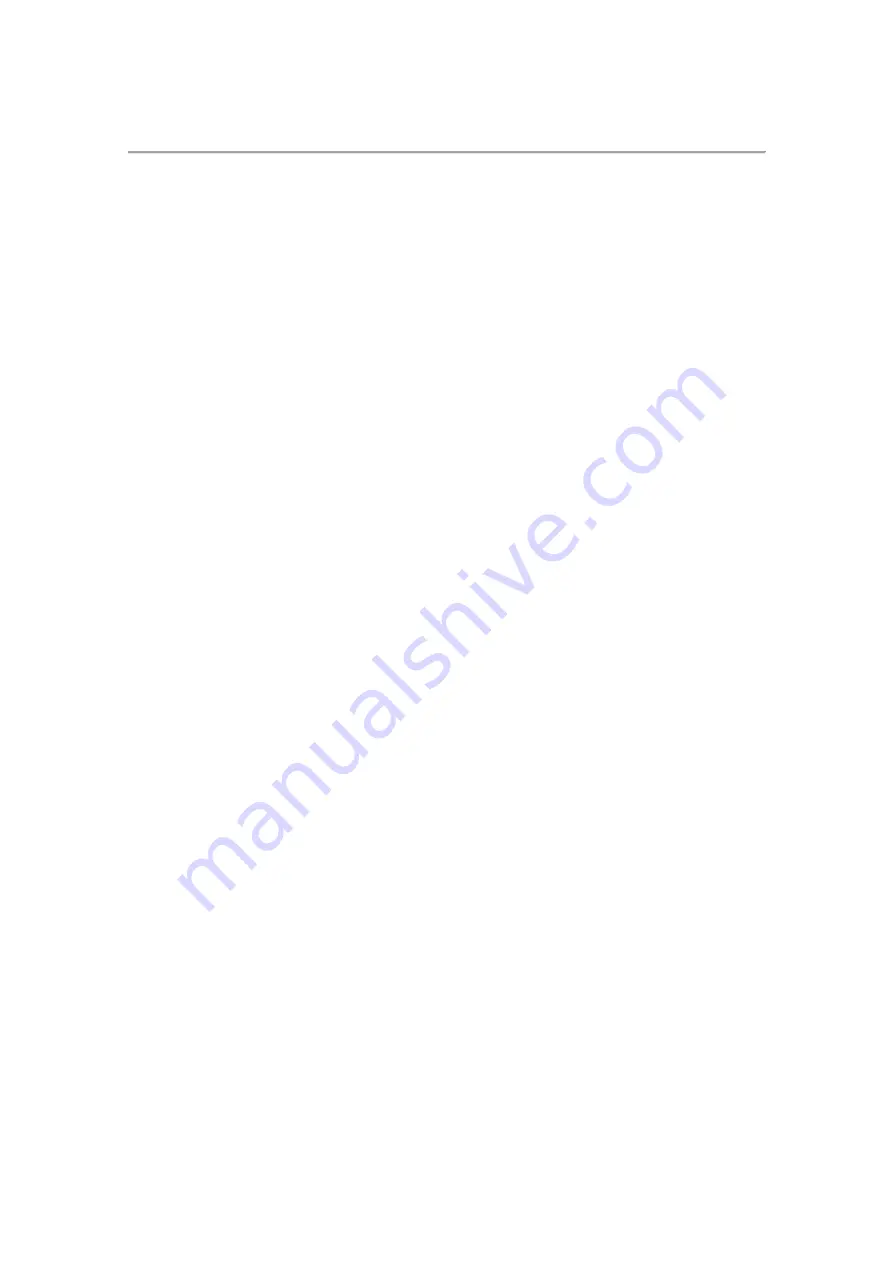
June, 2015
1-1
Preface
Thank you for purchasing our product. You can find the information related to take-out
arm for injection molding machine in this application note
during inspection, installation,
wiring, operation and examination.
The following information describes the purpose and application:
Control System (Chapter 1)
Operation (Chapter 2)
Program Usage and Editing (Chapter 3)
System Setting (Chapter 4)
Troubleshooting (Chapter 5)
Others (Chapter 6)
Examples (Chapter 7)
Product Features
Distributed fieldbus control: High precision and high speed motion, quick
response and can be easily constructed.
Built-in functions: Inhibited zone, protection in inner molding area, and
protection mechanism.
Smoothing function: Continuously smooth the interpolation.
Ejector protection: Protect the ejector when it moves forward.
Adaptive moving: Each axis can do adaptive moving with the setting of
torque limit.
Flexibly carry out stacking command
Template program: 10 program templates for customized setting
Provides huge amount of command program: With 1000 programs and up to
400 commands can be edited in one program.
Supports dual system
Technical Support
If you have any technical question, please contact local distributers or Delta
’s
service center.
Содержание HMC Series
Страница 2: ...HMC Take out Robot for Injection Molding Machine 2 June 2015 This page is intentionally left blank ...
Страница 6: ...HMC Take out Robot for Injection Molding Machine 6 June 2015 This page is intentionally left blank ...
Страница 18: ...HMC Take out Robot for Injection Molding Machine 18 June 2015 For protecting the circuit please connect right ...
Страница 22: ...HMC Take out Robot for Injection Molding Machine 22 June 2015 Power of Servo Drive Encoder GND 0V 24V HMC 4 ...
Страница 23: ...HMC Take out Robot for Injection Molding Machine June 2015 23 ...
Страница 24: ...HMC Take out Robot for Injection Molding Machine 24 June 2015 CN1 Homing Sensor Limit Sensor Brake ...
Страница 25: ...HMC Take out Robot for Injection Molding Machine June 2015 25 I O Board ...
Страница 26: ...HMC Take out Robot for Injection Molding Machine 26 June 2015 This page is intentionally left blank ...
Страница 33: ...HMC Take out Robot for Injection Molding Machine June 2015 33 System setting Password setting ...
Страница 39: ...HMC Take out Robot for Injection Molding Machine June 2015 39 ...
Страница 71: ...HMC Take out Robot for Injection Molding Machine June 2015 71 ...
Страница 89: ...HMC Take out Robot for Injection Molding Machine June 2015 89 This page is intentionally left blank ...
Страница 100: ...HMC Take out Robot for Injection Molding Machine 100 June 2015 This page is intentionally left blank ...