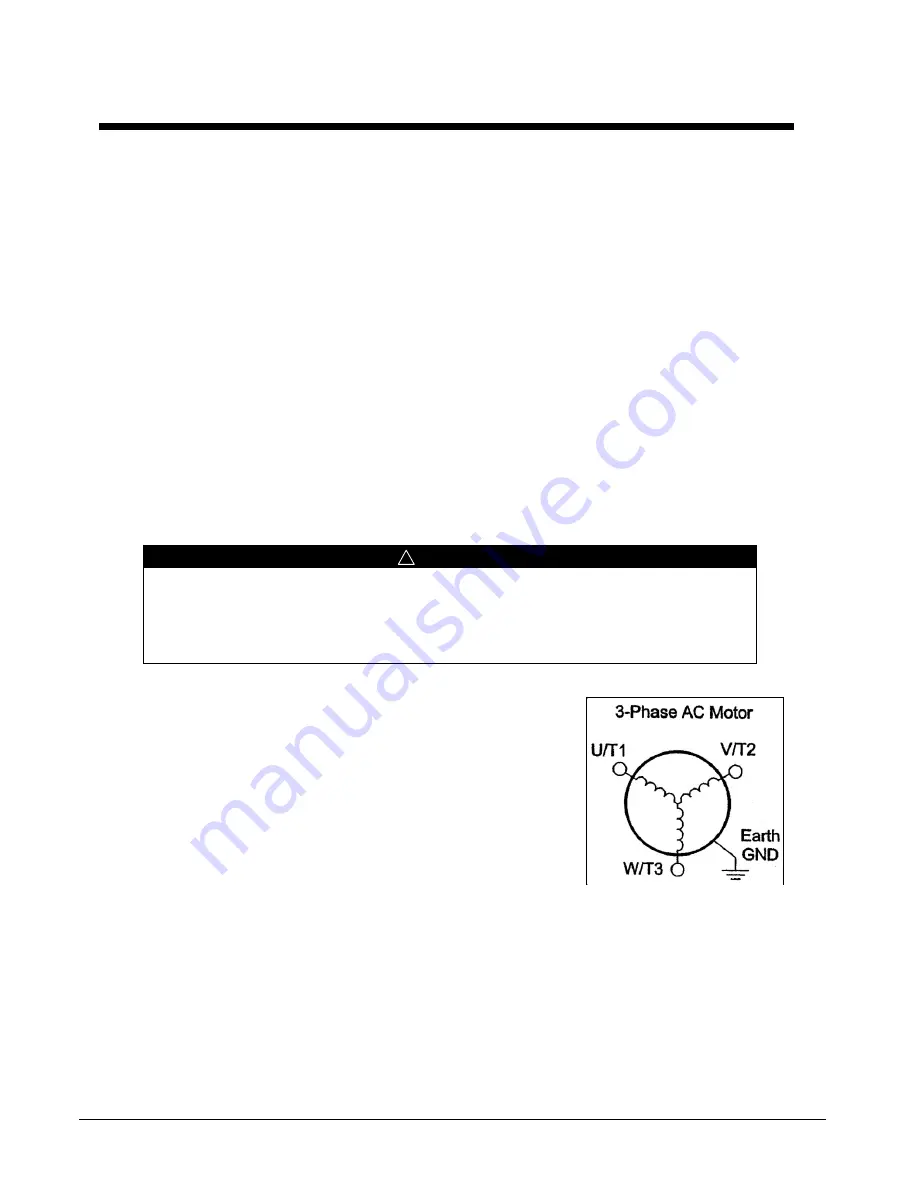
60
AGZ 025D through 190D
OMM 1166-1
Optional Low Ambient Fan VFD
The optional VFD fan control is used for unit operation below 35
F (2
C) down to a minimum of -10
F
(-23
C). The control looks at the saturated discharge temperature and varies the fan speed to hold the
temperature (pressure) at the “target” temperature.
Low ambient air temperature control is accomplished by using the Optional Low Ambient VFD to
control the speed of the first fan on each circuit. This VFD control uses a proportional integral function
to drive the saturated condenser temperature to a target value by changing the fan speed. The target
value is normally the same as the saturated condenser temperature target setpoint.
The fan VFD always starts when the saturated condenser temperature rises higher than the target.
What is an Inverter?
The term inverter and variable-frequency drive are related and somewhat interchangeable. An
electronic motor drive, for an AC motor, controls the motor’s speed by varying the frequency of the
power sent to the motor.
In general, an inverter is a device that converts DC power to AC power. The figure below shows how
the variable-frequency drive employs an internal inverter. The drive first converts incoming AC power
to DC through a rectifier bridge, creating an internal DC bus voltage. Then the inverter circuit converts
the DC back to AC again to power the motor. The special inverter can vary its output frequency and
voltage according to the desired motor speed.
Inverter Output to the Motor
!
WARNING
Avoid swapping any 2 of the 3 motor lead connections, which will cause reversal of the motor
direction. In applications where reversed rotation could cause equipment damage or personnel
injury, be sure to verify direction of rotation before attempting full-speed operation. For safety
to personnel, the motor chassis ground must be connected to the ground connection at the
bottom of the inverter housing.
The AC motor must be connected only to the inverter’s output terminals.
The output terminals are uniquely labeled (to differentiate them from the
input terminals) with the designations U/T1, V/T2, and W/T3. This
corresponds to typical motor lead connection designations T1, T2, and
T3. The consequence of swapping any two of the three connections is the
reversal of the motor direction. This must not be done. In applications
where reversed rotation could cause equipment damage or personnel
injury, be sure to verify direction of rotation before attempting full-speed
operation. For safety to personnel, the motor chassis ground must be
connected to the ground connection at the bottom of the inverter housing.
Notice the three connections to the motor do not include one marked “Neutral” or “Return.” The motor
represents a balanced “Y”
impedance to the inverter, so there is no need for a separate return. In other
words, each of the three “Hot” connections serves also as a return for the other connections because of
their phase relationship.
Do not to switch off power to the inverter
while the motor is running
(unless it is an emergency stop) to
avoid equipment damage. Also, do not install or use disconnect switches in the wiring from the inverter to
the motor (except thermal disconnect).
Содержание AGZ 190D
Страница 12: ...12 AGZ 025D through 190D OMM 1166 1 Figure 2 Typical Field Control Wiring...
Страница 81: ......
Страница 82: ......
Страница 83: ......