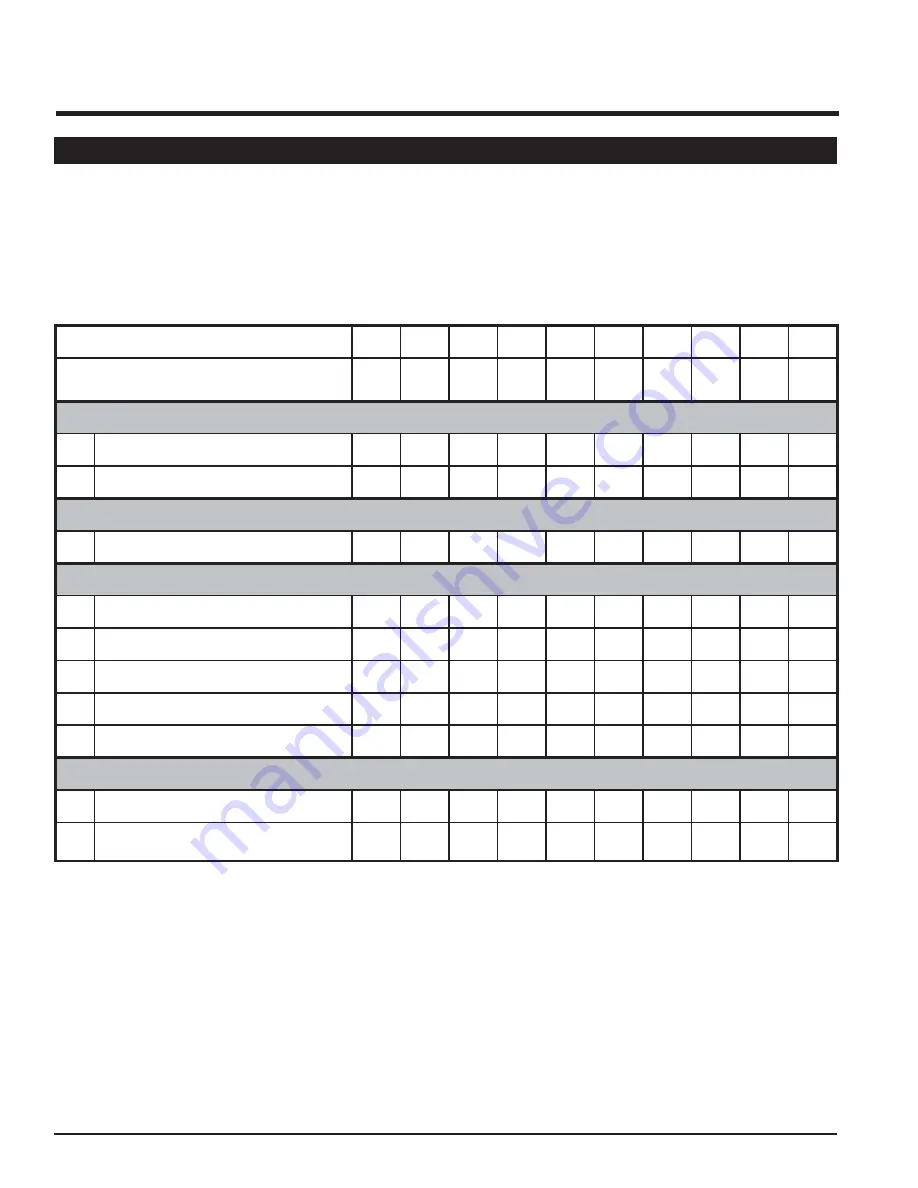
PN 12071 R122210
42
SERVICE & MAINTENANCE
Section
6
ACTION
CODE:
√
= CHECK OR INSPECT
CL = CLEAN
L = LUBRICATE
C = CHANGE
HOURS
SERVICED BY
DAILY
L
PTO CROSS JOURNAL ZERKS
√
GEARBOX OIL LEVEL
16 HOURS
L
PTO INNER TUBE
40 HOURS
L
PTO SHIELD RETAINING BEARING
L
PTO DISCONNECT MECHANISM
√
TENSION OF IDLER GEARS
√
FAN HOUSING AND AIRWAY
√
PLASTIC ECCENTRIC ROLLERS
YEARLY
C
GEARBOX OIL
√
CONDITION OF FRICTION DISC
TORQUE LIMITER (SLIP CLUTCH)
6.1 MAINTENANCE CHECKLIST
Along with a servicing interval, perform a visual inspection. Maintenance personnel can often detect potential problems
from any unusual sounds made by such components as shafts, bearings and drives.
These service recommendations are based on normal operating conditions. Severe or unusual conditions may require
more frequent attention. Copy this page to continue record.
Содержание Air Reel
Страница 14: ...PN 12071 R122210 10 ...
Страница 56: ......
Страница 57: ......
Страница 58: ......
Страница 59: ......