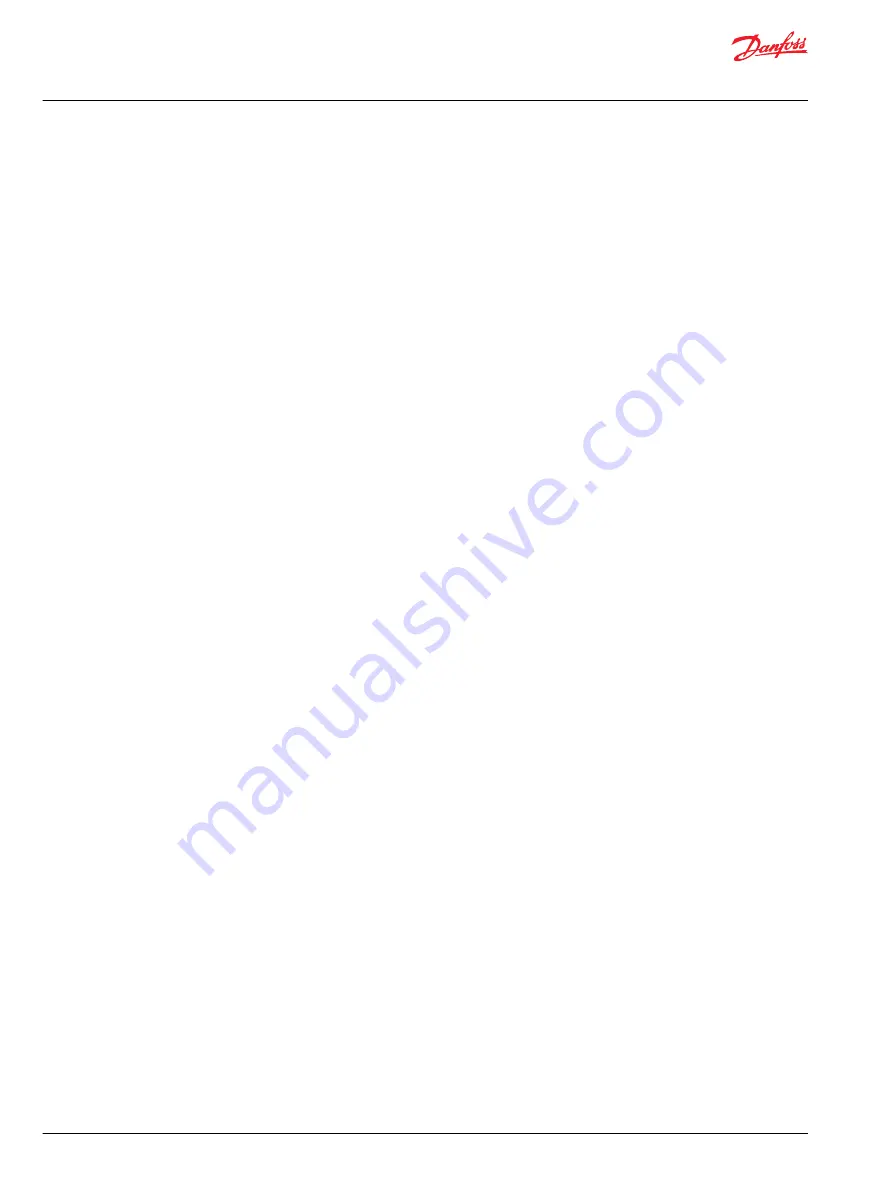
‒
Electric Displacement Control (EDC)
‒
Forward-Neutral-Reverse control (FNR)
‒
Non-Feedback Proportional Electric control (NFPE)
‒
Automotive Control (AC)
‒
Fan Drive Control (FDC)
‒
Manual Displacement Control (MDC)
‒
Control-Cut-Off valve (CCO)
•
High power density where all units utilize an integral electro-hydraulic servo piston assembly that
controls the rate (speed) and direction of the hydraulic flow.
•
Compatible with the Danfoss family of PLUS+1
®
micro-controllers for easy Plug-and-Perform
installation.
•
More compact and lightweight
•
Improved reliability and performance
Go to the Danfoss website or applicable product catalog to choose the components that are right for
your complete closed circuit hydraulic system.
Design
Danfoss H1 closed circuit piston pumps convert input torque into hydraulic power. The input shaft
transmits rotational force to the cylinder block. Bearings at the front and rear of the pump support the
shaft. Splines connect the shaft to the cylinder block. A lip-seal at the front end of the pump prevents
leakage where the shaft exits the pump housing. The spinning cylinder block contains nine reciprocating
pistons. Each piston has a brass slipper connected at one end by a ball joint. The block spring, ball guide,
and slipper retainer hold the slippers to the swashplate. The reciprocating movement of the pistons
occurs as the slippers slide against the inclined swashplate during rotation. Via the valve plate, one half of
the cylinder block is connected to low pressure and the other half to high pressure. As each piston cycles
in and out of its bore, fluid is replenished by charge flow and displaced to the outlet thereby imparting
hydraulic power into the system. A small amount of fluid is allowed to flow from the cylinder block/valve
plate and slipper/swashplate interfaces for lubrication and cooling. Case drain ports return this fluid to
the reservoir.
The angle of the swashplate controls the volume and direction of fluid displaced into the system. The
servo piston controls the angle of the swashplate. The pump control, by varying the pressure at the servo
piston, controls the piston’s position. An electric signal to the control coils transmits the command from
the operator to the pump. Mechanical feedback of the swashplate position to the control through the
feedback pins allows for very precise displacement control and increases overall system stability. Non-
feedback control options do not use the mechanical feedback link.
Service Manual
H1P 069—H1P 280 Axial Piston Single Pumps
Introduction
8 |
©
Danfoss | January 2021
AX152886482551en-000601