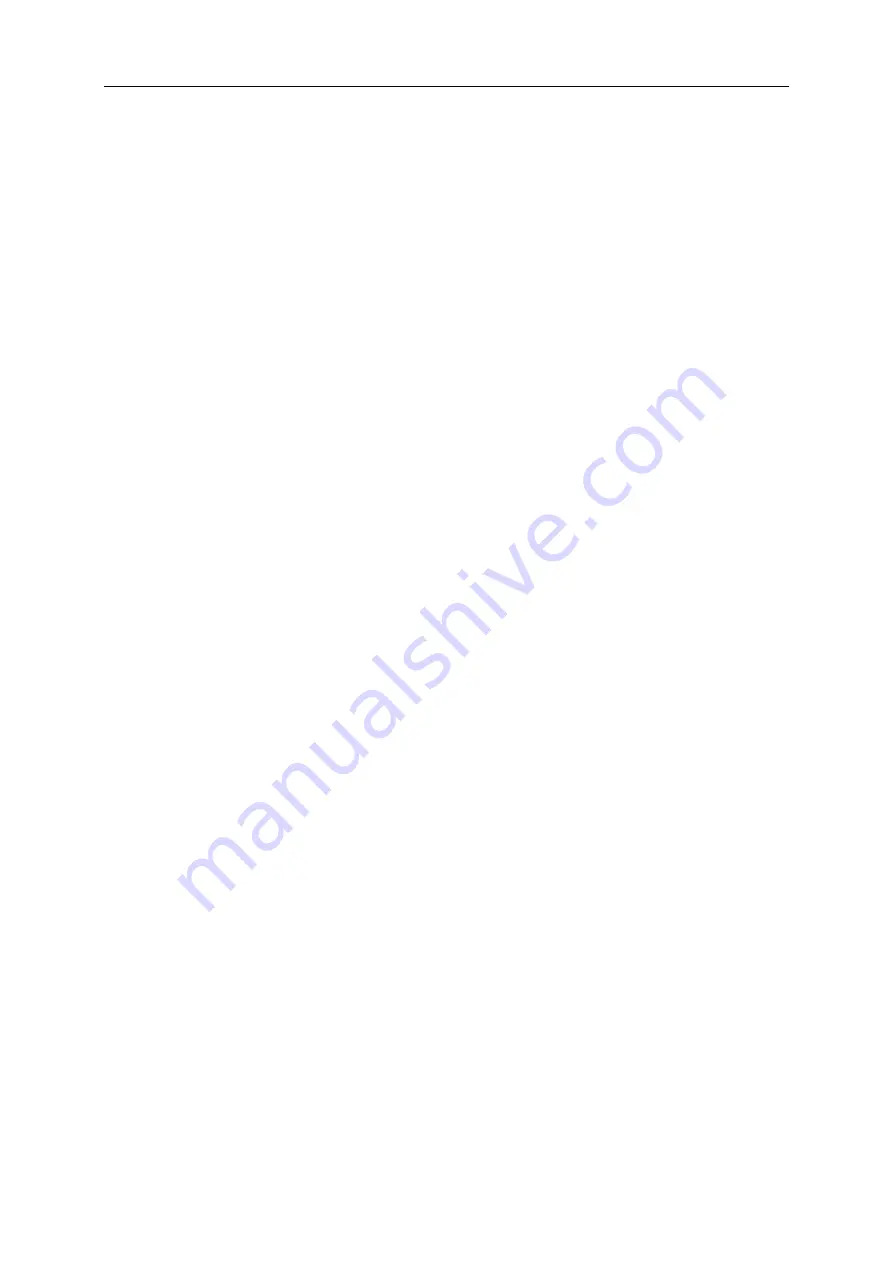
OPERATOR’S MANUAL
with Maintenance Information
Maintenance
44
Checklist A Procedures
A-1
Inspect the Manuals and Decals
Maintaining the operator’s manual in good
condition is essential to safe machine
operation. Manuals are included with each
machine and should be stored in the container
provided in the platform. An illegible or missing
manual will not provide safety and operational
information necessary for a safe operating
condition.
In addition, maintaining all of the safety and
instructional decals in good condition is
mandatory for safe machine operation. Decals
alert operators and personnel to the many
possible hazards associated with using this
machine. They also provide users with
operation and maintenance information. An
illegible decal will fail to alert personnel of a
procedure or hazard and could result in unsafe
operating conditions.
1 Check to make sure that the operator’s
manual is present and complete in the
storage container on the platform.
2 Examine the pages of manual to be sure
that they are legible and in good condition.
⊙
Result: The operator’s manual is
appropriate for the machine and the
manual are legible and in good condition.
¤
Result: The operator’s manual is not
appropriate for the machine or the manual
is not in good condition or is illegible.
Remove the machine from service until the
manual is replaced.
3 Open the operator’s manual to the decals
inspection section. Carefully and
thoroughly inspect all decals on the
machine for legibility and damage.
⊙
Result: The machine is equipped with all
required decals, and all decals are legible
and in good condition.
¤
Result: The machine is not equipped with
all required decals, or one or more decals
are illegible or in poor condition. Remove
the machine from service until the decals
are replaced.
4 Always return the manual to the storage
container after use.
Note: Contact your authorized DINGLI
distributor or DINGLI machinery if replacement
manuals or decals are needed.
Содержание S06-E
Страница 2: ......
Страница 4: ......
Страница 15: ...OPERATOR S MANUAL with Maintenance Information Decals 11 ...