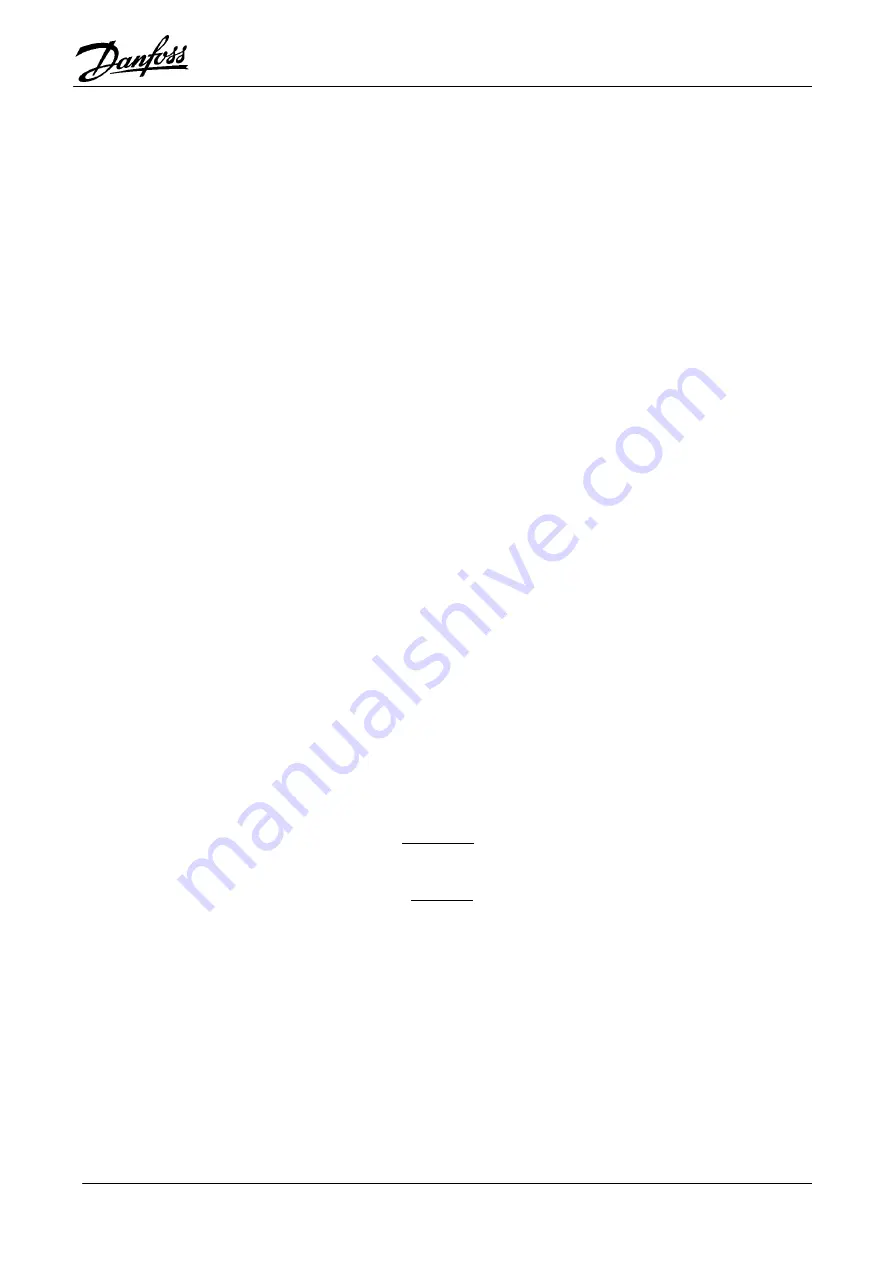
Synchronizing controller
56
MG.10.N4.02 - VLT is a registered Danfoss trademark
Then use the following procedure:
1. Start test run with virtual master by activating input 3. During test run you can read the
track error in the last value of the first display line. At stop the maximum track error
during the test run is read out.
2. If more accurate and dynamic control is required the P-portion (parameter 702) must be
increased. If the slave becomes unstable the value must be reduced to by approximately
25%.
3. Now set the D-portion (parameter 703) to 5 times the value of parameter 702
4. If a lower synchronizing error is required the I-portion (parameter 704) can be set to a
low value e.g. 10 but be careful a too high value will course overshoot and instability.
To store the optimized values:
Activate Input I4 (Store) or change first the value of parameter 710 to “1” .
How to program synchronization
Change the value of parameter 701 to “2”. This will start the synchronization program of VLT 5000
.
To do the synchronization programming you use the following parameters:
Parameter 725
Type of operation: Record “1” or “4” for position synchronization.
Parameter 729
Home function: Specify the start function of the drive:
“0” no defined position
“1” Home run must be carried out before the first start of synchronization
“2” Home run must be carried out before each start of synchronization.
Parameter 730 Home speed: Set the speed (% of maximum speed) at which Homing is to be
made. Positive values for clockwise rotation, negative values for counter-
clockwise rotation.
Parameter 731 Home acceleration: Set the acceleration (% of minimum acceleration) for
homing.
Parameter 733 Accuracy: Record a value (quad counts) for a tolerance within which the slave
position may deviate from the position of the master. With a negative value the
synchronizing error (parameter 797) show the error with a sign.
Parameter 734 Marker quantity Fault: Inaccuracy: Record the number of marker signals to
generate a Fault signal.
Parameter 735 Marker quantity Ready: Accuracy: Record the number of marker signals to
generate a Ready signal.
Parameter 737 Gear ratio No.: Record the number of the gear ratio that is to be displayed in
Parameters 738 to 739. First set the number of the gear ratio, then the
necessary values for this gear ratio can be set in Parameters 738 and 739.
The next gear ratio is then selected in Parameter 737 and the same procedure
is repeated.
Parameter 738 Gear ratio numerator: Enter here the numerator value of the gear ratio. The
value corresponds to the encoder pulses of the slave drive. To make fine
adjustment possible by means of inputs 32 and 33 a ratio of for example 7:16
must be programmed as 7000:16000.