomes undesirable for further
use. If another type of coolant is to be used, the
entire system must be flushed using DoALL Kleen
Flush.
3.
To thoroughly clean the reservoir section below the
conveyor trough, removal of the trough will be
necessary.
4.
Fill the reservoir with coolant through the conveyor
screw until the
red
marking line in the side gauge.
Содержание C-3028NC Boxed
Страница 2: ......
Страница 3: ......
Страница 11: ...6 MACHINE DIMENSIONS Continued C 3028NC DIMENSIONS...
Страница 12: ...7 MACHINE DIMENSIONS Continued C 3028NC Boxed DIMENSIONS...
Страница 13: ...8 MACHINE DIMENSIONS Continued C 4033NC DIMENSIONS...
Страница 14: ...9 MACHINE DIMENSIONS Continued C 420NC DIMENSIONS...
Страница 15: ...10 MACHINE DIMENSIONS Continued C 420NC BOXED DIMENSIONS...
Страница 16: ...11 MACHINE DIMENSIONS Continued C 5650NC DIMENSIONS...
Страница 17: ...12 MACHINE DIMENSIONS Continued C 560NC DIMENSIONS...
Страница 18: ...13 MACHINE DIMENSIONS Continued C 6260NC DIMENSIONS...
Страница 19: ...14 MACHINE FEATURES...
Страница 39: ...34 LUBRICATION DIAGRAM...