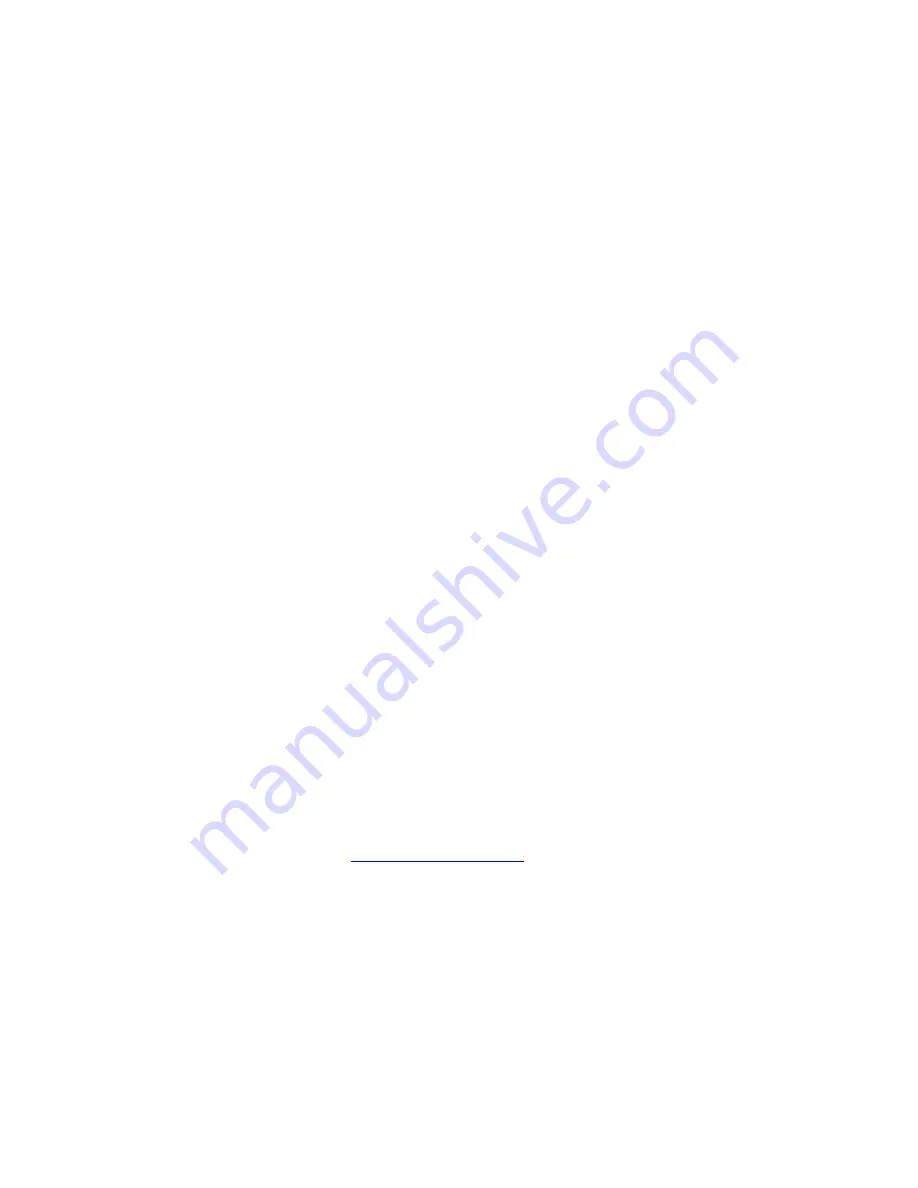
55
Planetary Final Drive Repair Instructions
Contact Information
With more than 100 years of experience, Fairfield Manufacturing
Co. Inc. has become the largest U.S. non-captive producer of
gears, custom gear assemblies, planetary final drives and related
gear products. Fairfield Manufacturing Co. Inc., headquartered in
Lafayette, Indiana USA, is distinguished by our extensive design,
manufacturing and applications engineering capabilities.
Our 500,000 square foot plant is a modern, fully equipped
manufacturing facility that includes a full service heat treat
department.
Our philosophy of synchronous engineering is a partnership that
matches our best and brightest people with your people to evaluate
your unique requirements, and develop products and assemblies
that meet your needs.
For more information, contact Fairfield Manufacturing Co Inc. today.
Mailing Address
Dana Incorporated
Off-Highway Drive and Motion Technologies
2400 Sagamore Parkway South / P.O. Box 7940
Lafayette, IN 47903 USA
Shipping Address
2309 Concord Road
Lafayette, IN 47909
Fax
Main
(765) 772-4001
Applications Engineering
(765) 772-4011
Sales and Service
(765) 772-4010
Applications Engineering
Sales
Website
www.grazianofairfield.com
Содержание Spicer Torque-Hub S350 Series
Страница 1: ...1 Torque Hub Planetary Final Drive S350 Series Service Manual Rev 04 11 13 ...
Страница 10: ...10 THIS PAGE INTENTIONALLY LEFT BLANK ...
Страница 11: ...11 DISASSEMBLY ...
Страница 16: ...16 THIS PAGE INTENTIONALLY LEFT BLANK ...
Страница 24: ...24 ASSEMBLY ...
Страница 43: ...43 Planetary Final Drive Service Manual Assembly Drawing ...
Страница 47: ...47 Planetary Final Drive Repair Instructions Assembly Tools T149933 LOCKNUT WRENCH ...
Страница 48: ...48 T158149 BEARING CUP PRESS TOOL ...
Страница 49: ...49 T170237 LEAK TEST ADAPTOR ...
Страница 50: ...50 T214147 ASSEMBLY PRESSING TOOL ...
Страница 51: ...51 T216332 ASSEMBLY PRESSING TOOL ...
Страница 52: ...52 T222390 LEAK TEST ADAPTER PLATE ...
Страница 53: ...53 T223131 LOCKNUT WRENCH ...
Страница 54: ...54 T223989 ROLL CHECKING TOOL ...