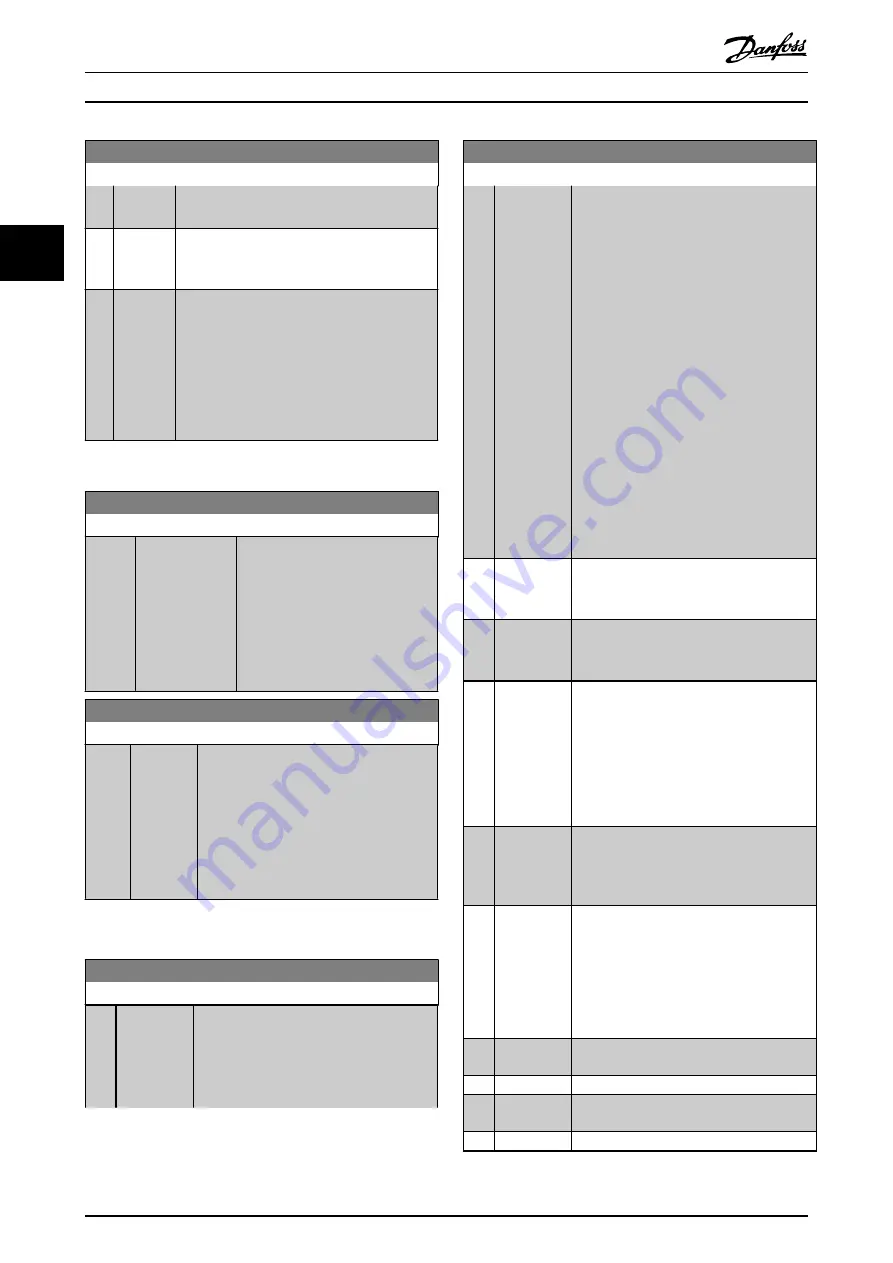
1-83 Precise Stop Function
Option:
Function:
has ramped up before you activate the speed
compensated stop.
[4]
Com cnt
stop w/rst
Same as [3] but after each precise stop the
number of pulses counted during ramp down to 0
rpm is reset.
[5]
Comp cnt
stop w/o r
Same as [3] but the number of pulses counted
during ramp down to 0 rpm is deducted from the
counter value entered in
.
You can for example use this reset function to
compensate for the extra distance done during
ramping down and to reduce the impacts of
gradual wear of mechanical parts.
This parameter cannot be adjusted while the motor is
running.
1-84 Precise Stop Counter Value
Range:
Function:
100000
*
[0 - 999999999 ] Enter the counter value to be used in
the integrated precise stop function,
.
The maximum permissible frequency
at terminal 29 or 33 is 110kHz.
Not used for selection [0] and [3] in
1-85 Precise Stop Speed Compensation Delay
Range:
Function:
10 ms
*
[0 - 100
ms]
Enter the delay time for sensors, PLCs, etc. for
use in
. In speed
compensated stop mode, the delay time at
different frequencies has a major influence on
the stop function.
Not used for selection [0], [1] and [2] in
3.3.9 1-9* Motor Temperature
1-90 Motor Thermal Protection
Option:
Function:
Thermal motor protection can be
implemented using a range of techniques:
•
Via a PTC sensor in the motor
windings connected to one of the
analog or digital inputs
1-90 Motor Thermal Protection
Option:
Function:
). See
3.3.1.1 PTC Thermistor Connection
•
Via a KTY sensor in the motor
winding connected to an analog
input (
See
.
•
Via calculation (ETR = Electronic
Thermal Relay) of the thermal load,
based on the actual load and time.
The calculated thermal load is
compared with the rated motor
current I
M,N
and the rated motor
frequency f
M,N
. See
and
.
•
Via a mechanical thermal switch
(Klixon type). See
.
For the North American market: The ETR
functions provide class 20 motor overload
protection in accordance with NEC.
[0]
*
No
protection
Continuously overloaded motor, when no
warning or trip of the frequency converter is
required.
[1]
Thermistor
warning
Activates a warning when the connected
thermistor or KTY-sensor in the motor reacts in
the event of motor over-temperature.
[2]
Thermistor
trip
Stops (trips) frequency converter when
connected thermistor or KTY sensor in the
motor reacts in the event of motor over-
temperature.
The thermistor cut-out value must be > 3 k
Ω
.
Integrate a thermistor (PTC sensor) in the
motor for winding protection.
[3]
ETR warning
1
Calculates the load when set-up 1 is active
and activates a warning on the display when
the motor is overloaded. Programme a
warning signal via one of the digital outputs.
[4]
ETR trip 1
Calculates the load when set-up 1 is active
and stops (trips) frequency converter when
the motor is overloaded. Programme a
warning signal via one of the digital outputs.
The signal appears in the event of a warning
and if the frequency converter trips (thermal
warning).
[5]
ETR warning
2
[6]
ETR trip 2
[7]
ETR warning
3
[8]
ETR trip 3
Parameter Descriptions
FC 300 Programming Guide
44
MG.33.MB.02 - VLT
®
is a registered Danfoss trademark
3
3
Содержание VLT AutomationDrive FC 300
Страница 1: ...MAKING MODERN LIVING POSSIBLE Programming Guide VLT AutomationDrive...
Страница 218: ...www danfoss com drives MG33MB02 130R0334 MG33MB02 Rev 2010 10 07...
Страница 219: ......