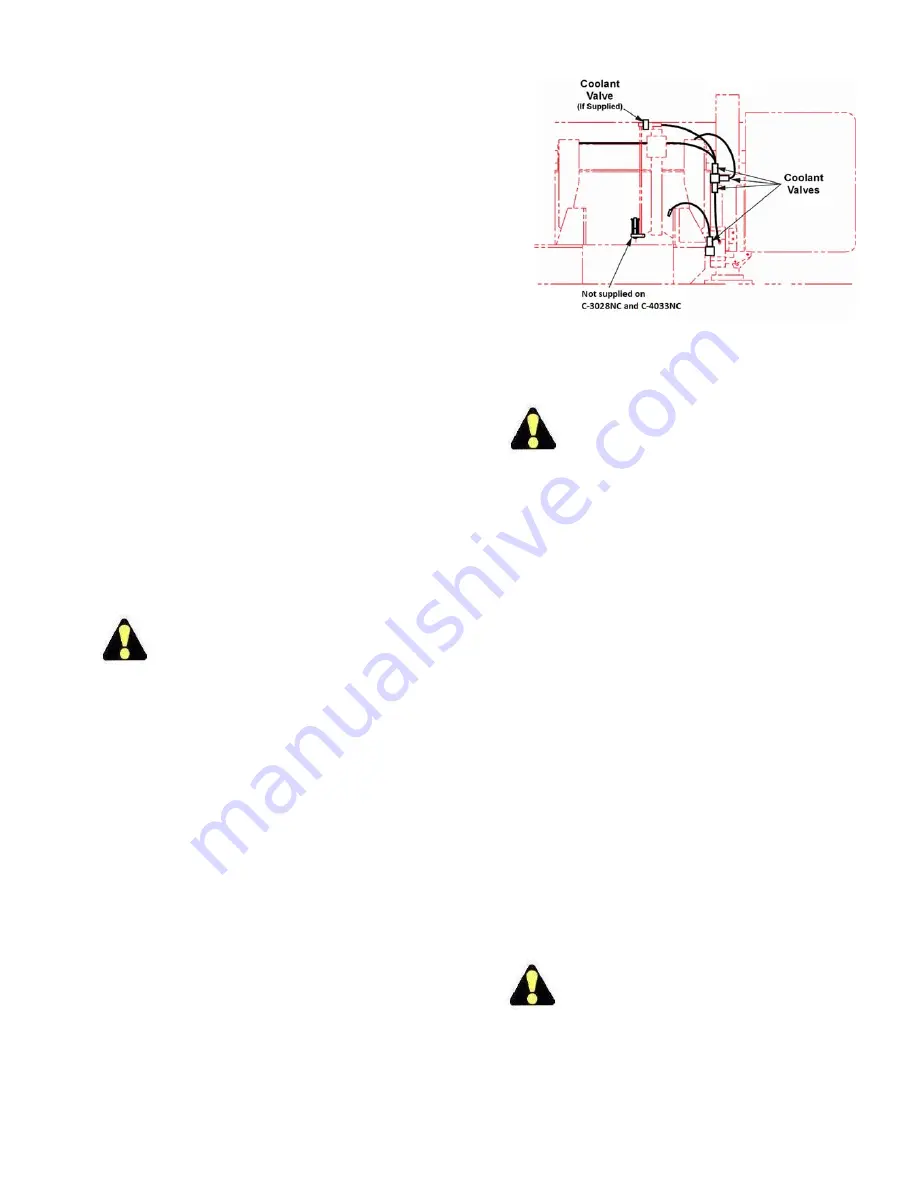
29
VERTICAL GUIDE ROLLERS
1.
These rollers are mounted near the end of the
index table and provides two laterally vertical
rollers.
2.
When the vertical roller is not needed, it can be
swiveled in the down position.
HYDRAULIC SYSTEM
1.
The hydraulic and band drive systems operate
independently. This allows the operator to perform
following tasks while the band drive motor is
not
running
: (a) change saw bands; (b) raise or lower
the saw head; (c) clamp or unclamp vises; (d)
position stock manually.
2.
The machine’s hydraulic reservoir capacity depends
on the machine model (see machine specifications
chart). Refer to the lubrication section of this
manual for recommended oils.
COOLANT SYSTEM
Coolant selection
1.
The main cause of tooth failure during band
machining is excessive heat built‐up. Using the
proper cutting fluid reduces the heat generated
during operation. It also helps the machine take
full advantage of its high‐speed steel saw bands.
Coolant application
Literature describing these and other coolant
types are available from your DoALL sales
representative.
1.
Coolant is applied as follows during sawing:
To the saw band and cutting area through the
saw guide inserts. Flow is regulated by a valve
on each saw guide arm.
To the band brush cleaning area through a
flushing nozzle. Flow is controlled by a valve.
To the cutting area through a flushing nozzle.
Flow is controlled by a valve.
An additional flexible flushing nozzle can apply
fluid where needed. Controlled by a valve.
2.
Coolant flow is started by: (a) pushing the hydraulic
start button; (b) turning the coolant selector to “I”
or “AUTO”; (c) tur all the coolant valves on until
fluids completely shrouds the saw band.
3.
Check the coolant reservoir level if flow is stopped
or reduced. Reservoir capacity depends on machine
model. A coolant level sight gauge is located at the
front right bottom of the machine base.
Coolant application points.
Coolant application points.
CHIP REMOVAL
DO NOT shovel or rake chips while the
saw band is running.
1.
Metal chips should be removed from the work area
as soon as possible. They can be washed or scraped
into the chip conveyor trough.
Band brush
1.
A covered, band drive motor driven band brush is
located near the right saw guide arm. During
machine operation, the brush bristles should be
positioned so that the tips clean chips from the
teeth tips, but should not contact the bottom of the
gullets. DO NOT allow metal chips to accumulate on
the brush.
2.
As the bristles wear, move the brush closer to the
blade. To do so: (a) open the right wheel cover; (b)
loosen the clamping handle; (c) position the brush
for correct blade cleaning; (d) tighten the clamp
handle and close the wheel door.
Flushing hose
1.
Metal chips and other debris may accumulate over
time around such areas as: saw guides, both band
wheels, vise, slide, brush housing, head lift cylinder,
feed and discharge areas, etc.
2.
The operator should check often for these
collections which can affect machine performance.
They should be removed with the flushing hose as
soon as possible.
The DoALL Company recommends using the
flushing hose to remove chips at least twice
per eight‐hour shift, and more often with
heavier use.
Содержание C-3028NC Boxed
Страница 2: ......
Страница 3: ......
Страница 11: ...6 MACHINE DIMENSIONS Continued C 3028NC DIMENSIONS...
Страница 12: ...7 MACHINE DIMENSIONS Continued C 3028NC Boxed DIMENSIONS...
Страница 13: ...8 MACHINE DIMENSIONS Continued C 4033NC DIMENSIONS...
Страница 14: ...9 MACHINE DIMENSIONS Continued C 420NC DIMENSIONS...
Страница 15: ...10 MACHINE DIMENSIONS Continued C 420NC BOXED DIMENSIONS...
Страница 16: ...11 MACHINE DIMENSIONS Continued C 5650NC DIMENSIONS...
Страница 17: ...12 MACHINE DIMENSIONS Continued C 560NC DIMENSIONS...
Страница 18: ...13 MACHINE DIMENSIONS Continued C 6260NC DIMENSIONS...
Страница 19: ...14 MACHINE FEATURES...
Страница 39: ...34 LUBRICATION DIAGRAM...