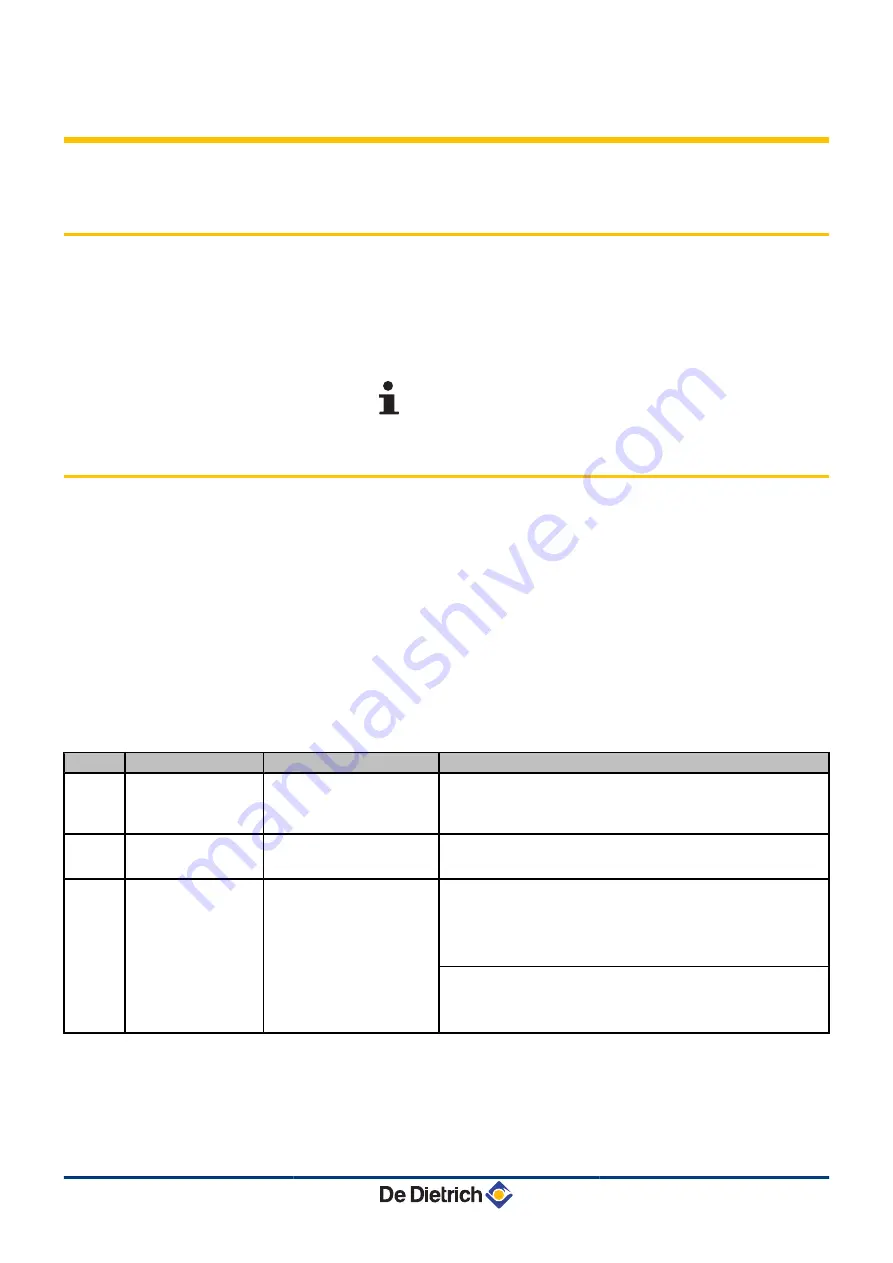
8 Troubleshooting
8.1
Anti-hunting
When the boiler is in Anti-short-cycle operating mode, the symbol
?
flashes.
1. Press the "?" key.
The message
Operation assured when the restart temperature
will be reached
is displayed.
This message is not an error message but an item of
information.
8.2
Messages (Code type Bxx or Mxx)
In the case of failure, the control panel displays a message and a
corresponding code.
1. Make a note of the code displayed.
The code is important for the correct and rapid diagnosis of the
type of failure and for any technical assistance that may be
needed.
2. Switch the boiler off and switch back on.
The boiler starts up again automatically when the reason for the
blocking has been removed.
3. If the code is displayed again, correct the problem by following the
instructions in the table below:
Code
Messages
Description
Checking / solution
B00
BL.PSU ERROR
The PSU PCB is incorrectly
configured
Parameter error on the PSU PCB
4
Set the type of generator again in the menu
#CONFIGURATION
(Refer to the original rating plate)
B01
BL.MAX BOILER
Maximum flow temperature
exceeded
The water flow in the installation is insufficient
4
Check the circulation (direction, pump, valves)
B02
BL.HEATING
SPEED
The increase in flow
temperature has exceeded
its maximum limit
The water flow in the installation is insufficient
4
Check the circulation (direction, pump, valves)
4
Check the water pressure
4
Check the cleanliness of the heat exchanger
Sensor error
4
Check that the sensors are operating correctly
4
Check whether the boiler sensor has been correctly fitted
AGC 10/15 - AGC 15 - AGC 25 - AGC 35
8. Troubleshooting
20/01/2012 - 300026081-001-B
103
Содержание AGC 10/15
Страница 7: ...20 01 2012 300026081 001 B 5 ...
Страница 130: ...9 Spare parts AGC 10 15 AGC 15 AGC 25 AGC 35 128 20 01 2012 300026081 001 B ...
Страница 131: ......