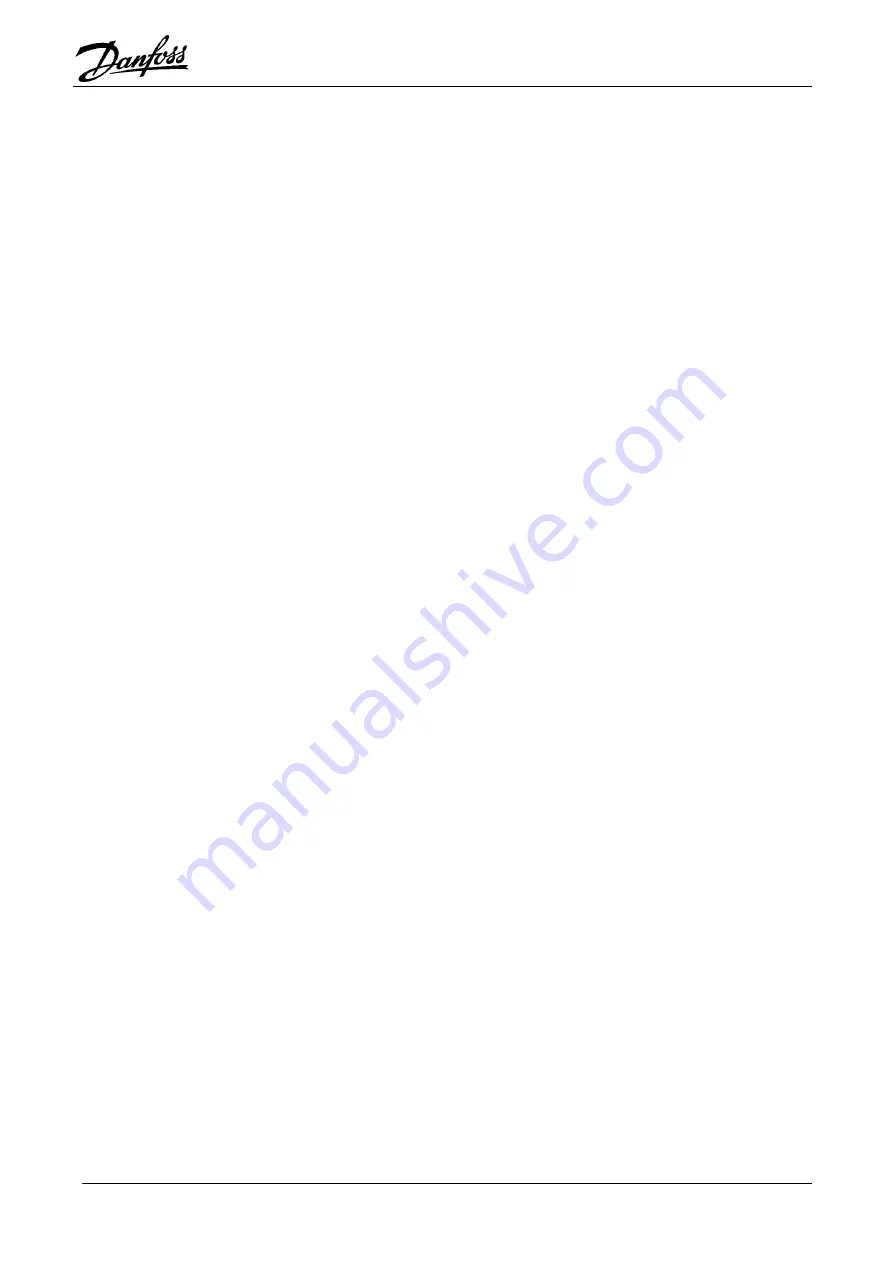
Synchronizing controller
54
MG.10.N4.02 - VLT is a registered Danfoss trademark
Parameter 718 Ramp type: Record “0” for linear ramp and “1” for s-ramp. Note: S-ramp
requires higher acceleration torque
Parameter 719 Maximum track error: Record the value that is to generate “Track error”
indication in the display, if exceeded. Input is in quad counts.
Parameter 720 Reversing behaviour: Record “0” if reversing is allowed, “1” if the slave must
always follow the direction of the master or “2” if reversing is not allowed.
How to check the motor connection
When you have programmed the above parameters you check the motor connection as follows:
1. Remove all signals to terminals 16-33 and I1-I8. Only input 27 must be connected and
closed.
2. Select “Local” function in Parameter 002. – VLT 5000 stops (display flashing)
3. Set the frequency for a low value, for example 3 Hz in parameter 003.
4. Press the [START] button on the VLT 5000 control panel and then the [STOP/RESET]
button watching the speed direction of the motor. If the motor rotates in the wrong
direction then exchange the motor phases.
Testing the incremental encoders
When you have tested the motor speed direction you test the incremental encoder connection as follows
1. Remove all signals to terminals 16-33 and I1-I8. Only Input 27 must be connected and closed.
2. Press the [DISPLAY/STATUS] button on the VLT 5000 control panel. Now the following values
appear in the upper line of the display: slave position, master position and track error.
3. Rotate the slave drive motor shaft manually in the allowed direction. Now the display shows an
ascending count of the slave position. If the count is descending, exchange the slave encoder track
A by B and A/ by B/. If there is no counting in the display then check the wiring of the encoder.
Follow the same procedure when you test the master encoder. Note: To be right the count must be
ascending here.
Remember to change parameter 002 back to “Remote” and start VLT 5000 by pressing the [START] button
on the control panel.
How to optimise the controller
Synchronization is obtained via two main elements of the controller: Velocity feed forward and
the PID controller.
NOTE: Before starting the optimizing procedures it is important to select the right type of
synchronization in parameter 728, in this example it must be “1” for position synchronization.
Please always have the necessary degree of accuracy in mind, you could go on optimizing for a
long time, but it might not be necessary to have a 100% accuracy in the application you are
dealing with.
First step is to optimise velocity feed forward this can be done via the automatic calculation
function:
Velocity feed forward calculation is activated by setting parameter 729 to “1”, remember to
make the required parameter settings according to the description of par. 729 before starting
the calculation. The calculation is done when the value of par. 729 returns to “0”.