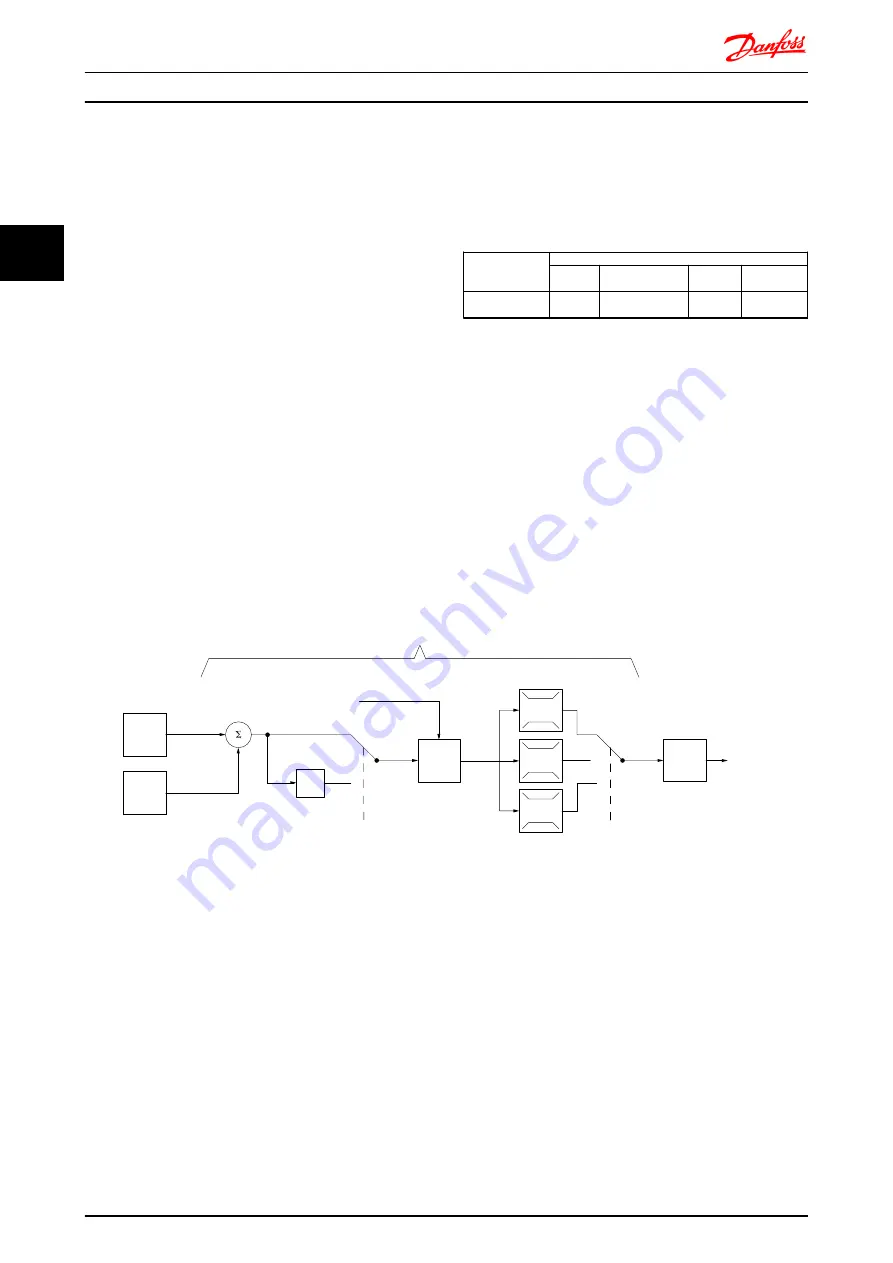
For incremental encoders the Encoder Resolution is found
in either
5-70 Term 32/33 Pulses per Revolution
(24V HTL on
standard drive) or
17-11 Resolution (PPR)
(5V TTL on
MCB102 Option).
Generally the practical maximum limit of
30-83 Speed PID
Proportional Gain
is determined by the encoder resolution
and the feedback filter time but other factors in the
application might limit the
30-83 Speed PID Proportional
Gain
to a lower value.
To minimize the overshoot,
7-03 Speed PID Integral Time
could be set to approx. 2.5 sec. (varies with the
application).
7-04 Speed PID Differentiation Time
should be set to 0 until
everything else is tuned. If necessary finish the tuning by
experimenting with small increments of this setting.
3.4.3 Process PID Control
The Process PID Control can be used to control application
parameters that can be measured by a sensor (i.e.
pressure, temperature, flow) and be affected by the
connected motor through a pump, fan or otherwise.
The table shows the control configurations where the
Process Control is possible. When a Flux Vector motor
control principle is used, take care also to tune the Speed
Control PID parameters. Refer to the section about the
Control Structure to see where the Speed Control is active.
1-00 Configu-
ration Mode
1-01 Motor Control Principle
U/f
VVC
plus
Flux
Sensorless
Flux w/ enc.
feedb
[3] Process
N.A.
Process
Process &
Speed
Process &
Speed
NOTE
The Process Control PID will work under the default
parameter setting, but tuning the parameters is highly
recommended to optimise the application control
performance. The two Flux motor control principles are
specially dependant on proper Speed Control PID tuning
(prior to tuning the Process Control PID) to yield their full
potential.
P 7-30
normal/inverse
PID
P 7-38
*(-1)
Feed forward
Ref.
Handling
Feedback
Handling
% [unit]
% [unit]
%
[unit]
%
[speed]
Scale to
speed
P 4-10
Motor speed
direction
To motor
control
Process PID
130BA178.10
_
+
0%
-100%
100%
0%
-100%
100%
Illustration 3.6 Process PID Control diagram
Introduction to FC 300
FC 300 Design Guide
32
MG.33.BD.02 - VLT
®
is a registered Danfoss trademark
3
3
Содержание VLT AutomationDrive
Страница 1: ...MAKING MODERN LIVING POSSIBLE Design Guide VLT AutomationDrive ...
Страница 280: ...www danfoss com drives MG33BD02 130R0301 MG33BD02 Rev 2011 03 29 ...
Страница 281: ......