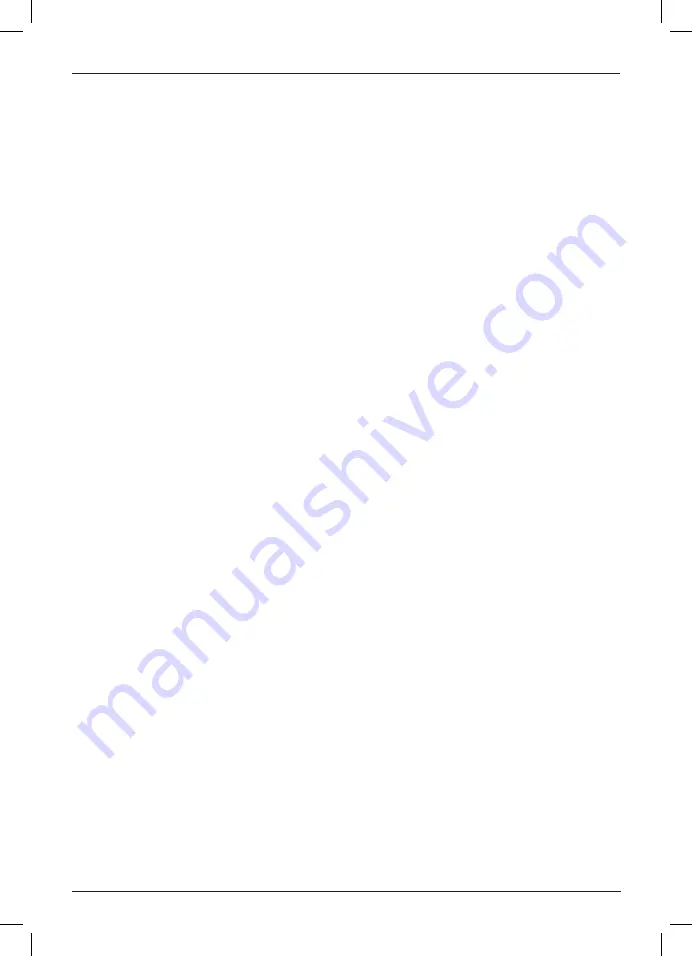
64
english
push harder which further loads the unit and
promotes twisting of the blade in the kerf.
Worn blades may also have insufficient body
clearance which increases the chance of
binding and increased loading.
5. RESTARTING A CUT WITH THE BLADE
TEETH JAMMED AGAINST THE MATERIAL
The saw should be brought up to full operating
speed before starting a cut or restarting a cut
after the unit has been stopped with the blade
in the kerf. Failure to do so can cause stalling
and kickback.
Any other conditions which could result in pinching,
binding, twisting, or misalignment of the blade could
cause kickback. Refer to the sections
Additional
Specific Safety Rules for Circular Saws
and
Blades
for procedures and techniques that will
minimize the occurrence of kickback.
Depth of Cut Adjustment (Fig. 6–8)
1. Raise the depth adjustment lever (X) to loosen.
2. To obtain the correct depth of cut, align the
appropriate mark on the depth adjustment
strap (AA) with notch (Y) on the upper blade
guard.
3. Tighten the depth adjustment lever.
4. For the most efficient cutting action using
a carbide tipped saw blade, set the depth
adjustment so that about one half of a tooth
projects below the surface of the wood to be
cut.
5. A method of checking for the correct cutting
depth is shown in Figure 8. Lay a piece of the
material you plan to cut along the side of the
blade, as shown in the figure, and observe how
much tooth projects beyond the material.
ADJUSTING DEPTH ADJUSTMENT LEVER (FIG. 7)
It may be desirable to adjust the depth adjustment
lever (X). It may loosen in time and hit the base plate
before tighten ing.
To Tighten the Lever:
1. Hold depth adjustment lever (X) and loosen the
locknut (Z).
2. Adjust the depth adjustment lever by rotating
it in the desired direction about 1/8 of a
revolution.
3. Retighten nut.
Bevel Angle Adjustment (Fig. 1, 9)
The bevel angle adjustment mechanism (H) can be
adjusted between 0° and 57°.
of the blade can dig into the top surface of the
material causing the blade to climb out of the kerf
and jump back toward the operator.
Kickback is more likely to occur when any of the
following conditions exists.
1. IMPROPER WORKPIECE SUPPORT
A. Sagging or improper lifting of the cut off
piece can cause pinching of the blade and
lead to kickback (Fig. 24).
B. Cutting through material supported at the
outer ends only can cause kickback. As the
material weakens it sags, closing down the
kerf and pinching the blade (Fig. 24).
C. Cutting off a cantilevered or overhanging
piece of material from the bottom up in a
vertical direction can cause kickback. The
falling cut off piece can pinch the blade.
D. Cutting off long narrow strips can cause
kickback. The cut off strip can sag or twist
closing the kerf and pinching the blade.
E. Snagging the lower guard on a surface
below the material being cut momentarily
reduces operator control. The saw can lift
partially out of the cut increasing the chance
of blade twist.
2. IMPROPER DEPTH OF CUT SETTING ON
SAW
To make the most efficient cut, the blade
should protrude only far enough to expose a
tooth as shown in Figure 8. This allows the
shoe to support the blade and minimizes
twisting and pinching in the material. See the
section titled
Depth of Cut Adjustment
.
3. BLADE TWISTING (MISALIGNMENT IN
CUT)
A. Pushing harder to cut can cause the blade
to twist.
B. Trying to turn the saw in the cut (trying to get
back on the marked line) can cause blade
twist.
C. Overreaching or operating the saw with poor
body control (out of balance), can result in
twisting the blade.
D. Changing hand grip or body position while
cutting can result in blade twist.
E. Backing up the saw to clear blade can lead
to twist.
4. USE OF DULL OR DIRTY BLADES
Dull blades cause increased loading of the
saw. To compensate, an operator will usually
Содержание DCS575
Страница 1: ...DCS575 DCS576 Final Page size A5 148mm x 210mm ...
Страница 3: ...1 Figure 1 T Q DCS576 S R H L K J DCS575 I M N D A E C F G B O P ...
Страница 4: ...2 D Figure 4 Figure 6 Figure 3 Figure 5 M K U L V Figure 7 Figure 2 X Y AA X W Z ...
Страница 5: ...3 Figure 9 Figure 8 Figure 10 G AC DCS575 DCS576 AD AB J J ...
Страница 6: ...4 Figure 11 Figure 12 AH AJ AI Figure 13 AG AG AG AF AE J N ...
Страница 7: ...5 AK AK AH DCS576 Figure 15 AL AH 100 mm 20 mm Figure 14 DCS576 ...
Страница 8: ...6 Figure 17 Figure 16 ...
Страница 9: ...7 Figure 18 Figure 20 AH AH 45 0 45 0 Figure 19 Figure 21 DCS576 DCS575 45 0 AM AM ...
Страница 10: ...8 Figure 24 Figure 23 C F Figure 22 ...
Страница 11: ...9 Figure 28 Figure 25 Figure 27 Figure 26 AN Figure 29 G AO F ...
Страница 12: ...10 Figure 30 AG ...