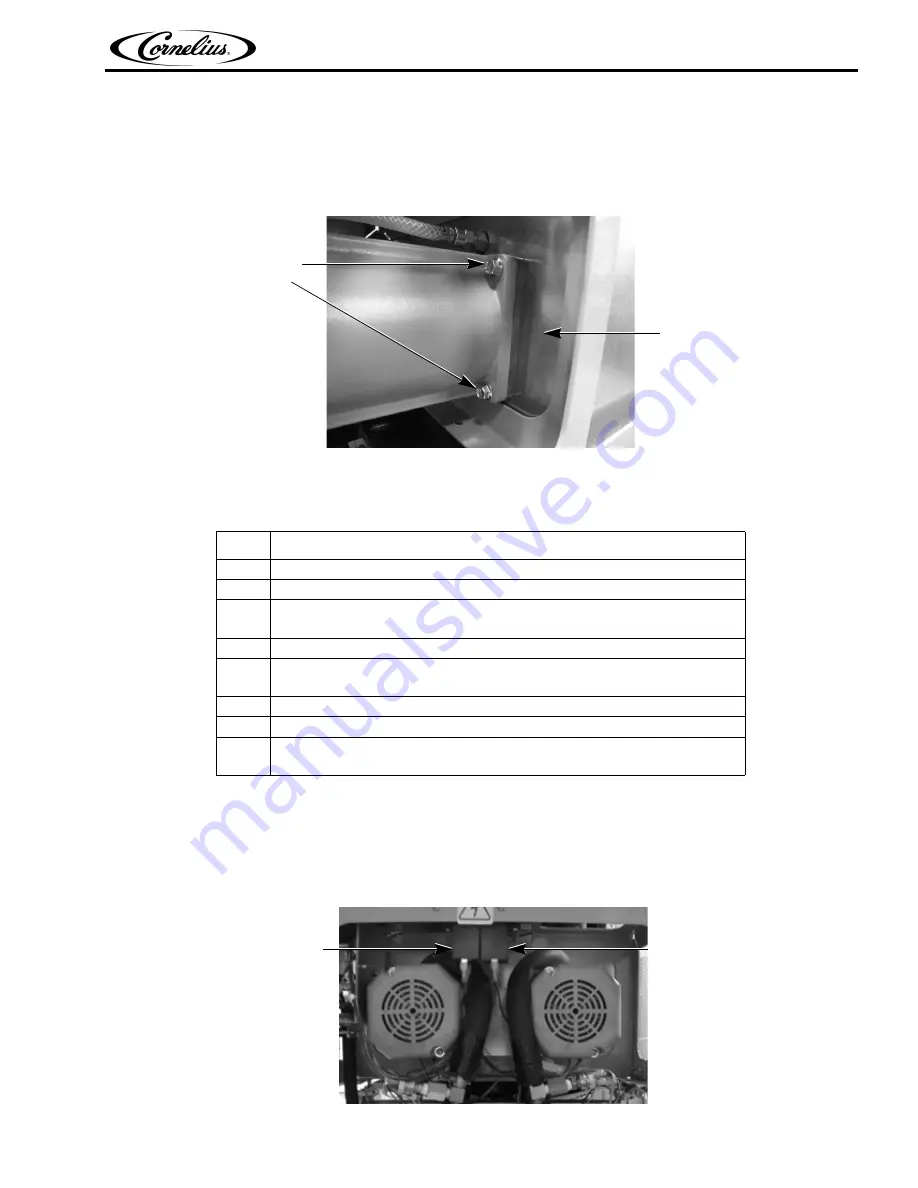
Viper Installation, Service & Decommissioning Manual
© 2022, Marmon Foodservice Technologies Inc.
- 89 -
Publication Number: 620073146SER
B
ARREL
M
OTOR
R
EPLACEMENT
The barrel motor does not require any special alignment when being replaced. It mounts on four (4) bolts. These bolts are
screwed into threaded bosses in the foam pack barrel assembly, as shown in Figure 70. To replace a barrel motor, perform
the procedure in Table 73
Figure 70. Side View of Motor Showing Two of the Four Mounting Bolts
M
OTOR
R
UN
C
APACITOR
R
EPLACEMENT
The motor run capacitors, shown in Figure 71, are mounted at the rear of the unit between the barrel motors. To replace a
run capacitor, perform the procedure in Table 74
Figure 71. View of Motor Run Capacitors
Table 73.
Step
Action
1
Perform the procedure in Steps 1 through 8 of Table 73
2
Disconnect the motor from the circuit by unplugging the connector.
3
Remove the motor by removing the four (4) bolts holding the motor to the barrel
assembly.
4
Install the replacement motor and connect the connector.
5
Replace the motor seal, scraper blade assembly onto the motor shaft in the barrel, as
described in Table 73
6
Reconnect power to the unit.
7
Refill the barrel with product. “Filling a Barrel” on page 67.
8
When barrel fill is complete, perform a motor calibration. “Calibrating a Motor” on
page 73.
Barrel Motor
Mounting
Bolts
Foam
Pack
Motor Run
Capacitor
Motor Run
Capacitor
Содержание R-454C
Страница 111: ...Cornelius Inc www cornelius com...